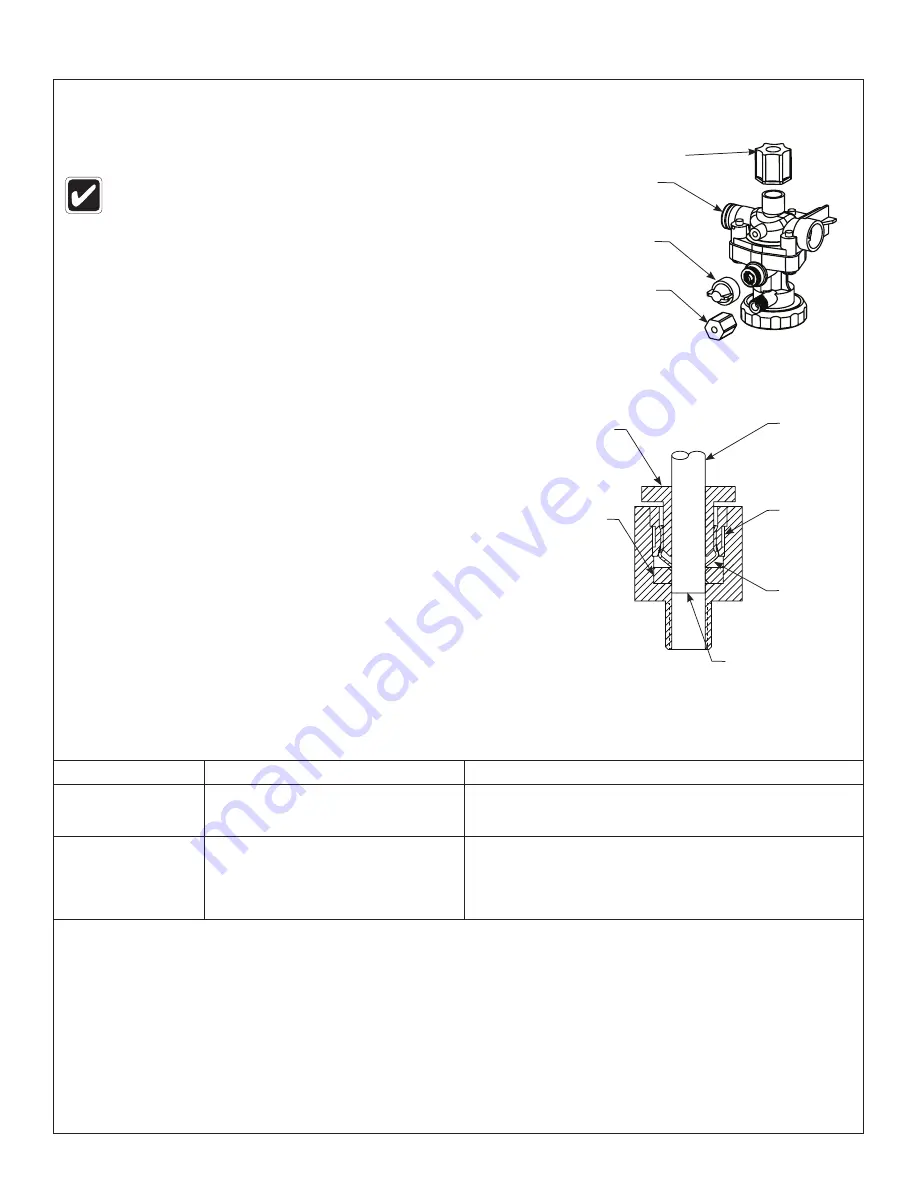
15
Bradley •
215-1595 Rev. E; ECN 17-00-014
9/28/2017
Installation
S93-572, S93-573, S93-574
Metering Air Valve Maintenance
Adjust Air Valve Meter Time
1 . Remove filter cap and use a screwdriver to tighten or
loosen the timer (see illustration at right) . Turning the
timer clockwise increases the time; turning the timer
counterclockwise decreases the time .
2 . Continue to adjust until the timer is set at desired length .
3 . Replace filter cap over the timer .
Tube Connection Leaks
1 . Push in the white manual release button while pulling the
tube out (see illustration at right) to disconnect the tube at
the connector . No tools are needed .
2 . To correct a leak, press tubing firmly into the connector
and make sure it is seated .
3 . If leak persists, remove tubing from the fitting, and trim
the tubing end square with a razor-sharp knife . If leak
continues, replace the fitting or contact your Bradley
representative for assistance .
Manual
Release
Button
Sealing
Ring
Air Valve
Tubing
Locking
Slope
Gripping
Ridge
Tube Stop
Water Tube Connector
Air Valve
Filter Cap
Air Tube Connector
Troubleshooting – Stop Valve
Problem
Cause
Solution
Water just dribbles
or does not flow from
sprayhead .
Water supply malfunctioning .
1 . Close the stops and check the valves that supply water to the
lavatory system .
2 . Inspect the stop valves for proper installation .
Water sprayhead
delivers all hot or cold
water .
Water supply or mixing valve
malfunctioning .
1 . Close the stops and check the valves that supply water to the
lavatory system .
2 . Inspect the stop valves for proper installation .
3 . Inspect mixing valve for proper hot and cold installation . A red
marking indicates the hot inlet .
The air valve timer is located next to the tube
connector on the air valve body. The timer is capped
with a filter to prevent dirt build-up on the timer. The
air valve timing can be adjusted from 5–60 seconds.