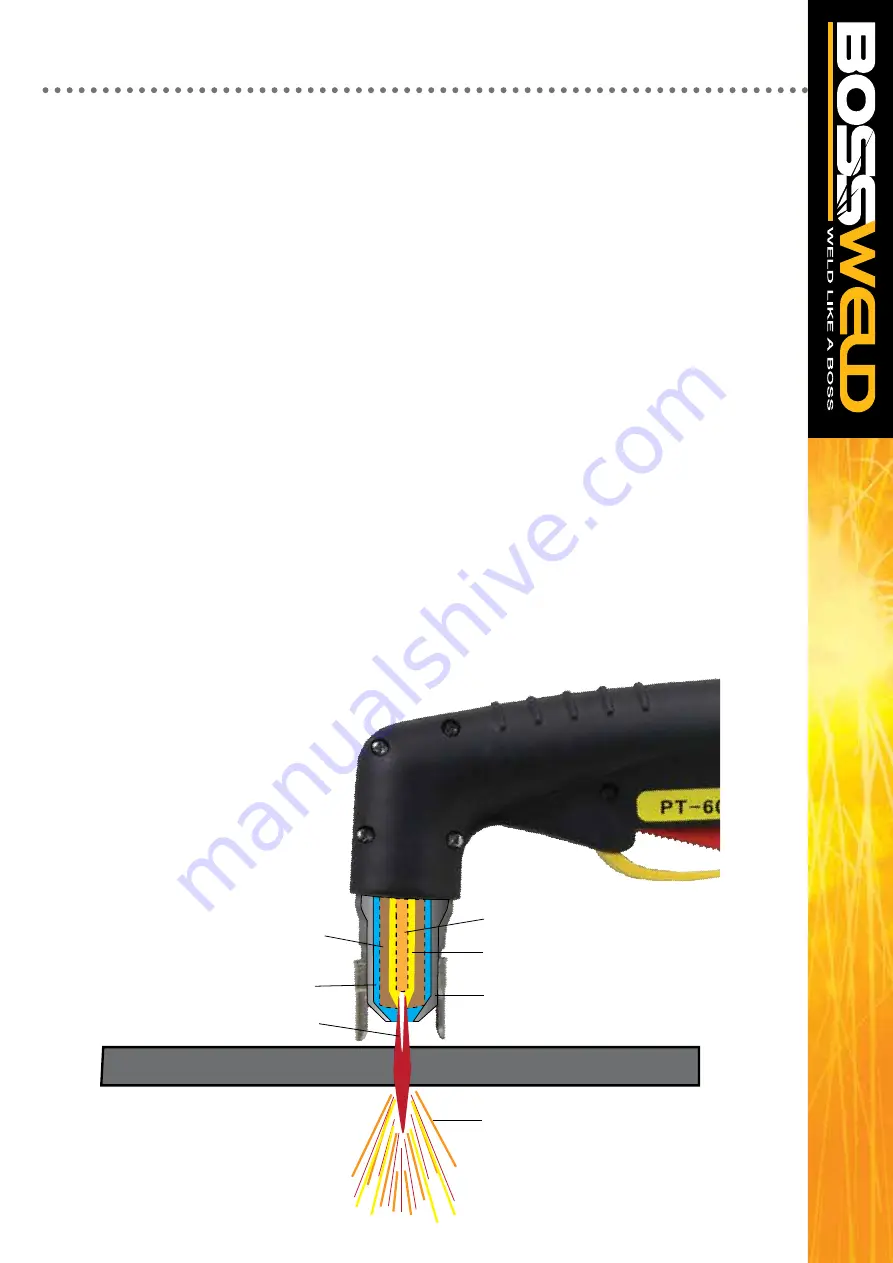
15
TIPS FOR PLASMA CUTTING
COMPRESSED AIR REQUIREMENTS
1. A reliable and consistent supply of clean dry compressed air is essential for proper operation.
2. The compressed air supply must have filtration in the line feeding the power source, both a standard
water trap (sintered bronze filter) and also a coalescing filter (for oil in air).
3. The unit requires a minimum (FAD) Free Air Delivery of 200LPM and 60 – 80 PSI pressure. This normally
means the compressor must be a belt drive model or if a direct drive it must have a motor power of 2.5HP
or greater.
4. The air must be dry and free of oil and moisture (normally a symptom of older, worn out compressors).
The air hose must also be of sufficient size (3/8”/10mm minimum) to supply the machine.
Note: Alloys generally take 50% more amperage for the thickness than steel
PIERCING THE WORK
Many inexperienced users try to pierce the metal by coming straight down perpendicular (90°) to the work.
This results in molten metal being blown back into the torch. A better method is to approach the metal at a
slight angle (60°) towards the direction of the cut. This way, the molten metal is blown away from the torch.
Handheld Operation – how it works
In a typical handheld plasma system, such as our Bossweld Plascut 40 Air Plasma, the electrode and nozzle
consumable parts are in contact with one another inside the torch when in the OFF state. When the trigger is
squeezed, the power supply produces a DC current that flows through this connection, and also initiates the
plasma gas flow. Once the plasma gas (compressed air) builds up enough pressure, the electrode and
nozzle are forced apart, which causes an electrical spark that converts the air into a plasma jet. The DC
current flow then switches from electrode to nozzle, to a path between the electrode and work piece. This
current and airflow continues until the trigger is released.
WORK PIECE
WORK PIECE
ELECTRODE
COOLING AIR
PILOT ARC
TIP
COMPRESSED AIR (PLASMA GAS)
NOZZLE
DROSS