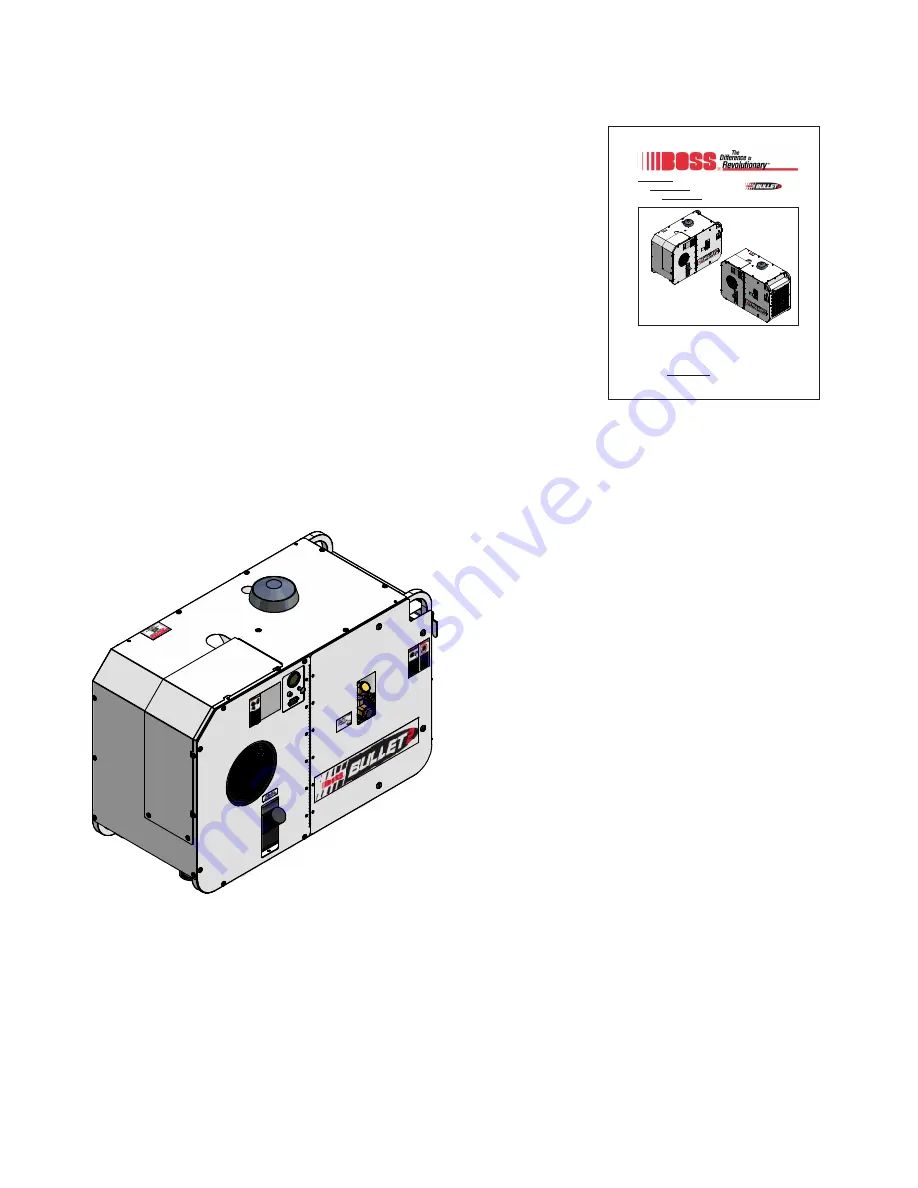
6
309003
Welcome
2.1 General Information
Thank you for choosing the Boss Industries Inc. Bullet 2 Air Compressor.
Before operating this compressor, read over this manual and become well
acquainted with your new machine. Doing this will increase your safety and
maximize the life of the machine.
While this manual is written to be as accurate as possible, Boss Industries
Inc. strives to continually improve the efficiency and performance of its
machines. As a result, sometimes there may be slight differences between a
given version of the manual and the machine.
2.2 Overview
The Boss Industries Inc. Bullet 2 is a compact, strategically designed system. It integrates all major
components on a single frame, which is enclosed in a tough, weather-resistant canopy.
The Bullet 2 design provides output of up to 70
CFM (cubic feet of air per minute) at up to a
maximum of 100 PSI (pounds per square inch).
Two maintenance doors make virtually all
components accessible for maintenance and
service. Instrumentation clearly displays pressure
and hours of operation. Other features, including a
spin-on compressor oil filter, and a spin-on
coalescer element, reduce the time and costs
associated with routine maintenance.
The Bullet 2 also has enhanced safety features to
protect your valuable resources: minimum pressure
orifice, high compressor oil temperature shutdown,
automatic blowdown device, pressure relief valve,
low engine oil pressure shutdown, and clearly
displayed warning/information decals.
This manual must be read carefully before using your Boss Industries Inc. Air Com-
pressor. Store in a safe and convenient location for future reference.
309003
04/7/2011 DCL
Service and
Maintenance
User Manual
Engine Driven
Air Compressor
For technical support:
Phone: (800) 635-6587 (USA)
Phone: (219) 324-7776 (Outside USA)
Fax: (877) 254-4249 (USA)
Email: [email protected]
Website: http://www.bossair.com
Summary of Contents for Bullet 2
Page 2: ...2 309003...
Page 26: ...26 309003...
Page 27: ...27 309003 WARRANTY SECTION...
Page 33: ...33 309003 PARTS AND ILLUSTRATION SECTION...
Page 37: ...37 309003 Engine System 5 5 6 4 1 2 10 9 8 7 3 10 2 Engine System continued...
Page 41: ...41 309003 Cooler System 6 3 10 2 7 5 9 1 8 4 10 4 Cooler System continued...
Page 48: ...48 309003 Wiring Diagram 10 8 Wiring Diagram...
Page 49: ...49 309003 System Schematic 10 9 System Schematic...