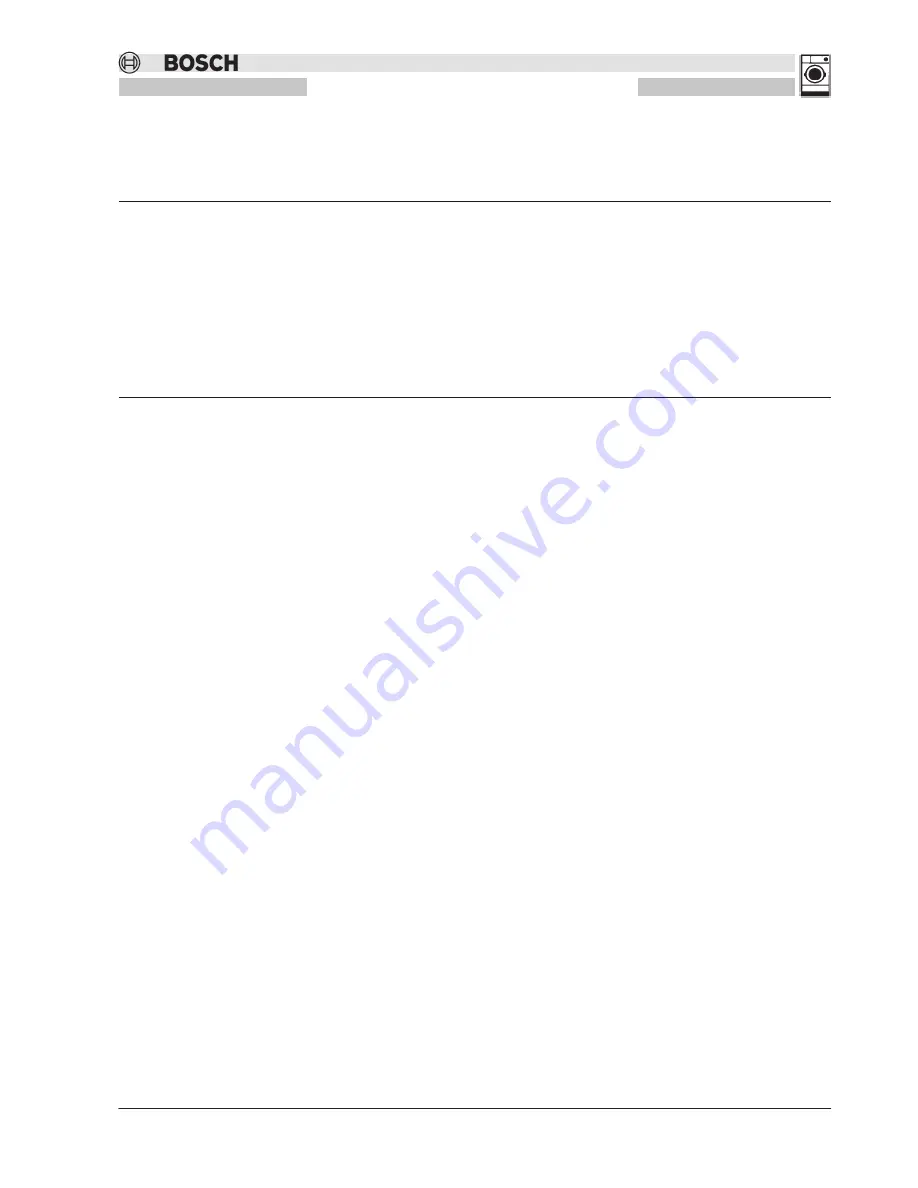
REPAIR INSTRUCTIONS
r120085e -15/1
04.99
TUMBLE DRYER
Vented WTA34.. / WTA35..
I.
SAFETY INFORMATION
Page
1
II.
OPERATION
Page
1
III.
DESCRIPTION OF FUNCTION / TECHNICAL INFORMATION
Page
2
IV.
CONSUMPTION RATES / ENERGY REQUIREMENT / OTHER DATA
Page
6
V.
REPAIRS
Page
7
VI.
SUPPLEMENTS
Page
13
I.
SAFETY INFORMATION
Before commencing repairs, ALWAYS disconnect the appliance from the power supply!
If tests have to be performed while the appliance is live, ALWAYS use a residual-
current-operated circuit-breaker! When repairs are complete, perform a function test, as
well as a safety test in accordance with VDE 0701.
1.
Safety test in accordance with VDE 0701
•
Plug in the tester mains plug.
In the case of switchover models connect L1 and L2 on the tester.
•
Switch on the appliance (door must be closed).
•
Perform the test.
II.
OPERATION
1.
Selecting the programme
•
“Cottons/coloureds”
Turn the programme selector in a clockwise direction to the
desired drying setting (6 automatic drying settings).
•
Easy-care
Turn the programme selector in an anti-clockwise direction to the
desired setting (5 automatic drying settings).
•
Timed programme
Turn programme selector / time switch to the desired time.
2.
Buttons
•
ON/OFF
Switches the appliance on / off.
•
“Low heat”
For delicate textiles. The temperature is reduced.