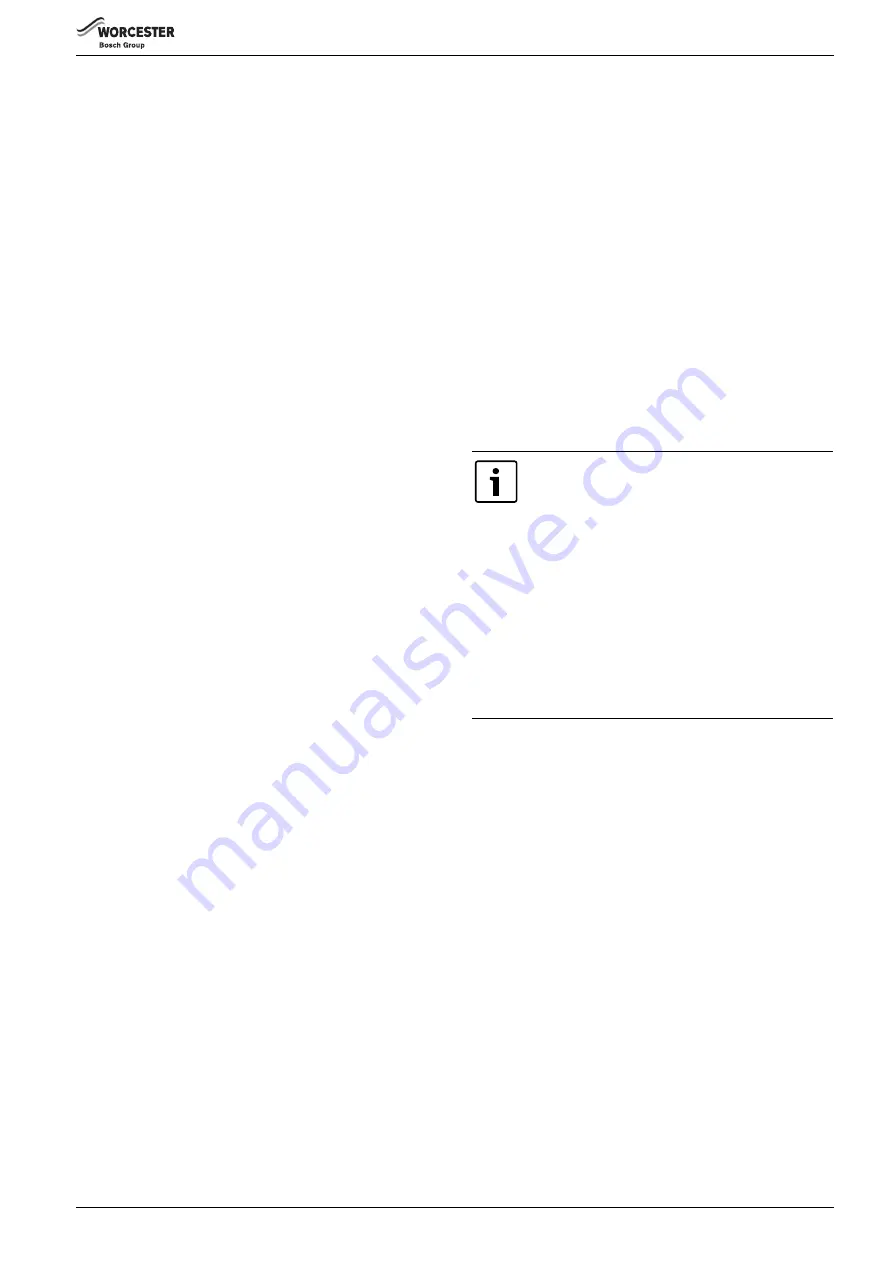
PRE-INSTALLATION
6 720 821 670 (2018/06)
29
Key to Figure 23 - Plume re-direct terminal positions:
[1]
This feature allows some basic plume re-direction options on a
standard telescopic horizontal flue terminal.
300mm minimum clearances to a opening e.g. window.
However the minimum clearances to an opening in the direction
that the plume management is facing, must be increased to
1,500mm.
Where the flue is less than 150mm to a drainpipe and plume
redirection is used the deflector should not be directed towards
the drainpipe.
[2]
300mm adjacent to a boundary line, unless it will cause a
nuisance. BS 5440: Part 1 recommends that care is taken when
siting terminal in relation to surfaces or boundary lines.
[3]
Where the flow of products of combustion is not at right angles to
the boundary, the 600mm dimension may be measured in the
direction of flow as long as the terminal is not less than 300mm
from the boundary.
[4]
When redirecting the flue discharge the terminal end must be at
least 1,500mm from any opening in the direction of the discharge
to prevent combustion products from entering the building.
Key to Figure 23 - Plume management terminal positions:
[5]
600mm distance to a surface or a boundary line, unless it will
cause a nuisance. BS 5440:Part 1 recommends that care is taken
when siting a terminal in relation to surfaces or boundary lines.
[6]
Proximity of flue duct outlet to boundaries, 2000mm distance to
an opening in adjacent building facing a terminal. BS 5440: Part
1 recommends that care is taken when siting terminal in relation
to boundary lines.
[7]
300mm adjacent to a boundary line, unless it will cause a
nuisance. BS 5440: Part 1 recommends that care is taken when
siting terminal in relation to surfaces or boundary lines.
[8]
300mm distance from a boundary line to the air intake as long as
the exhaust terminal faces away from the boundary line. The
exhaust terminal must have a minimum 300mm clearance to a
surface below and there must be at least 600mm clearance when
measured horizontally in a straight line from the exhaust terminal
to any other surface.
[9]
Plume Management kit air intake can be reduced to 150mm
providing the flue exhaust outlet is no less than 300mm adjacent
to a boundary line.
[10] Above, below and either side of an opening door, air vent or
opening window.
Using a Plume Management kit the air intake measurement can be
reduced to 150mm providing the flue exhaust outlet has a
300mm clearance.
[11] Below balcony or overhange. The air intake clearance can be
reduced to 150mm providing the flue exhaust outlet has a
200mm clearance.
[12] 1,200mm between terminals facing each other.
[13] Internal/external corners. The air intake clearance can be
reduced to 150mm providing the flue exhaust outlet has a
300mm clearance.
[14] Clearances no less than 200mm from the lowest point of the
balcony or overhang.
[15] If a plume management kit is installed within the confines of a
carport or other covered, partially enclosed extension, then the
exhaust terminal must be positioned at least 1200mm away from
any opening into the building which is sited within the footprint of
the carport.
If the exhaust terminal is extended at least 300mm beyond the
footprint of the carport then the distance from the terminal to an
opening within the carport can be reduced to 600mm.
The exhaust terminal can also be routed though the roof of the
carport providing 25mm clearance is provided around the flue
pipe to any flammable material and that it extends at least
300mm above the roof.
The air intake must have a minimum 150mm clearance to any
opening in the building in order to ensure the integrity of the
structure is maintained. If the exhaust terminates within the
footprint of the carport then the carport must have at least 2 sides
completely open. If the exhaust terminates at least 300mm
beyond the footprint of the carport then the carport must have at
least one completely open side. The exhaust terminal must be
positioned to ensure that plume will not cause nuisance or
damage to vehicles and that minimum clear distances in front of
the terminal will not be impeded by vehicles.
Note:
▶ Installations in car ports are not recommended.
▶ The flue cannot be lower than 1,000mm from the top
of a light well due to the build up of combustion
products.
▶ Dimensions from a flue terminal to a fanned air inlet
to be determined by the ventilation equipment
manufacturer.
▶ Plume kits running horizontally must have at least a
3° fall back to the appliance for proper disposal of
condensate, except or the initial horizontal run from
the terminal.
The initial plume kit horizontal run will have at least a
10° fall back to the appliance, due to the terminal
elbow design, for proper disposal of the condensate.
Summary of Contents for Worcester GREENSTAR 12Ri ErP +
Page 63: ...6 720 821 670 2018 06 63 Notes ...
Page 64: ...6 720 821 670 2018 06 64 Notes ...