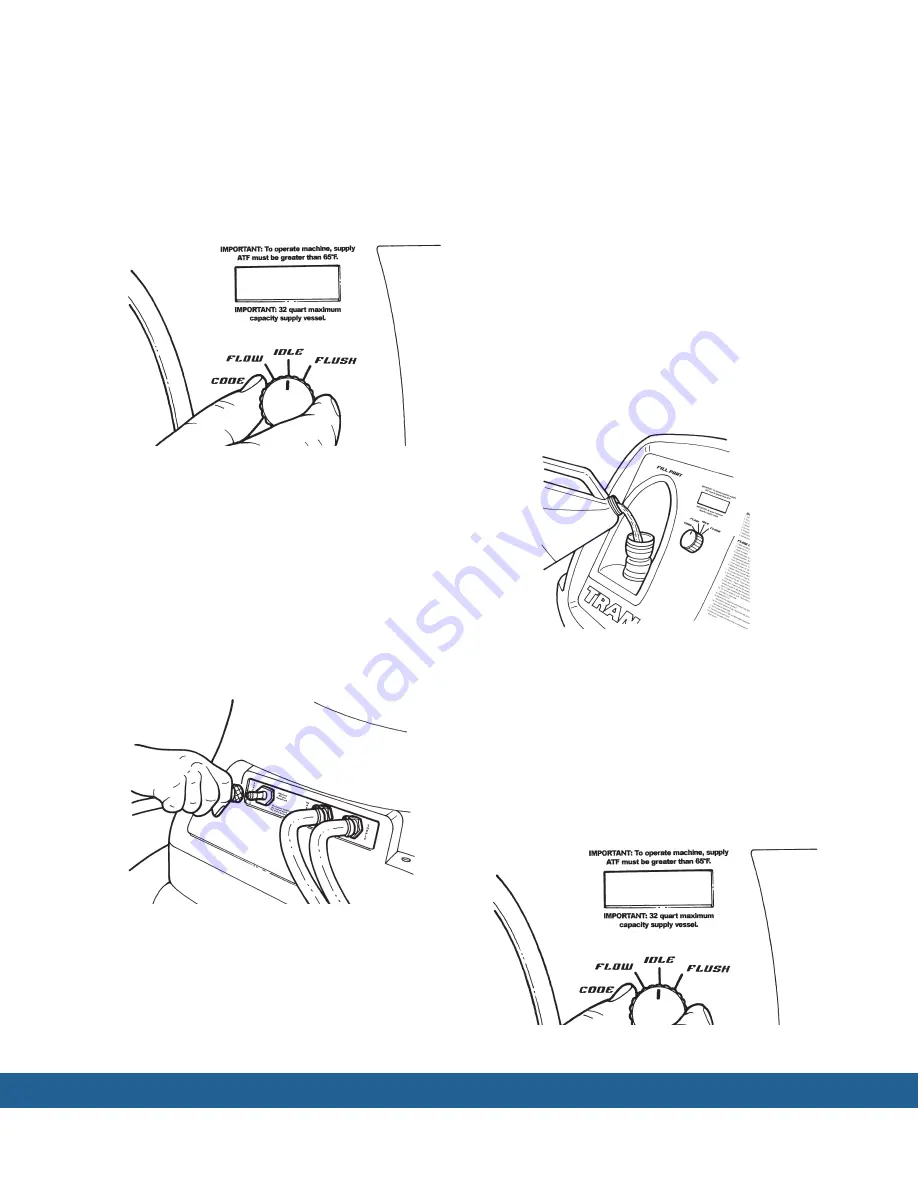
TRANSFLOW Transmission Cooling System Service Tool J-45096
9
TransFlow Self-Test
Important: Whenever a cooler fails the flow
test, disconnect from the cooler lines and run
the self-test procedure to verify flow is 2.0 gpm
or greater. If less than 2.0 gpm, ensure the shop
air supply maintains a minimum of 90 PSI when
connected to the tester. The entire self-test should
take no more than one to two minutes to com-
plete. For additional information, refer to "Use-
ful Information/Helpful Hints" in this manual.
1. Remove the fill port cap.
2. Add two gallons of Dexron VI
®
ATF,
or equivalent, to the supply vessel through
the fill port. See Figure 1.
Caution: Do not overfill the supply vessel.
Damage to the unit may result. To verify the fluid
level, view the LCD screen display while filling
the unit to ensure that the fluid level does not
exceed 32 US quarts.
Note: If the Self-Test has already been carried
out, verify the fluid level by viewing the LCD
screen display. See Figure 2.
Figure 1
3. Connect an air hose from your compressed
air supply to the quick-disconnect on the rear
panel marked SUPPLY AIR. See Figure 3.
Note: Using an accurate pressure gauge, ensure
there is a minimum 90 psi of Supply Air at the
quick-disconnect.
Figure 2
IDLE
FLUID 00 QTS @ 075F
Figure 3
2. Verify that the main function switch is in the
IDLE position. Place the main power switch
(see Control Panel graphic on page 4
for its
location) in the ON position, and wait for the
IDLE screen to initialize. See Figure 2.
Figure 2
IDLE
FLUID 20 QTS @ 075F