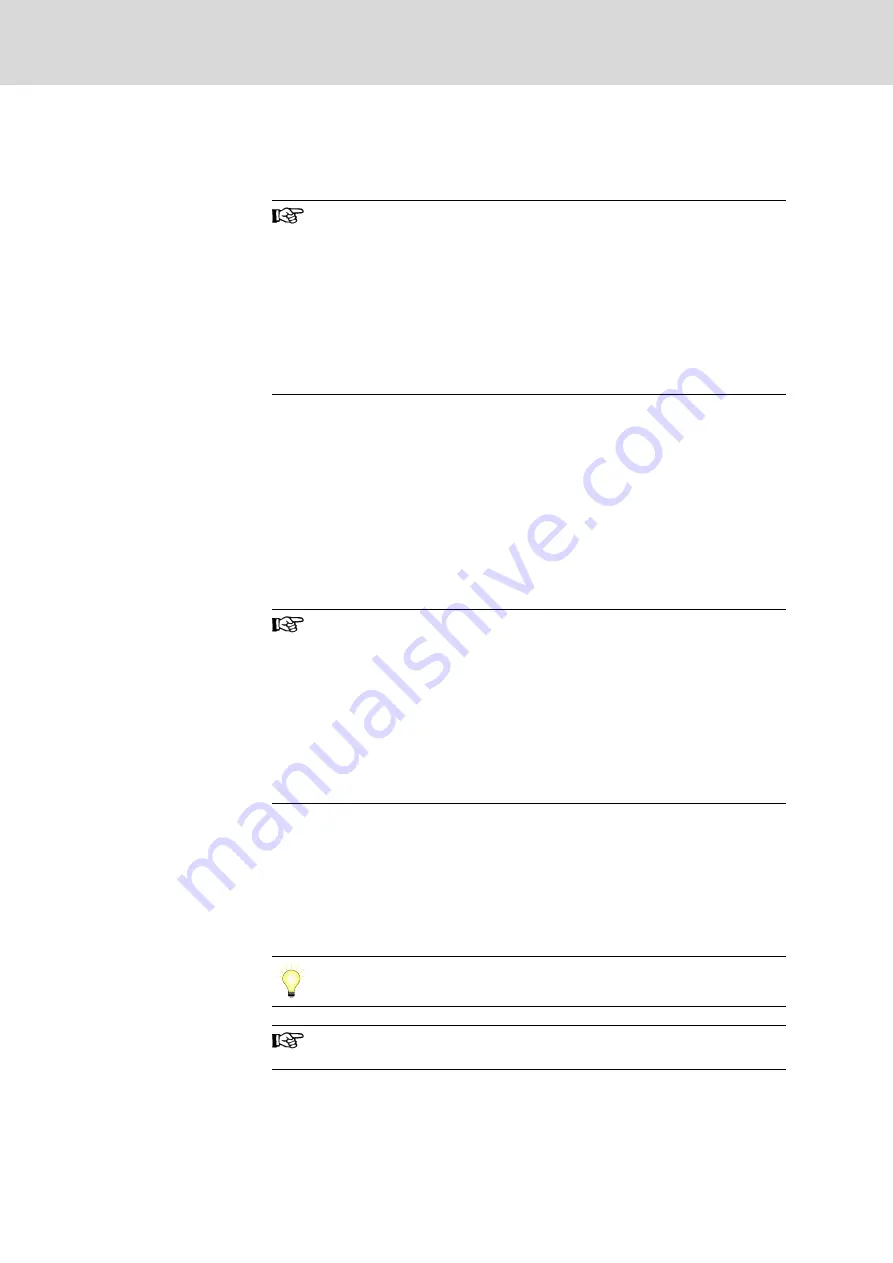
in connection cables with 3-pin valve connectors according to DIN and then
hooked up to the control section. The required connection cables are not in‐
cluded in the scope of delivery.
●
Suitable connection cables can be found in the Rexroth
document “Mating connectors and cable sets for valves and
sensors in hydraulics“, see also
supplementary documentation" on page 5
●
For a detailed description of the electrical interfaces and the
wiring diagrams, please refer to the related documentation
(electrical wiring diagram) from Bosch Rexroth.
●
Important information and safety instructions can be found in
the data sheets of the individual valves, see
"Required and supplementary documentation" on page 5
.
Connecting the valves –Y5, –Y6
as well as position monitors –SY5
and –SY6
The solenoids of valves –Y5 and –Y6 of the self-contained servo-hydraulic
linear axis have to be connected by means of plug-in connection cables with
2-pin + PE valve connectors, form A, according to EN 175301-803 and then
hooked up to the “control module for inductive loads - HAT02.1-002-NNN-
NN” (included in the scope of delivery). The required connection cables are
not included in the scope of delivery.
Position monitoring of the valves –Y5 and –Y6 at the self-contained servo-hy‐
draulic linear axis is realized by means of the two proximity switches –SY5
and –SY6. They have to be connected by means of plug-in connection cables
M12x1, 4-pin and then hooked up to the control section. The required con‐
nection cables are not included in the scope of delivery.
●
Suitable connection cables can be found in the Rexroth
document “Mating connectors and cable sets for valves and
sensors in hydraulics“, see also
supplementary documentation" on page 5
●
For a detailed description of the electrical interfaces and the
wiring diagrams, please refer to the related documentation
(electrical wiring diagram) from Bosch Rexroth.
●
Important information and safety instructions can be found in
the data sheets of the individual valves, see
"Required and supplementary documentation" on page 5
.
Connection of equipotential bond‐
ing at the drive unit
The drive unit is equipped with a connection point for establishing equipoten‐
tial bonding. It has to be connected before commissioning.
1.
Prior to the installation, ensure that the circumferential surface of the
thread is clean and fat-free.
2.
Connect the drive unit via a flexible equipotential bonding conductor with
a minimum cross-section of 6 mm
2
(16 mm
2
are recommended) to the
equipotential bonding system of your installation or machine.
Recommended raw cable:
●
ÖLFLEX HEAT 125 SC 1X 16 GNYE by Lapp Kabel
When selecting the equipotential bonding conductor, pay atten‐
tion to its oil resistance and temperature rating.
Bosch Rexroth AG
Operating Instructions
44/91
Self-contained servo-hydraulic linear axis Type SHA...
Installation