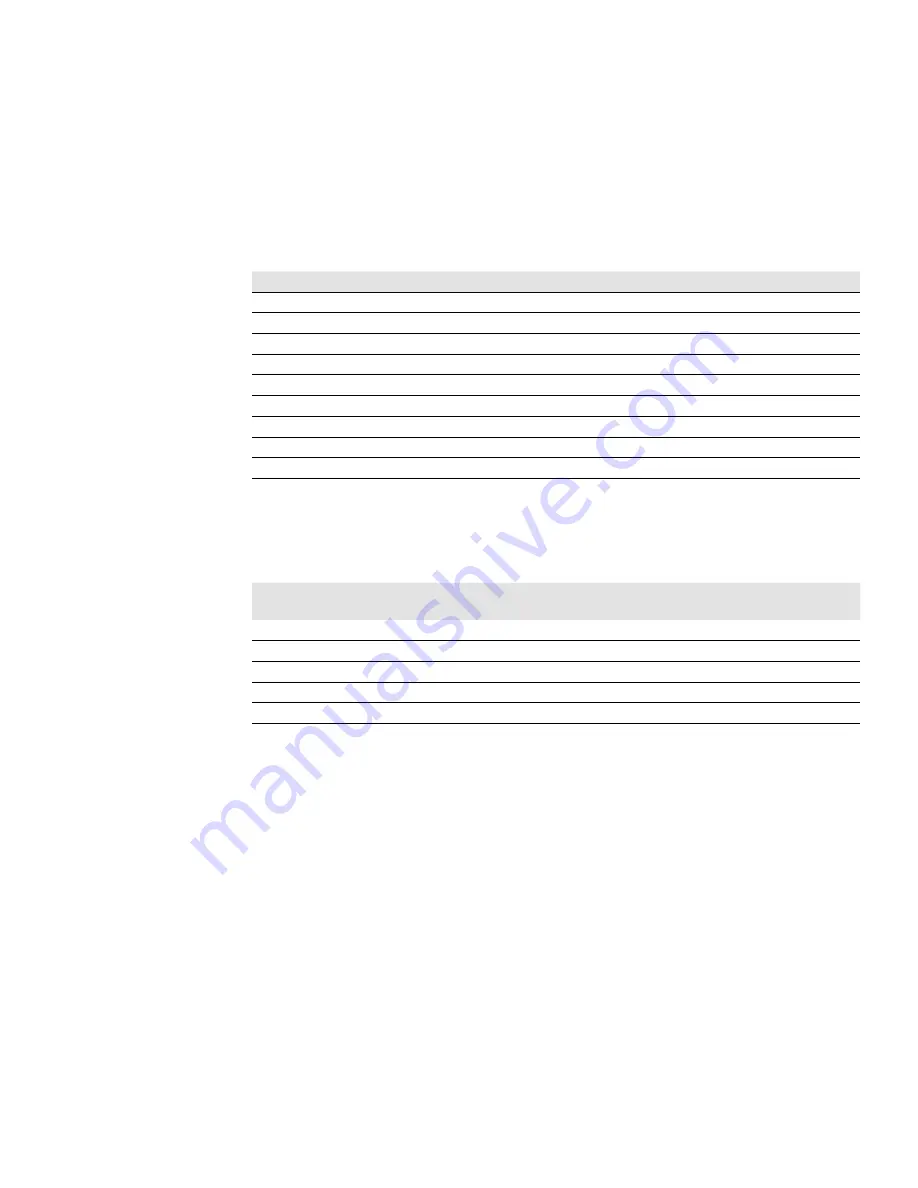
Bosch Rexroth Corp.
, USL00010, 01.2015
4 Preconditions
4.1 Commissioning the CKL drive controller
4.1.1 Hardware
Compact Module CKL
System size Carriage length
Primary part
Secondary part
CKL 110
180 mm
MCP030B-V180-NI-xxCN-NNNN
MCS030-3S-xxxx-NNNN
240 mm
MCP030C-V180-NI-xxCN-NNNN
MCS030-3S-xxxx-NNNN
300 mm
MCP030D-V180-NI-xxCN-NNNN
MCS030-3S-xxxx-NNNN
CKL 145
244 mm
MCP040C-V300-NI-xxCN-NNNN
MCS040-3S-xxxx-NNNN
364 mm
MCP040E-V300-NI-xxCN-NNNN
MCS040-3S-xxxx-NNNN
484 mm
MCP040G-V300-NI-xxCN-NNNN
MCS040-3S-xxxx-NNNN
CKL 200
237 mm
MCP070C-V300-NI-xxCN-NNNN
MCS070-3S-xxxx-NNNN
297 mm
MCP070D-V300-NI-xxCN-NNNN
MCS070-3S-xxxx-NNNN
417 mm
MCP070F-V300-NI-xxCN-NNNN
MCS070-3S-xxxx-NNNN
xx: L0 = digital Hall, L1 = analog Hall, N0 = without Hall
xxxx: 0120, 0180, 0300 = secondary part length mm, select any value
HCS01 IndraDrive Cs with Firmware MPx-17V08 or greater
Supported feedback combinations:
Firmware
Encoder
HCS01
connector
Hall unit HCS01
connector
Additional hardware requirement
MPE/B/C
analog
X4
without
without
none
MPE/B/C
digital
X4
without
without
none
MPE/B/C
analog
X4
digital
X4
with SHL03 Hall sensor box
MPB/C
digital
X4
analog
X8
with HCS01 dual encoder interface (EC-EC)
MPB/C
analog
X4
analog
X8
with HCS01 dual encoder interface (EC-EC)
Firmware: MPE=Economy, MPB=Basic, MPC=Advanced
Encoder: digital encoder is supported but analog encoder is recommended with IndraDrive!
For detailed descriptions of firmware and encoders, please see the IndraDrive MPx-17 (or later) Functions
Applications Manual.
4.1.2 Software
• IndraWorks Ds 13VRS (recommended)
• IndraWorks Ds 12VRS (possible with caution*)
4.1.3 Operating System
• Windows 7 (recommended)
• Windows XP (possible with caution*)
NOTE: Caution* = software bugs, unexpected behavior, limited tests
8
Preconditions