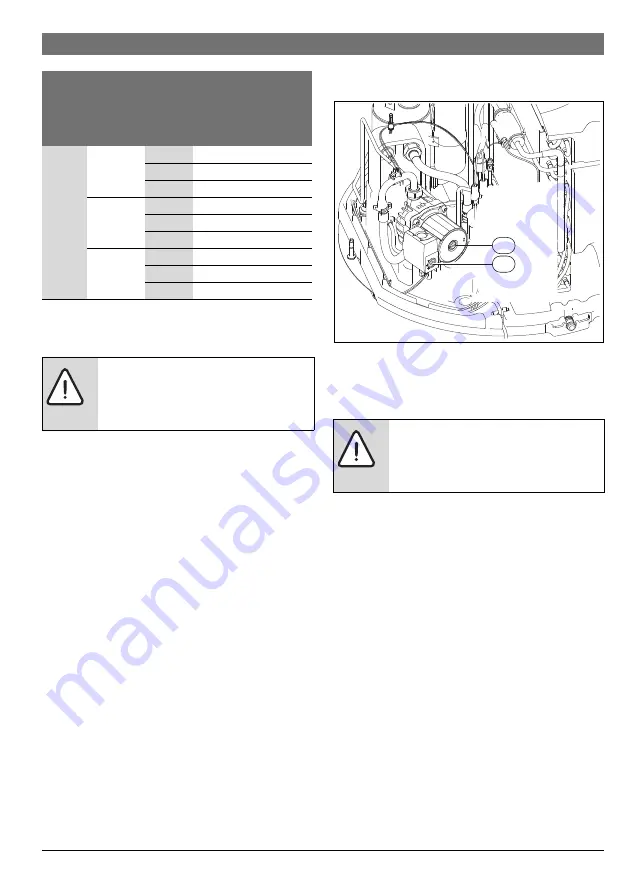
6 720 809 134 (2013/09)
Compress 3000 DW FII
Installation | 15
5.9 Filling the cylinder
Automatic filling - systems with water pressure above 3 bar
▶ Open the water outlet valve and at least one hot water tap.
▶ Open the water inlet valve on the cylinder (Fig. 5, [4]).
The cylinder is filled.
▶ Do not close the hot water taps until the water flows steadily
and is free from air bubbles.
The process of filling the cylinder is complete.
▶ Connect the appliance to the power supply via a separate
socket with an earth connection.
If the fault code "E09" appears on the display after a few
minutes, proceed as follows:
▶ Fill manually.
Manual filling - systems with water pressure below 3 bar
▶ Open the water outlet valve and at least one hot water tap.
▶ Open the water inlet valve on the cylinder (Fig. 5, [4]).
The cylinder is filled.
▶ Do not close the hot water taps until the water flows steadily
and is free from air bubbles.
▶ Connect the appliance to the power supply via a separate
socket with an earth connection.
▶ Set the selector switch on the heating pump (Fig. 11, [1]) to
"III"
.
Fig. 11
Heating pump
[1] Selector switch
[2] Air vent screw
▶ Select "Purg" operating mode (
▶ Open the drain screw on the heating pump (Fig. 11, [2])
until the water flows steadily and without air bubbles.
▶ Close the drain screw on the heating pump.
▶ Wait around 5 minutes until the "Purg" operating mode has
finished.
▶ Set the selector switch on the heating pump to
"I"
.
The process of draining and filling the cylinder is complete.
If the fault code "E09" appears on the display after a few
minutes, proceed as follows:
▶ Clear the fault (
page 25, section "Resetting the fault
display").
▶ Refill manually.
5.9.1 Water quality
Inadequate water quality or contaminated water can damage
the appliance.
Cylinder
type
Safety
valve
(maximum
pressure)
Water
pressure
in the
system
Capacity of the
expansion vessel
corresponding to the
switch-on pressure of
the safety valve
HP
270...
6 bar
2
12 l
3
18 l
4
25 l
8 bar
2
12 l
3
12 l
4
18 l
10 bar
2
12 l
3
12 l
4
18 l
Table 6
NOTICE:
Damage to the appliance!
▶ Prior to commissioning the appliance, fill
the cylinder with water and bleed the
system if necessary.
CAUTION:
Risk of scalding!
▶ Ensure that draining water from the air
vent screw presents no risk to people or
property.
6720804054-12.1V
2
1
Summary of Contents for Compress 3000 DW FI Series
Page 29: ...6 720 809 134 2013 09 Compress 3000 DW FII 29 Notes ...
Page 30: ...6 720 809 134 2013 09 Compress 3000 DW FII 30 Notes ...
Page 31: ...6 720 809 134 2013 09 Compress 3000 DW FII 31 Notes ...
Page 32: ...Bosch Thermotechnik GmbH Junkersstrasse 20 24 D 73249 Wernau www bosch thermotechnology com ...