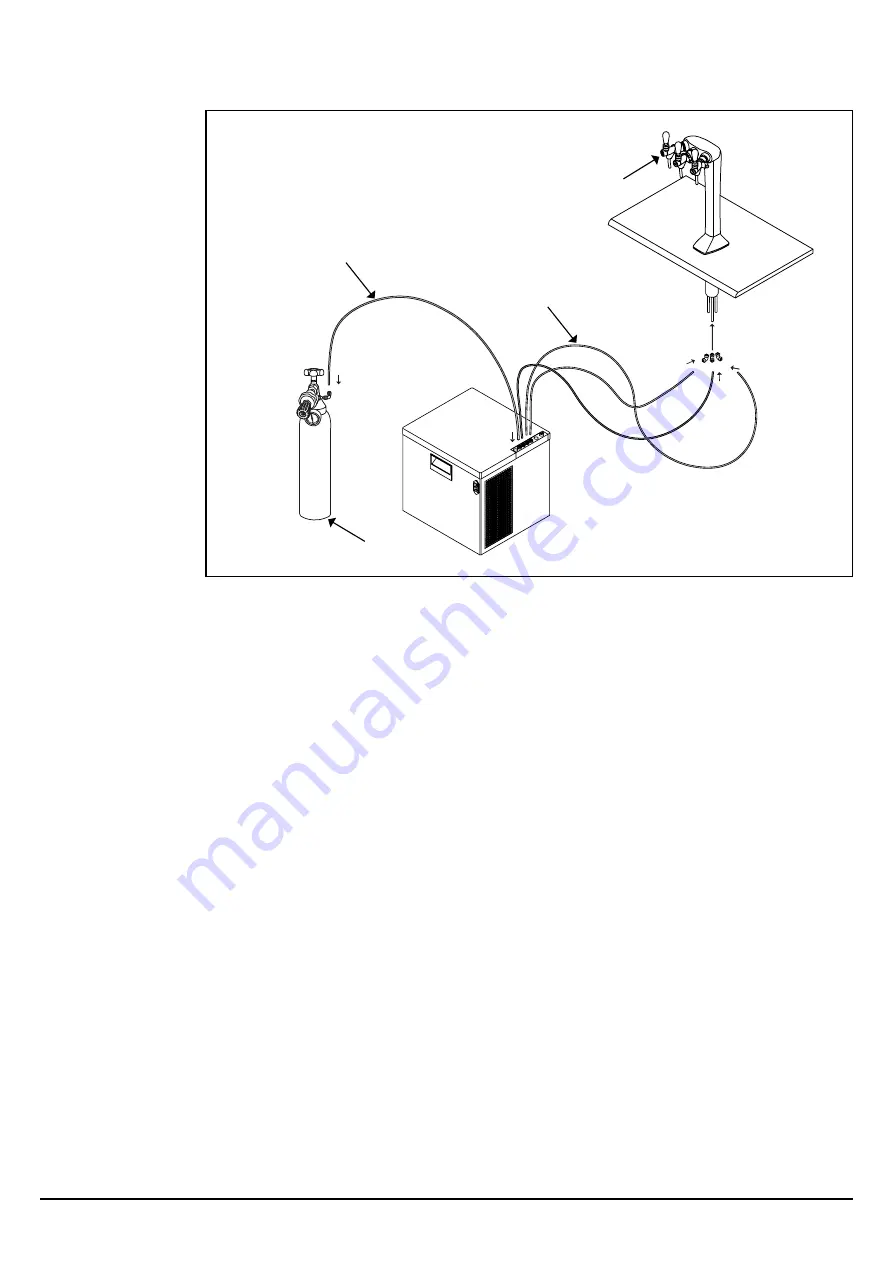
Borg & Overström
GB
12
Install & Operation Manual
The unit should be isolated from the electricity supply before removal of any covers.
Great care must be employed when working with high pressure carbon dioxide, and
in no cases should the maximum operating pressure of 58 PSI (4 bar) be exceeded.
Safety
Tap
Water Pipe
Co2 Bottle
Co2 Pipe