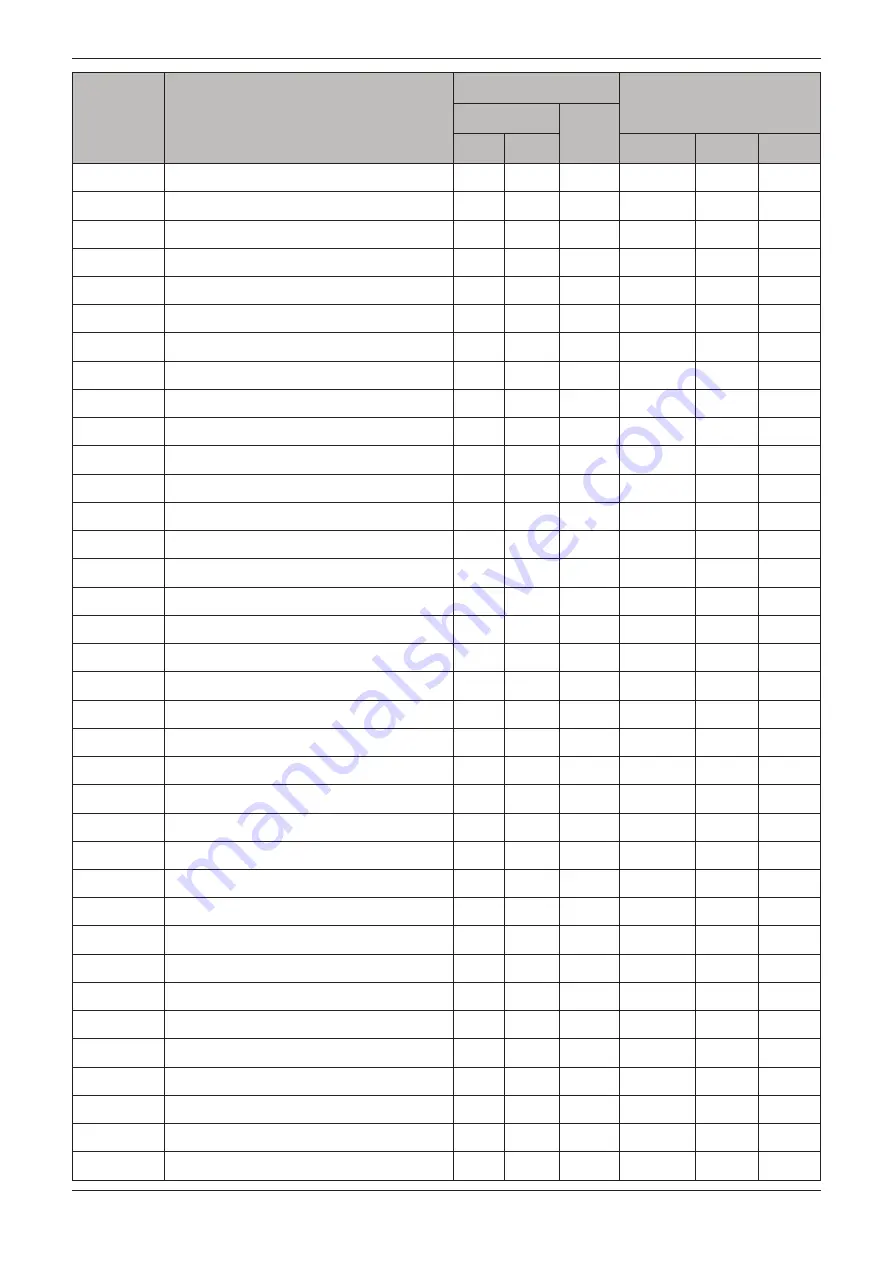
818 Sport Models
44
Azure Part
No
Azure Ref
Quantity
Exploded component
view reference
818
828
CW
CS
818CS
818CW
828
184422
Top Bracket-Front
1
C3
133424
Cold Tank Lid
1
C4
134564
Dispense Tube
1
C5
135732
Cold Tank Insulation -Top
1
C6
135731
Cold Tank Insulation
1
C7
133421
Cold Tank Coller
1
C8
183423
Large Back Nut
1
C9
174341
Thermostat Sleeve
1
C10
134605
Capillary Tube
1
C11
131581
Thermostat Sleeve Cap
1
C12
181125
4.0 x 16 S/S RHD S/T Screw
8
C13
131569
Cold Tank Outlet Seal
1
C14
131651
Cold Tank Outlet
1
C15
134592
1
/
4
" LLDPE Water Pipe
3
C16
131649
1
/
4
" Push Fit Tee
1
C17
134566
Vent Tube
1
C18
135722
Pipe Insulation
1
C19
135722
Pipe Insulation
1
C20
191161
PCB - Cold & Ambient
1
O1
135722
Pipe Insulation
1
O2
172148
Euro IEC Power Cord Set
1
1
E6
E6
User Manual
1
1
128981
B & O Carton
1
1
128904
Polybag
1
1
193221
CO
2
Regulator
0
1
120821
Front Infill Panel-Black
1
B3
184542
Spring Cap
1
B6
184543
Cup Retaining Ring
1
B5
184544
Spring Base Plate
1
B8
120932
Cup Dispenser Top Panel-Black
1
B4
184545
Spring
1
B3
120816
Door Panel-Silver
1
B2
184622
Door Magnetic Catch
2
B9
131341
3.0 x 10 BZP UK S/T Screw
2
B10
181341
3.0 x 8 YP PHD S/T Screw
6
B11
181134
4.0 X 12 BZP PHD S/T Screw
5
B12
Summary of Contents for 818
Page 1: ...INSTALLATION OPERATION GUIDE 818 SPORT MODELS ...
Page 3: ...Section1 Technical Manual 818 Sport ...
Page 9: ...Section2 Technical Manual 818 Sport ...
Page 21: ...Section3 Technical Manual 818 Sport ...
Page 24: ...Section4 Technical Manual 818 Sport ...
Page 31: ...Section5 Technical Manual 818 Sport ...
Page 39: ...Technical Manual 818 Sport Section6 ...
Page 46: ...Technical Manual 818 Sport Section7 ...
Page 49: ...818 Sport Models 49 ...
Page 50: ...818 Sport Models 50 ...
Page 51: ...Notes ...
Page 52: ...Notes ...
Page 53: ...Notes ...
Page 54: ...Notes ...