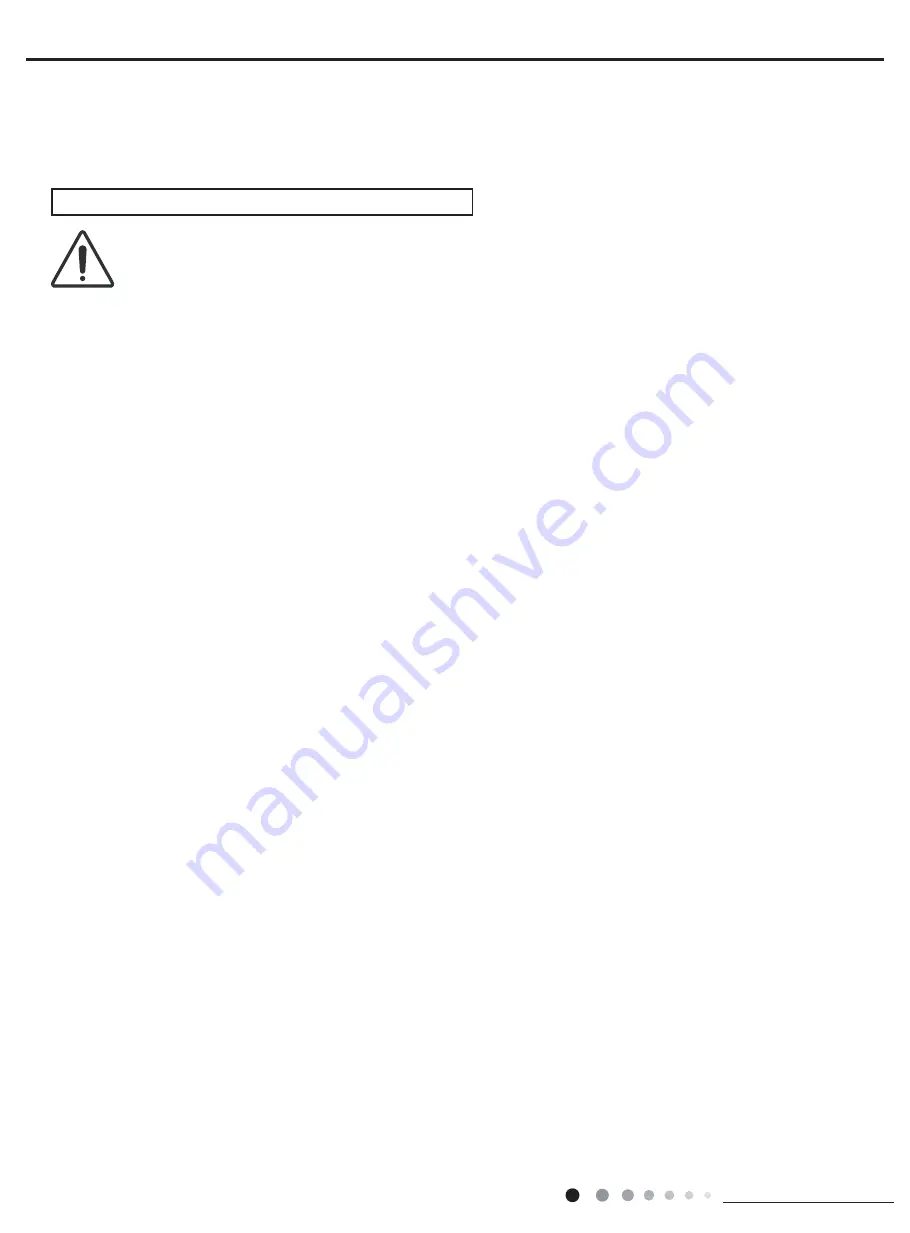
34
Installation and Maintenance
Service Manual
Safety Precautions for Installing
and Relocating the Unit:
Warnings
To ensure safety, please be mindful of the following precautions.
1. When installing or relocating the unit, be sure to keep the
refrigerant circuit free from air or substances other than the
�����������
Any presence of air or other foreign substance in the refrigerant
circuit will cause system pressure rise or compressor rupture,
resulting in injury.
2.When installing or moving this unit, do not charge the
refrigerant which is not comply with that on the nameplate or
������������
Otherwise, it may cause abnormal operation, wrong action,
mechanical malfunction or even series safety accident.
3.When refrigerant needs to be recovered during relocating
or repairing the unit, be sure that the unit is running in
cooling mode.Then, fully close the valve at high pressure
side (liquid valve).About 30-40 seconds later, fully close the
valve at low pressure side (gas valve), immediately stop
the unit and disconnect power. Please note that the time for
refrigerant recovery should not exceed 1 minute.
If refrigerant recovery takes too much time, air may be sucked in
and cause pressure rise or compressor rupture, resulting in injury.
4.During refrigerant recovery, make sure that liquid valve and
gas valve are fully closed and power is disconnected before
detaching the connection pipe.
If compressor starts running when stop valve is open and
connection pipe is not yet connected, air will be sucked in and
cause pressure rise or compressor rupture, resulting in injury.
5.When installing the unit, make sure that connection pipe is
securely connected before the compressor starts running.
If compressor starts running when stop valve is open and
connection pipe is not yet connected, air will be sucked in and
cause pressure rise or compressor rupture, resulting in injury.
6.Prohibit installing the unit at the place where there may be
�������������������
If there leaked gas around the unit, it may cause explosion and
other accidents.
7.Do not use extension cords for electrical connections. If
the electric wire is not long enough, please contact a local
service center authorized and ask for a proper electric wire.
��������������������������
������������������������������
between the indoor and outdoor units. Firmly clamp the
wires so that their terminals receive no external stresses.
��������������������
, wrong wire connections
������������������������������K
Summary of Contents for Brisa BRS09HPL1IA/OA
Page 20: ...17 Technical Information 6 Function and Control 6 1 Remote Controller Introduction...
Page 21: ...18 Service Manual...
Page 22: ...19 Technical Information...
Page 23: ...20 Service Manual...
Page 24: ...21 Technical Information...