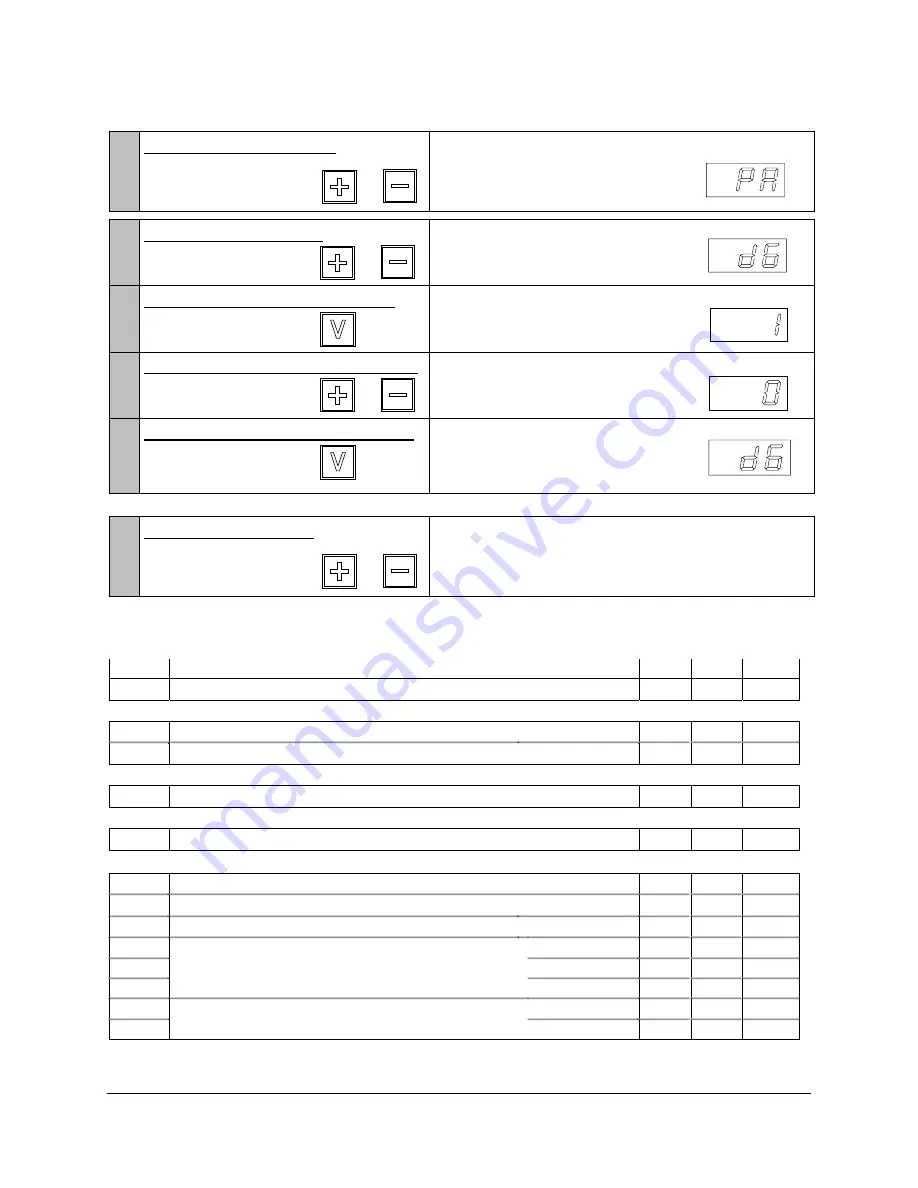
User Manual n°648261 –
Page 9
1.6 SPECIAL SETTINGS
1.6.1 PROGRAMMATION
(The regulation is ON)
1
Access to programmation :
Press simultaneously
and for a few seconds
)
and
Beginning of the programmation mode.
Display of the indication
2
Selection of parameters :
Press simultaneously
)
or
Display of the parameters one after another.
Display of the parameters’ codes
3
Access to the selected parameter :
Press
)
Presetting display of the parameter
4
Modification of the parameter setting
Press successively
)
or
Display of the parameter’s values one after another.
Display of the parameter’s values
5
Validation of the parameter’s setting :
Press
)
Display of the modified parameter’s
code
Start again stage 2 to 5 for the other parameters.
6
To exit programmation:
Press simultaneously
and for a few second
)
and
Restart of the system.
During or after programmation, the system
restarts automatically if no key is pressed in less
than 15 seconds.
The parameters’ modifications are definitively taken into account, even after the stop of the appliance
.
1.6.2 TABLE OF PARAMETERS
Code
Parameters
Min
Max
Fact.
PA
Password to access level 2
(reserved to installer)
-99
99
--
Temperature parameters
cA
Core probe temperature reading
(read only) °C
--
--
--
cc
Fragile products interior probe set-point
°C
-55
99
-15
Defrost parameters
d6
Defrost at the beginning of the prefunction cycle
0 = No, 1 = Yes
0
1
1
Ventilation parameters
F1
Ventilation with Fragile Products ON
(1)
0 = Weak,1 = Strong
0
1
1
Printing parameters (with optional printer
)
i1
Printing frequency in chilling cycle
mn
0
60
5
i2
Printing frequency in preservation cycle
mn
0
60
30
i3
Printing at the beginning of the cycle
0 = No, 1 = Yes
0
1
1
i4
Date setting
Day
1
31
(2)
i5
Month
1
12
(2)
i6
Year
990
050
(2)
i7
Time setting
Hour
0
23
(2)
i8
Minute
0
59
(2)
(1) Except for MI3
(2) The configuration must be set during installation