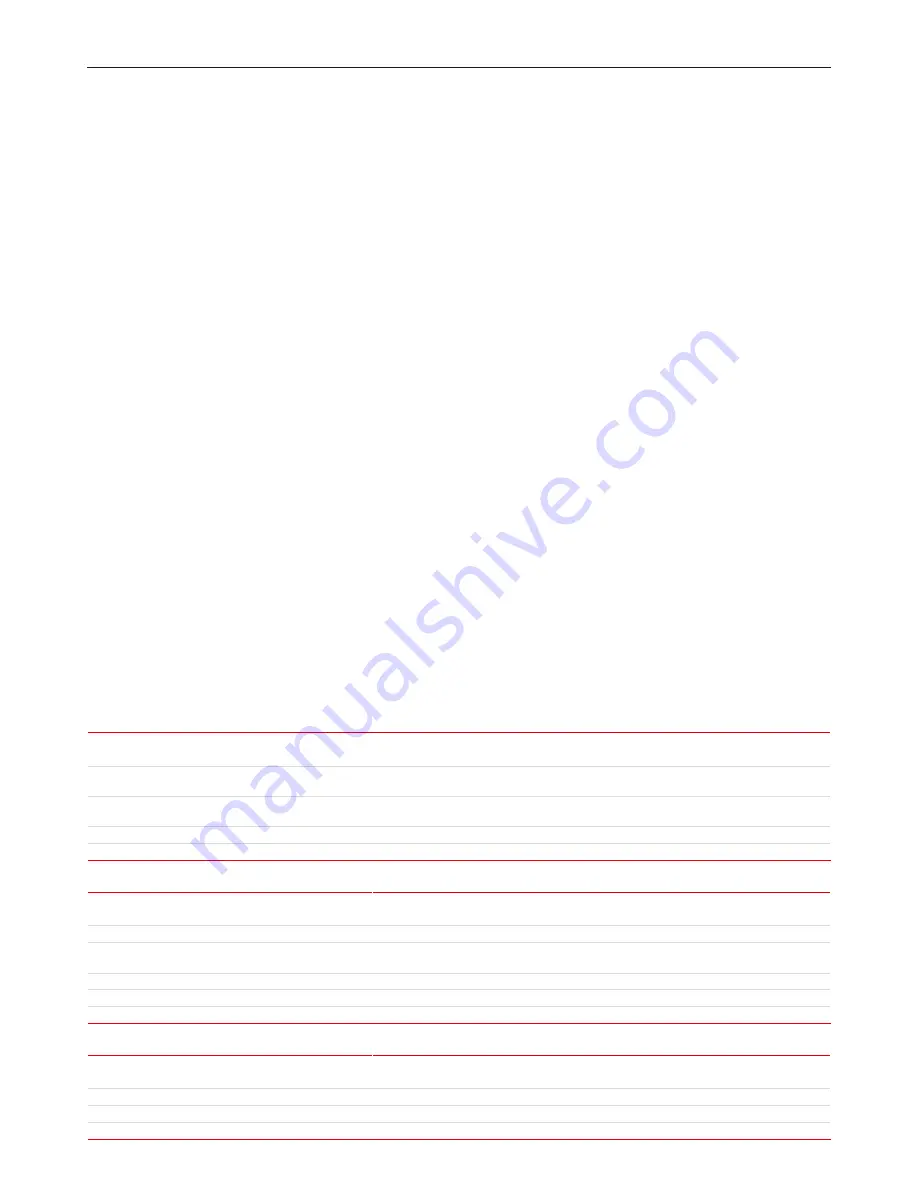
Cracking in Welds
Cause
Solution
Hot cracking in heavy sections or welding on metals prone
to hot cracking
Increase weld bead cross-section size. Change weld bead contour for e.g. concave to flat or
convex, check fit-up gap, reduce welding speed
Post weld cold cracking due to excessive joint restraint,
rapid cooling or hydrogen embrittlement
Preheat prior to welding. Use pure or non-contaminated gas. Increase the bead size. Prevent
craters or notches. Change the weld joint design
Centreline cracks in single pass weld
Increase bead size. Decrease root opening. Use preheat. Prevent craters
Underbead cracking from brittle microstructure
Eliminate sources of hydrogen, joint restraint, and use preheat
Inadequate shielding
Cause
Solution
Gas flow blockage or leak in hoses or torch
Locate and eliminate the blockage or leak
Excessive travel speed exposes molten weld to
atmospheric contamination
Use slower travel speed or carefully increase the flow rate to a safe level below creating
excessive turbulence. Use a trailing shield cup
Wind or drafts
Set up screens around the weld area
Excessive electrode stickout
Reduce electrode stickout. Use a larger size cup, or switch to gas saver or gas lens
Excessive turbulence in gas stream
Change to gas safer parts or gas lens parts
Short parts Life
Cause
Solution
Cup shattering or cracking in use
Change cup size or type. Change tungsten position
Short collet life
Ordinary style is split and twists or jams. Change to wedge style
Short torch head life
Do not operate beyond rated capacity. Do not bend torch heads
27
BOC Smootharc TIG 185 AC/DC Operating Manual
Summary of Contents for Smootharc TIG185 AC/DC
Page 1: ...Smootharc TIG185 AC DC Operating Manual...
Page 31: ......