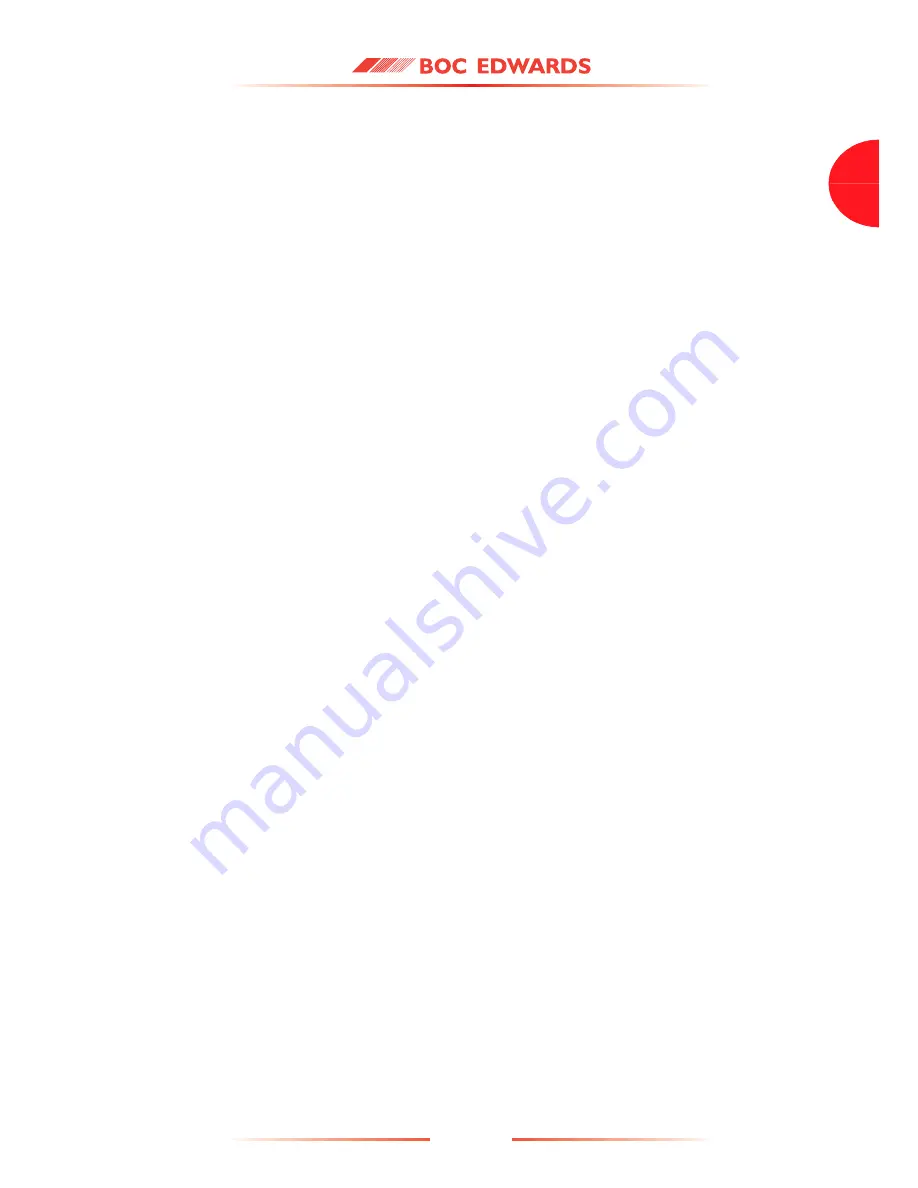
E2M28 and E2M30 Rotary Vacuum Pumps
IN
STALLATION
PAGE
15
Issue K
15
Jul 05
3.6.2
Standard single-phase motors
1.
Remove the cover from the motor terminal box (Figure 1, item 8).
2.
Remove the cable-gland from the inside of the terminal-box and fit the cable-gland to the cable
leadthrough hole in the side of the terminal-box.
3.
Pass the electrical supply cable through the gland.
4.
Remove the receptacle connectors from the fitting pack.
5.
Fit a ring connector to the earth (ground) wire.
6.
Select the correct size of receptacle connectors for your cable wires:
•
Use the red connectors for wire sizes 0.75 to 1.5 mm
2
.
•
Use the blue connectors for wire sizes 1. 5 to 2.5 mm
2
.
7.
Attach the appropriate connector to the live and neutral wires.
8.
Connect the electrical supply cable to the appropriate terminals as shown in Figures 3 to 5. You
must tighten the earth (ground) terminal connection to a torque of 2.13 to 2.87 Nm.
9.
Tighten the dome shaped nut on the cable-gland until the outer sheath of the cable is firmly gripped.
Do not overtighten.
10.
Check that the cable connections are correct, then refit the cover on the motor terminal-box.
3.6.3
Amphenol version single-phase motors
When you select the mating half of the amphenol connector, please ensure that it is compatible.
For conformance with CSA standards, only CSA certified connectors are to be used; the protective earth
(ground) connection is required to make first and break last with respect to the other connections.
Connect the electrical supply cable to the appropriate pins as shown in Figure 6.
3.6.4
110/200-240 V 50 Hz or 115-120/200-230 V 60 Hz single-phase motors
The motor is designed for a single-phase electrical supply and is suitable for 50 Hz and 60 Hz operation.
The motor can be manually switched between nominal supply voltages of 110-120 V and 200-240 V.
Use the following procedure to check that the voltage selector switch is correctly positioned for your
electrical supply voltage:
1.
Refer to Figure 7. Undo the three screws securing the terminal box cover (1) and remove the
cover.
2.
Check the position of the voltage selector switch (6). If the switch is in the correct position,
continue at Step 3. If the voltage selector switch (6) is in the wrong position, press the switch to
select the alternative position.
3.
Refit the terminal box cover and secure with the three screws.
When you select the mating half of the connector, please ensure that it is compatible (IEC60320 C19
female). For compliance with CSA standards, only CSA certified connectors are to be used.
Summary of Contents for E2M28
Page 6: ...E2M28 and E2M30 Rotary Vacuum Pumps PAGE iv Issue K iv Jul 05 This page intentionally blank...
Page 16: ...E2M28 and E2M30 Rotary Vacuum Pumps PAGE 10 Issue K 10 Jul 05 This page intentionally blank...
Page 34: ...E2M28 and E2M30 Rotary Vacuum Pumps PAGE 28 Issue K 28 Jul 05 This page intentionally blank...
Page 42: ...E2M28 and E2M30 Rotary Vacuum Pumps PAGE 36 Issue K 36 Jul 05 This page intentionally blank...
Page 44: ...E2M28 and E2M30 Rotary Vacuum Pumps PAGE 38 Issue K 38 Jul 05 This page intentionally blank...
Page 51: ...This page intentionally blank...