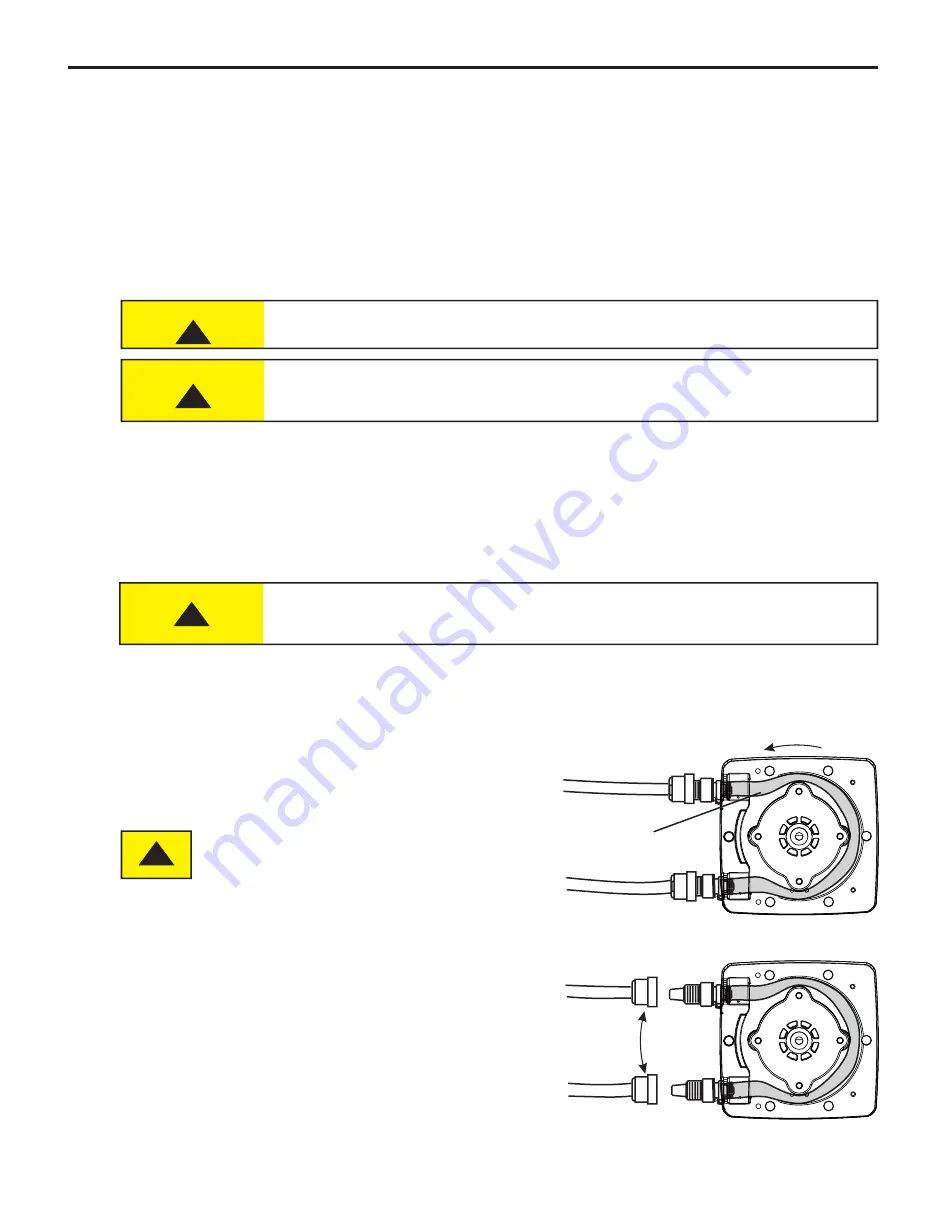
13.0 TFD (Tube Failure Detection)
Flex-Pro is equipped with a
Tube Failure Detection
System which is designed to
stop pump and provide an output alarm in event pump tube should rupture and
chemical enters pump head. Pump will detect a chemical with a conductivity
reading greater than 500 microsiemens. Chemicals with a conductivity of less
than 500 microsiemens will not be detected.
This patented system is capable of detecting presence of a large number of
chemicals including Sodium Hypochlorite (Chlorine), Hydrochloric (muriatic)
Acid, Sodium Hydroxide, and many others. System will not be triggered by water
(rain, condensation, etc.) or silicone oil (roller and tubing lubricant).
Chemical from tube failure
Flex-Pro has a built in Pump Tube Timer. Timer starts when rotor is rotating and stops when rotor is idle.
To view current Pump Tube Timer value, press and hold START button, then press and release DOWN arrow.
Tube Timer screen will appear. Screen will display current Pump Tube Time in run-time hours. Tube Timer screen
will display for 4 seconds and then switch back to previous operating display screen.
While displayed, press START button twice to reset Pump Tube Timer to zero.
When replacing pump tube, pump will ask you if you’d like to reset Pump Tube Timer. If you choose YES, screen
will display current Pump Tube Time for 5 seconds before timer is reset to zero.
If system has detected chemical, pump tube must be replaced and pump head and roller assembly must be
thoroughly cleaned. Failure to clean roller assembly will void warranty.
If TFD alarm occurs, pump will stop, close an alarm output, and screen will flash TFD with an alarm icon.
Confirm Chemical Detection
To determine if your chemical will be detected by system, remove pump head cover and pump tube and roller
assembly.
Place a small amount of chemical in bottom of pump head - just enough to cover sensors. Replace pump head
cover only.
Turn on pump (press START). If TFD system detects chemical, pump will stop after a two second confirmation
period and TFD Alarm screen will display. If TFD system does not detect chemical, pump will continue to run after
confirmation period.
Carefully clean chemical out of pump head being sure to remove all traces of chemical from sensor probes.
Replace roller assembly and tubing. Replace pump head cover. Press START button to clear alarm condition and
restart pump.
12.0 Pump Tube Timer
Tube Life Timer
Display tube life timer.
Press and hold START button.
Press and release DOWN arrow.
Displays amount of total runtime hours on currently installed tube.
Time will be displayed in hours.
Timer will be display for approximately 4 seconds before returning to
previous runtime screen.
236
1
SPEED
Hours
Page 31
Page 30
®
FLEXFLO A2
®
FLEXFLO A2
Pump has a built in 3 amp alarm output relay. Relay is pre-configured to energize on tube failure detection (TFD)
and on Flow Verification Sensor (FVS).
A Flow Verification Sensor must be installed and configured for relay to trigger on no-flow conditions.
Prior to service, pump clean water through pump and suction / discharge line to remove
chemical.
Always wear protective clothing, face shield, safety glasses and gloves when working on or
near your metering pump. Additional precautions should be taken depending on solution
being pumped. Refer to MSDS precautions from your solution supplier.
Reverse rotation of pump; press and hold REVERSE ROTATION button until rotor begins rotating in opposite
direction. This process can be used for many reasons throughout various industries.
Two reasons for reversing current rotor rotation; to purge chemical from tubing and to extend tube life.
Plan ahead before reversing rotor rotation. If check valves are installed, make necessary arrangements to allow
back flow.
If your desire is to simply extend tube life:
Typically tubing fails on outlet side (pressure side) of tube assembly in pump head.
Failure to install check valves in their proper flow direction can cause excess pressure
(PSIg) build up in system and can result in tube rupture.
Always use extreme caution and ensure proper connections when using this feature.
Swap Inlet
and Outlet
ON
R
T
F
Reversing rotation, moves outlet side (pressure side) to
opposite side of tube assembly, greatly increasing tube life.
Stop pump before tube failure occurs.
Disconnect power from pump. Carefully purge any pressure
in discharge line of pump. Disconnect suction end tubing and
discharge end tubing from pump head tubing.
IMPORTANT! Swap sides of suction (inlet) and discharge
(outlet) tubing. No need to remove Pump Head Cover.
Double check all connections before starting pump.
ON
R
T
F
Outlet
Inlet
D
ir
n
e
o
i
c
t
t
a
i
t
o
o
n
R
Typical Failure Point
(pressure side)
!
CAUTION
!
CAUTION
!
CAUTION
!
15.0 Reverse Rotor Rotation
14.0 Alarm Relay