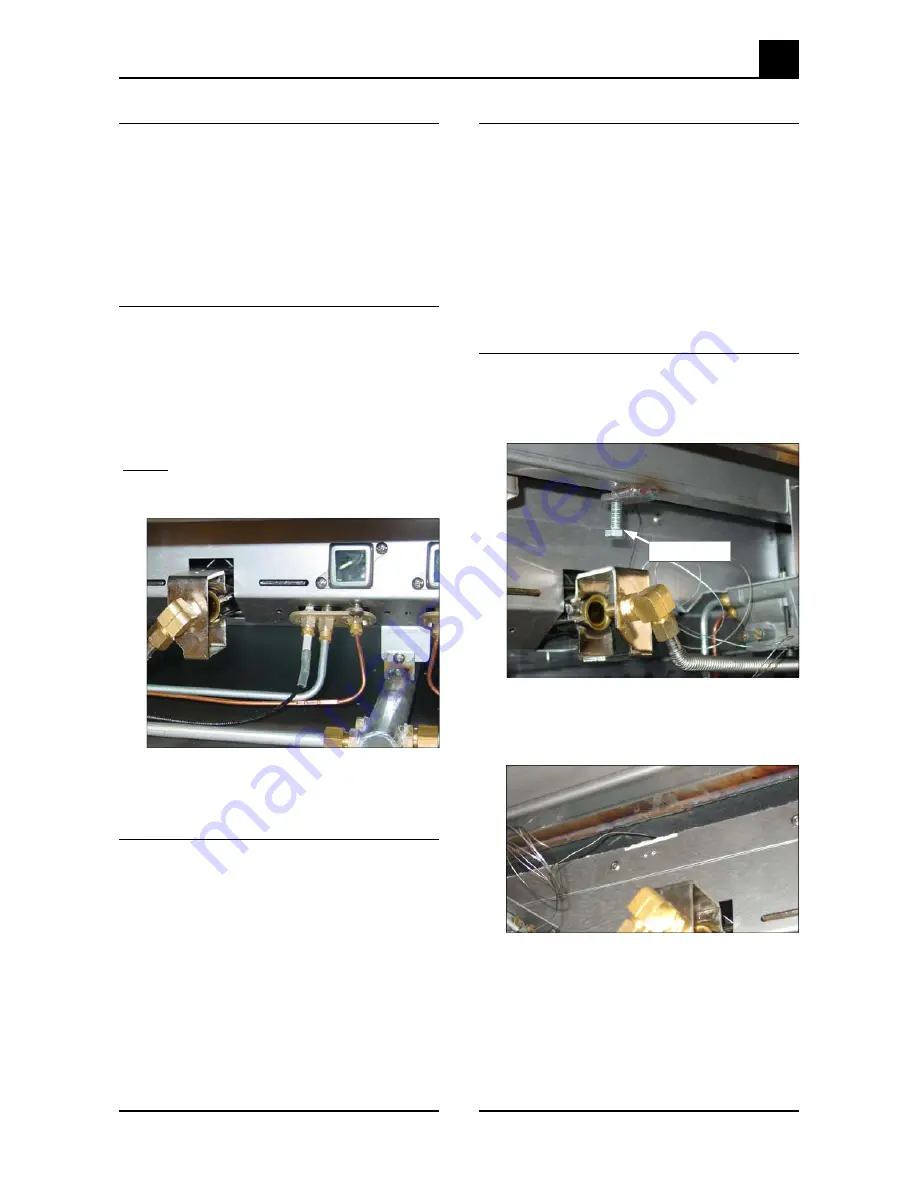
6
Service Procedures
21
© Moffat Ltd, January 2007
Revision 1/
Blue Seal Evolution Series Gas Griddles
6.2.4 Pilot Burner Injector
1) Remove the pilot burner (refer 6.2.3).
2) Withdraw the pilot burner injector from the
pilot burner.
3) Clean or replace as necessary.
4) Reassemble in reverse order.
6.2.5 Thermocouple
1) Remove the griddle plate control panel (refer
section 6.1.1).
2) Disconnect the thermocouple from the pilot
burner assembly.
3) Undo the thermocouple from the rear of the
gas control valve.
4) Replace thermocouple and reassemble.
NOTE: When screwing thermocouple back into
gas control, once threaded up tighten up
another ¼ turn only. Do not over-tighten.
6.2.6 Spark Electrode
1) Remove the griddle plate control panel (refer
section 6.1.1).
2) Undo the spark electrode from the pilot
burner assembly.
3) Replace electrode and reassemble.
6.2.7 Piezo Ignitor
1) Remove the griddle plate control panel (refer
section 6.1.1).
2) Remove the HT lead form the rear of the
piezo ignitor by pulling firmly away.
3) Unscrew the nut securing the piezo ignitor to
the control panel.
4) Replace ignitor and reassemble.
6.2.8 Gas Control
1) Remove the griddle plate control panel (refer
section 6.1.1).
2) Using the jacking screw provided, lift the
griddle plate as high as possible.
Figure 6.2.8a
Figure 6.2.8b
3) Withdraw the thermostat capillary and phial
from it’s pocket underneath the plate.
Figure 6.2.5
Jacking screw