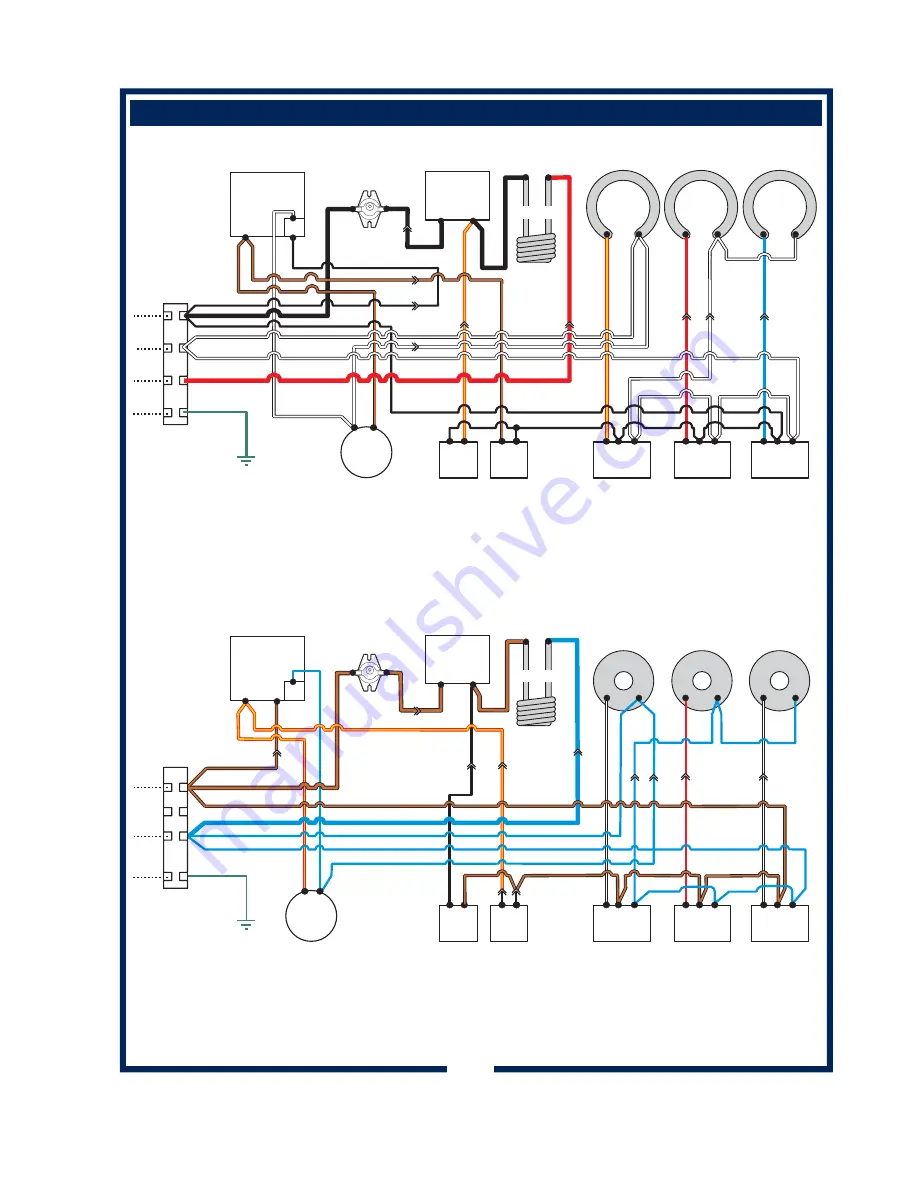
WIRING DIAGRAMS (continued)
23
601
75815
Owner
s
M
anual In
tegri
ty Decante
r
B
rewers
TIMER
GREEN
LINE
LINE
NEUT
GND
1
2
3
1
2
3
1
2
3
READY
LIGHT
BREW
SWITCH
WARMER
SWITCH
WARMER
SWITCH
WARMER
SWITCH
SOLENOID
BLACK
BLACK
BLACK
BLACK
RED
BROWN
BROWN
WHITE
WHITE
WHITE
WHITE
WHITE
WHITE
WHITE
WHITE
WHITE
WHITE
BLUE
BROWN
MODEL 9016
RED 12 ga
ORANGE
ORANGE
MAIN
WARMER
TOP
REAR
WARMER
TOP
FRONT
WARMER
C1
A1
A2
C2
C3
B1
B2
B3
A4
HI-LIMIT
BLACK
BLACK
BLACK
12 ga
12
ga
12
ga
THERMOSTAT
ELEMENT
p/n 72356
TIMER
GREEN
1
2
3
1
2
3
1
2
3
READY
LIGHT
BREW
SWITCH
WARMER
SWITCH
WARMER
SWITCH
WARMER
SWITCH
SOLENOID
BROWN
12
ga.
BROWN
12
ga.
BROWN
BROWN
MODEL 9016EX
MAIN
WARMER
TOP
REAR
WARMER
TOP
FRONT
WARMER
B2
THERMOSTAT
ELEMENT
p/n 73652
A4
B1
B3
C3
C2
C1
A1
A3
HI-LIMIT
BROWN
BLUE
BLUE
BLUE
BLUE
BLUE
BLUE
12
ga
BLUE 12 ga
BLACK
WHITE
WHITE
ORANGE
ORANGE
RED
BLUE
LINE
LINE
GND