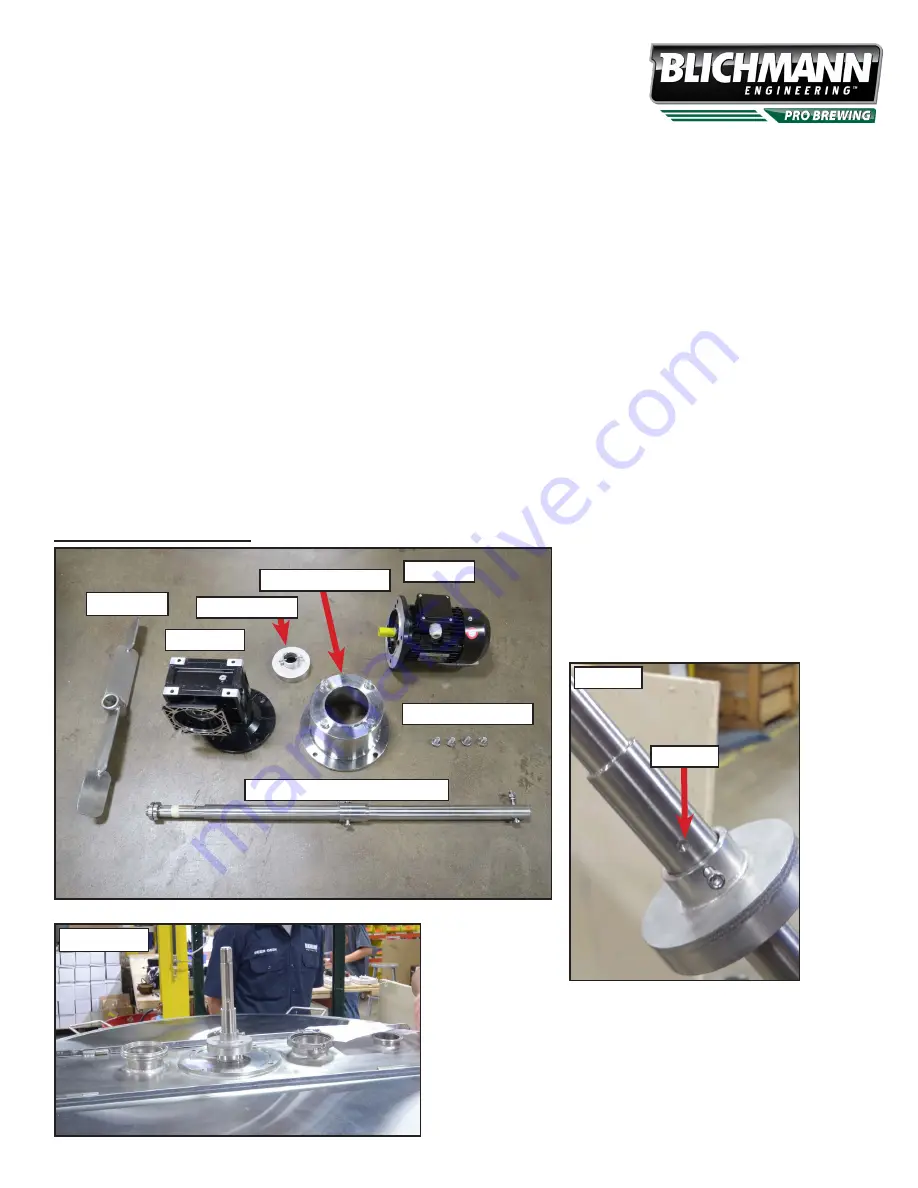
7 BBL Insulated Hybrid Brewhouse V1
© Blichmann Engineering, LLC 2018
For replacement parts, visit: blichmannengineering.com/genuine-replacement-parts
7
Chillers:
Sanitize the chiller by either pumping StarSan or similar copper friendly sanitizer through the chiller. Alternately the chiller may be submerged
(fittings up) into a pail of sanitizer. Drain the chiller after the recommended time with the fittings facing down. Connect the chiller per the instructions
on the nameplate.
Drain off the first gallon or so of wort from the boil kettle to a waste drain to eject any solids in the piping and to ensure only clear wort flows through the
chiller, use the higher drain point to prevent plugging. Then divert the flow to the chiller. Adjust the wort flow and/or the cooling water flow to achieve
the desired wort temperature to your fermentor.
IMMEDIATELY
after use back-flush the chiller with hot water to eject any solids and wort. IMMEDIATELY soak the chiller, with fittings up, in PBW or
other copper friendly cleaning agents for 30 min or pump through the chiller. Rinse with hot water and then soak in sanitizer. Allow to drain, with fittings
down, then store with the chiller horizontal. Following this procedure consistently will give you a very long service life for your chiller.
Pumps:
The pumps included with the system
MUST NOT
run dry or the impeller bearing surface will be damaged! This is NOT covered under warran
-
ty. Ensure the hoses and pump head are filled with liquid before turning on the pump. If you hear a loud squeal stop the pump immediately!
Caution:
NEVER restrict the inlet to the pump. Always place flow throttling valves on the OUTLET of the pump ONLY. Failure to do this will cause
cavitation in the pump possibly leading to failure of the impeller. If you hear any grumbling or grinding in the pump STOP IMMEDIATELY as this is
cavitation. Cavitation failures are NOT covered under warranty.
Installing the Mash Rake
Motor
Gear Box
Gear Box Mount
Impeller
Two Piece Impeller Shaft
Shaft Collar
Step 1:
Dissasemble the two piece impeller shaft by
removing the cotter pin. Remove the threaded nuts
from the top of the impeller shaft.
Slide the shaft collar over the impeller shaft as shown
in
Figure 1
. Screw the mounting bolts into the divots
on the impeller shaft.
Nuts and Bolts
Divot
Figure 1
Step 2:
Place the shaft into the kettle as shown in Figure 2.
Figure 2