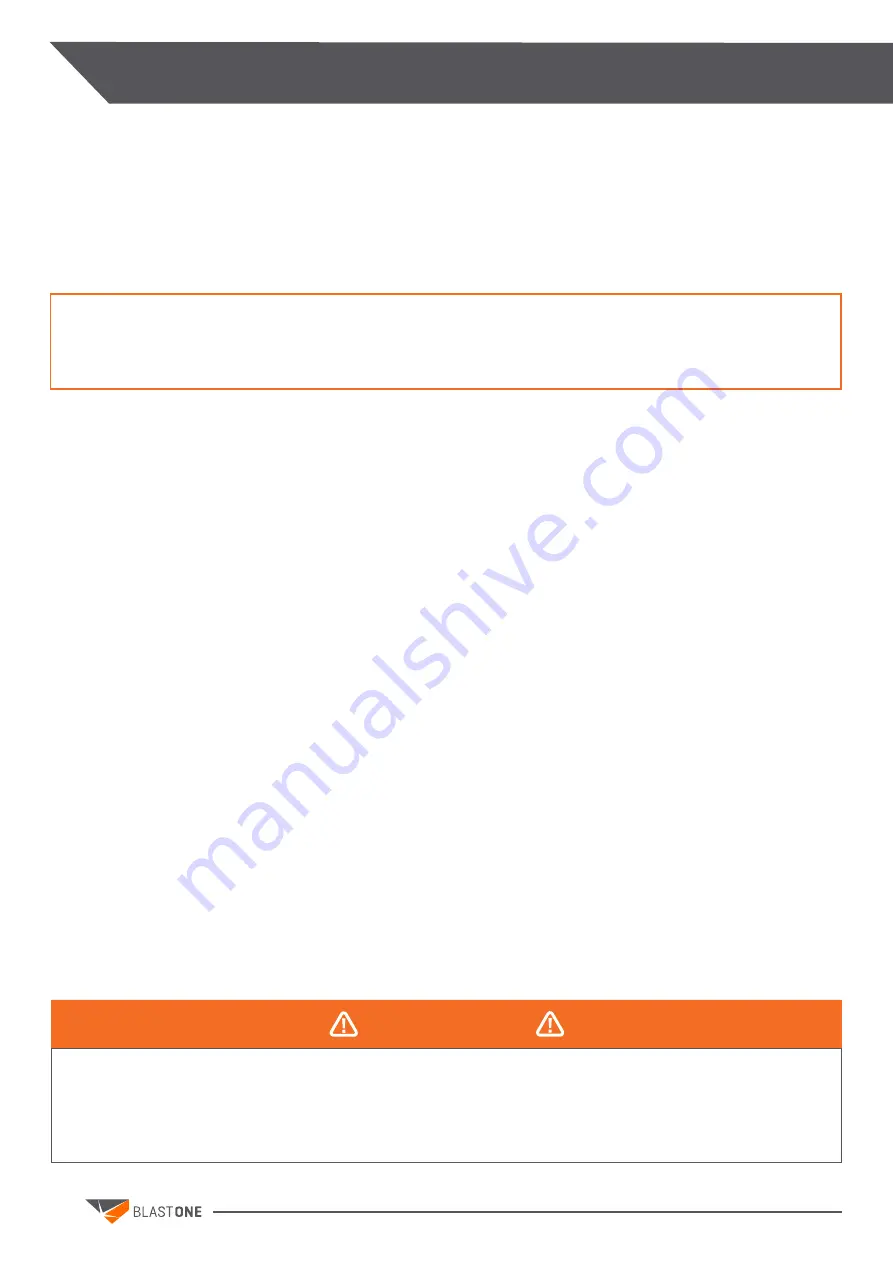
14
OPERATING PROCEDURE
PROPER SHUT DOWN PROCEDURE
It is recommended that when blasting has finished, the blast hose should be flushed free of all
abrasive and water. Shut the union ball valve and set the system to dry blast and activate the
deadman. This will only take 20 to 30 seconds, depending on the length of the blast hose. When the
white haze is not observed at the nozzle, the hose is clear.
This is an important procedure, especially when working at heights. This blow through
prevents any residual water in the hose running backwards and accumulating at the Thompson
valve, resulting in a clogged valve.
DEPRESSURIZING THE POT
To release the pressure in the blast pot, close off the inlet ball valve, then open the blow down
ball valve. When all the air is released, the pop-up valve will drop, allowing abrasive to be added if
required.
WATER SUPPLY
Water supply with a positive head is required for the Mist Blaster™. You can achieve this by
positioning the fluid level of the reservoir above the water inlet of the pump or by providing a
pressurized fluid supply.
One way to achieve a pressurized fluid supply is with a water tank and 12V transfer pump. The
transfer pump should be connected to a fully charged 12V automotive or marine battery. When
operating in dry blast mode, ensure that the transfer pump is off. In addition, ensure that the
transfer pump is off when the Mist Blaster™ is not in use. Consult a BlastOne sales representative
about suitable water supply options.
WINTERIZING THE UNIT
When operating in near-freezing to freezing temperatures, it is vital that the necessary precautions
are taken to prevent any water freezing in the pipes of the Mist Blaster™. To prevent such freezing,
run windshield wiper fluid through the unit in place of water until only the windshield wiper fluid
exits the unit.
Airborne particles and loud noise hazard from exhaust air can cause serious injury and loss
of hearing. Stay clear of the blow down path. DO NOT place hands or other body parts in the
blow down air path. Make sure no personnel are in the blow down air path. Wear approved
eye and ear protection.
WARNING