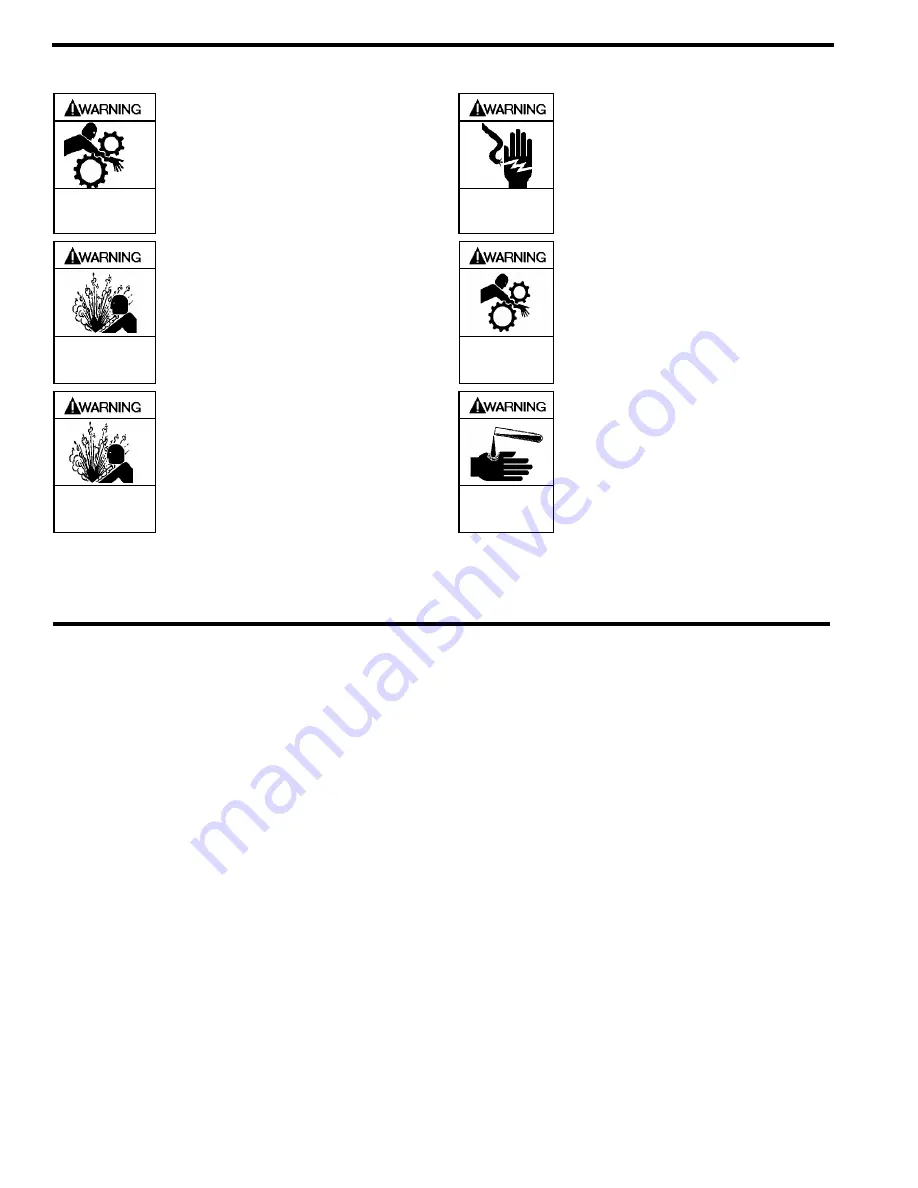
105-A00 Page 6/12
MAINTENANCE
Hazardous
machinery can
cause serious
personal injury.
FAILURE TO DISCONNECT AND
LOCKOUT ELECTRICAL POWER
BEFORE ATTEMPTING MAINTENANCE
CAN CAUSE SHOCK, BURNS OR
DEATH
Hazardous voltage.
Can shock, burn or
cause death.
FAILURE TO DISCONNECT AND
LOCKOUT ELECTRICAL POWER
BEFORE ATTEMPTING MAINTENANCE
CAN CAUSE SHOCK, BURNS OR
DEATH
Hazardous pressure
can cause personal
injury or property
damage
DISCONNECTING FLUID OR
PRESSURE CONTAINMENT
COMPONENTS DURING PUMP
OPERATION CAN CAUSE SERIOUS
PERSONAL INJURY, DEATH OR
MAJOR PROPERTY DAMAGE..
Do not operate
without guard
in place
OPERATION WITHOUT GUARDS IN
PLACE CAN CAUSE SERIOUS
PERSONAL INJURY, MAJOR
PROPERTY DAMAGE, OR DEATH.
Hazardous pressure
can cause personal
injury or property
damage
FAILURE TO RELIEVE SYSTEM
PRESSURE PRIOR TO PERFORMING
PUMP SERVICE OR MAINTENANCE
CAN CAUSE PERSONAL INJURY OR
PROPERTY DAMAGE.
Hazardous or toxic
fluids can cause
serious injury.
IF PUMPING HAZARDOUS OR TOXIC
FLUIDS, SYSTEM MUST BE FLUSHED
AND DECONTAMINATED, INSIDE AND
OUT, PRIOR TO PERFORMING SERVICE
OR MAINTENANCE
NOTICE:
MAINTENANCE SHALL BE PERFORMED BY QUALIFIED TECHNICIANS ONLY. FOLLOWING THE APPROPRIATE
PROCEDURES AND WARNINGS AS PRESENTED IN THIS MANUAL.
SCHEDULED MAINTENANCE
STRAINERS
Strainers must be cleaned regularly to avoid pump
starvation. Schedule will depend upon the application and
conditions.
LUBRICATION
NOTICE:
TO AVOID POSSIBLE ENTANGLEMENT IN MOVING PARTS
DO NOT LUBRICATE PUMP BEARINGS, GEAR REDUCER
OR ANY OTHER PARTS WHILE THE PUMP IS RUNNING
.
Pump bearings should be lubricated every one to twelve weeks
(AT MINIMUM), depending on the application, and operating
conditions.
Recommended Grease:
Exxon® - RONNEX MP Greas
e,
Mobile® - MOBILITH AW-2 (64353-6) Grease,
or
equivalent.
Greasing Procedure:
1. Remove the grease relief fittings (76A) from the bearing
covers (27A).
2.
SLOWLY
apply grease with a hand gun until grease begins
to escape from the grease relief fitting port. (76)
3. Replace the grease relief fittings (76A).
DO NOT overgrease pump bearings. While it is normal for
some grease to escape from the grease tell-tale hole after
lubrication, excessive grease on pumps equipped with
mechanical seals can cause seal failure.
Summary of Contents for XLW1 1/2
Page 11: ...105 A00 Page 11 12 NOTES...