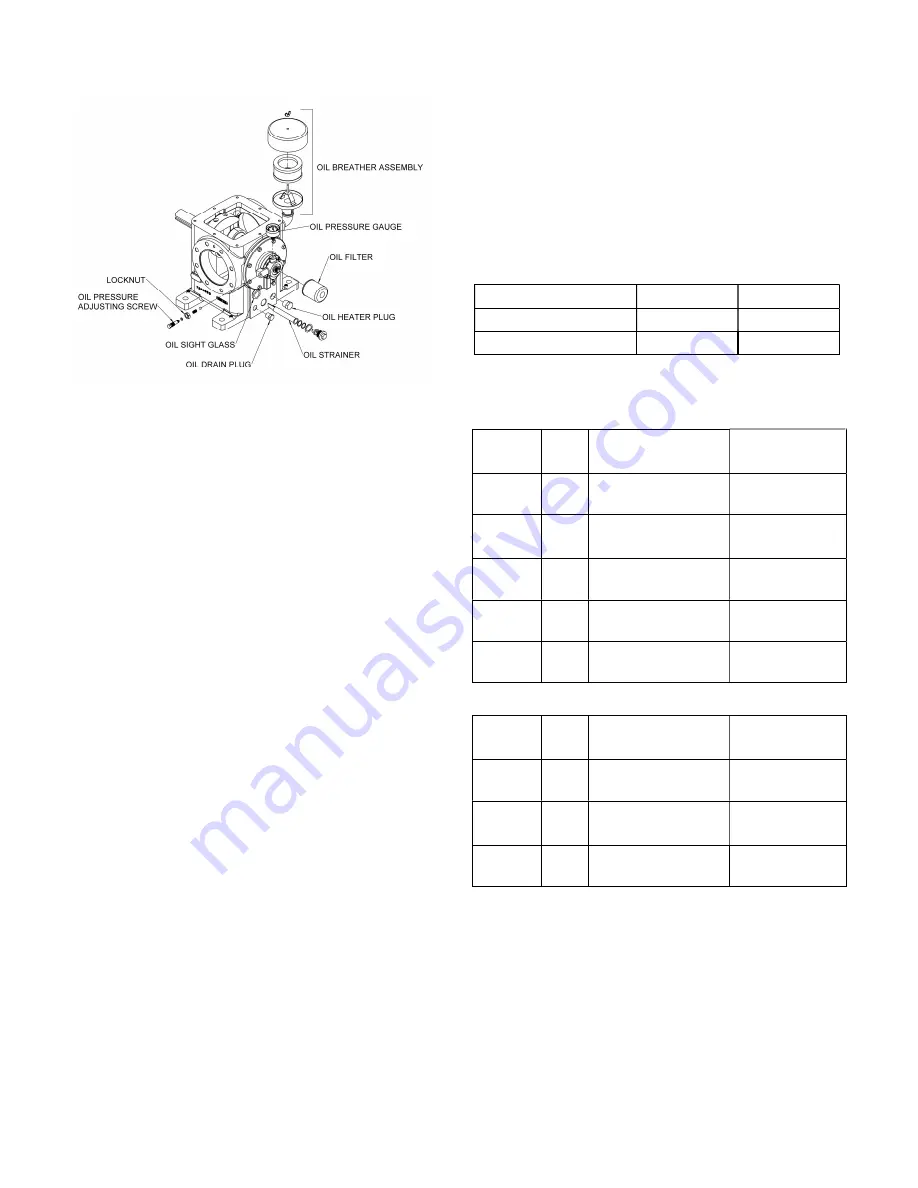
MAINTENANCE
CB6A-210 page 16/32
Figure 5: Compressor Lubrication System
C
RANKCASE LUBRICATION
Change the crankcase oil every 1,000 hours or 180 days,
whichever is shorter. Under severe dusty, sandy or wet
operating conditions, the oil should be changed every
500 hours or every 90 days.
If the crankcase oil becomes contaminated or diluted
due to gas leakage past the packing seals, the oil must
be changed more frequently. In such cases, change
the packing seals as soon as possible.
Non-detergent oils are recommended. Detergent oils
can be used providing the gas being handled does not
react with the detergent in the oil. If using a detergent
oil, be sure there is not a compatibility problem.
Ammonia, amine and imine gases are known to react
with many of the detergents in oil.
The oil used, detergent or non-detergent, should be
of high quality such as API grade SJ, SL, SM, SN or
similar.
API grade SA, SB, SC or similar oils should never
be used. Recycled oils should never be used.
Synthetic oils are acceptable; use the same guidelines
as mineral based lubricants. Consult factory for special
lubricating requirements.
Before changing the oil, bring the compressor up to
normal operating temperature. Remove the crankcase
drain plug and drain the oil into an adequately sized
container. Remove the oil pickup screen and clean in a
suitable solvent. When reinstalling the pickup screen,
inspect the metal gasket and the O-ring for damage,
replacing as necessary. If equipped, replace the external
oil filter. See
Figure 5
.
Oil Cooler
The NGH100 compressor is supplied with an oil cooler
and is required. See OIL COOLING AND CONTOL.
Refill the crankcase via the vent pipe or the crankcase
cover. A sight glass is located on the lower portion of the
crankcase below the oil filter. This should register at the
halfway mark.
DO NOT OVERFILL THE CRANKCASE!
The oil pump on these models will operate in either
direction of crankshaft rotation.
Models
Quarts
Liters
NGH100
4
3.785
NGH100 w/oil cooler
5
4.732
Table 7 - Oil Capacity
Mineral Based Oil - API Grade SN, SM, SL, SJ
ISO
Grade
SAE
Ambient
Temperature
Product
(or equivalent)
150
40
120°F and Above
(49°C and Above)
Mobil® Rarus
429
100
30
80°F to 120°F
(27°C to 49°C)
Mobil® Rarus
427
68/46
20
32 to 80°F
(0 to 27°C)
Mobil® Rarus
426/425
32
10
0 to 32°F
(-18 to 0°C)
Mobil® Rarus
424
22 - 15 5 - 0
Below 0°F
(-18°C)
NA
Synthetic Oil
ISO
Grade
SAE
Ambient
Temperature
Product
(or equivalent)
150
40
120°F and Above
(49°C and Above)
Mobil® Rarus
829
100
30
80°F to 120°F
(27°C to 49°C)
Mobil® Rarus
827
68
20
32 to 80°F
(0 to 27°C)
Mobil® Rarus
SHC 68
Table 8 - Oil Viscosity
SETTING THE OIL PRESSURE
(see Figure 5)
1. The oil pressure should be about 50 psig
(3.45 Barg).
2. Loosen the locknut.
3. Increase the pressure setting by turning the
adjusting screw inward, CLOCKWISE.
4. Decrease the pressure setting by turning the
adjusting screw outward, COUNTER-CLOCKWISE.
5. Retighten the locknut.
Summary of Contents for NGH1013
Page 11: ...INSTALLATION CB6A 210 page 11 32 Figure 4 Recommended Optional Oil Cooler Assembly...
Page 15: ...MAINTENANCE CB6A 210 page 15 32...
Page 18: ...COMPRESSOR DISASSEMBLY CB6A 210 page 18 32 Figure 7 Upper Compressor Assembly...
Page 19: ...COMPRESSOR DISASSEMBLY CB6A 210 page 19 32 Figure 8 Lower Compressor Assembly...
Page 29: ...DECLARATIONS CB6A 210 page 29 32...
Page 30: ...DECLARATIONS CB6A 210 page 30 32 Insert ATEX cert...
Page 31: ...CB6A 210 page 31 32 NOTES...