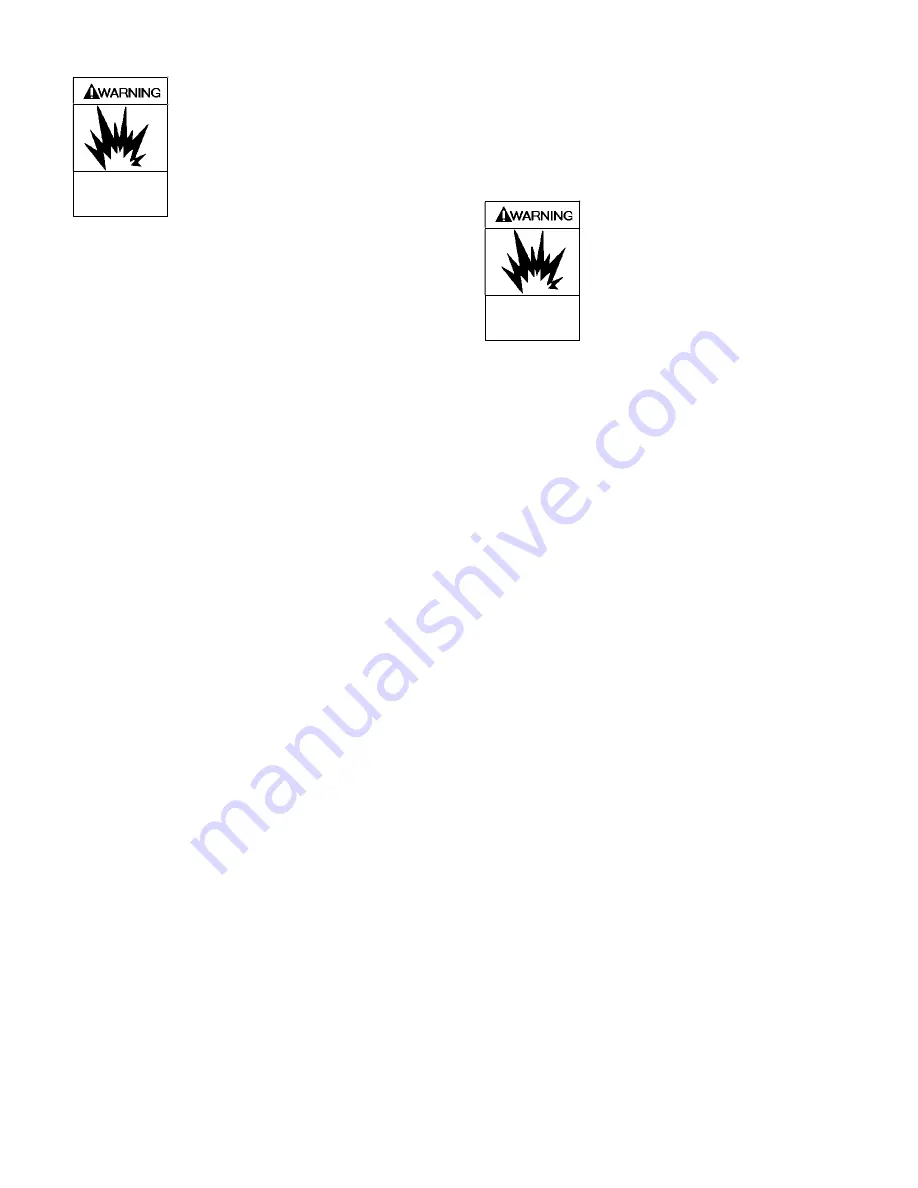
INSTALLATION
CB6A-210 page 10/32
Excessive gas recirculation using suction
valve unloaders can be a source of
ignition in explosive atmospheres
causing severe personal injury or death
Hazardous gases
can cause property
damage, personal
injury or death
3. Do not place a restrictive device such as a back check
valve in the suction line near the compressor. If such
a device must be installed, the volume in the piping
between the device and the compressor must be at
least 10 times the cylinder swept volume.
LIQUID TRAPS
Compressors handling gases that contain condensates or
other liquids MUST be protected from entry of the liquid.
Liquid can also enter the compressor from the discharge
piping, particularly if the piping slopes down toward the
compressor. To prevent liquid from entering the
compressor and causing major damage, it is necessary to
carefully consider the system design and have strict
procedures for operation.
NOTICE: Liquid in the compressor cylinder can cause
destruction of the compressor.
Suction liquid traps collect liquid entrained in the suction
gas stream, preventing it from entering the compressor.
The most common liquid trap is an ASME code vessel
(approx. 12" diameter X 50" tall) fitted with an internal
stainless steel mist pad, a relief valve, a manual drain
valve, and one or two electric float switches. This type trap
is needed if level gauges or automatic drain systems are to
be used.
If the liquid level rises too high in the trap, a float switch is
tripped, sending a signal to stop the compressor or sound
an alarm. The trap must then be drained before the
compressor can be restarted. The cause of the high liquid
level should be found and the problem corrected.
TEMPERATURE SWITCHES
Excessive discharge temperature is a leading cause of
premature component failure and is often an early warning
sign of impending problems.
Optional temperature switches should be installed with a
thermowell as close to the compressor discharge as
possible. The switch should be set to actuate at a
temperature just above the maximum operating
temperature of the compressor.
ATEX compliant compressors
must
have a temperature
switch installed.
LOW OIL PRESSURE SWITCHES
Loss of crankcase oil pressure is a rare occurrence, but
can result in costly damage. An optional low oil pressure
switch set at about 15 psig (1 bar-g) may be installed to
shut down the compressor in the event of a lubrication
failure. A 10 second delay timer should be used to lock the
low oil pressure switch out during compressor startup.
PRESSURE SWITCHES
Pressure switches may be installed in the suction or
discharge gas stream as protective devices, for
compressor control, or for other uses varying with each
application and system design.
OIL COOLING AND CONTROL
Oil temperature and pressure monitoring is recommended
on all units. An increase in oil temperature can be caused
by oil breakdown, improper filtration, or dirty oil.
An oil cooler is recommended on all machines running at
1200 or more RPM. An oil cooler is typically supplied with
these units and should be installed using an oil cooler
sandwich adaptor (installed on oil pump cover).
A crosshead guide oil injection system is supplied and
installed on all machines.
WARNING:
IF OIL COOLER SANDWICH ADAPTOR
IS INSTALLED, SANDWICH ADAPTOR MUST BE
CONNECTED TO AN APPROVED OIL COOLER. IF OIL
COOLER
SANDWHICH
ADAPTOR
IS
NOT
CONNECTED TO AN APPROVED OIL COOLER, THE
SANDWICH ADAPTOR MUST BE REMOVED FROM
COMPRESSOR ASSEMBLY BY A QUALIFIED
TECHNICIAN. FAILURE TO DO SO WILL
POTENTIALLY RESULT IN LOW OIL PRESSURE,
WHICH MAY RESULT IN CATASTROPHIC DAMAGE
TO THE COMPRESSOR.
To Remove Oil Cooler Sandwich Adaptor (See Figure
4):
1: Remove Oil Filter from assembly.
2: Remove Oil Filter Adaptor from assembly.
3: Remove Oil Cooler Sandwich Adaptor and O-Ring from
assembly
4: Assure that Oil Filter Fitting is tight.
5: Reassemble Oil Filter to Oil Filter Fitting.
TIP:
Fill Oil Filter with approved compressor oil per
Table
8
to help with oil system priming at compressor
startup.
Optional liquid trap level switches,
temperature switches, pressure
switches or other electrical devices
must be properly specified for
applications using explosive gases.
Hazardous gases
can cause property
damage, personal
injury or death
Summary of Contents for NGH1013
Page 11: ...INSTALLATION CB6A 210 page 11 32 Figure 4 Recommended Optional Oil Cooler Assembly...
Page 15: ...MAINTENANCE CB6A 210 page 15 32...
Page 18: ...COMPRESSOR DISASSEMBLY CB6A 210 page 18 32 Figure 7 Upper Compressor Assembly...
Page 19: ...COMPRESSOR DISASSEMBLY CB6A 210 page 19 32 Figure 8 Lower Compressor Assembly...
Page 29: ...DECLARATIONS CB6A 210 page 29 32...
Page 30: ...DECLARATIONS CB6A 210 page 30 32 Insert ATEX cert...
Page 31: ...CB6A 210 page 31 32 NOTES...