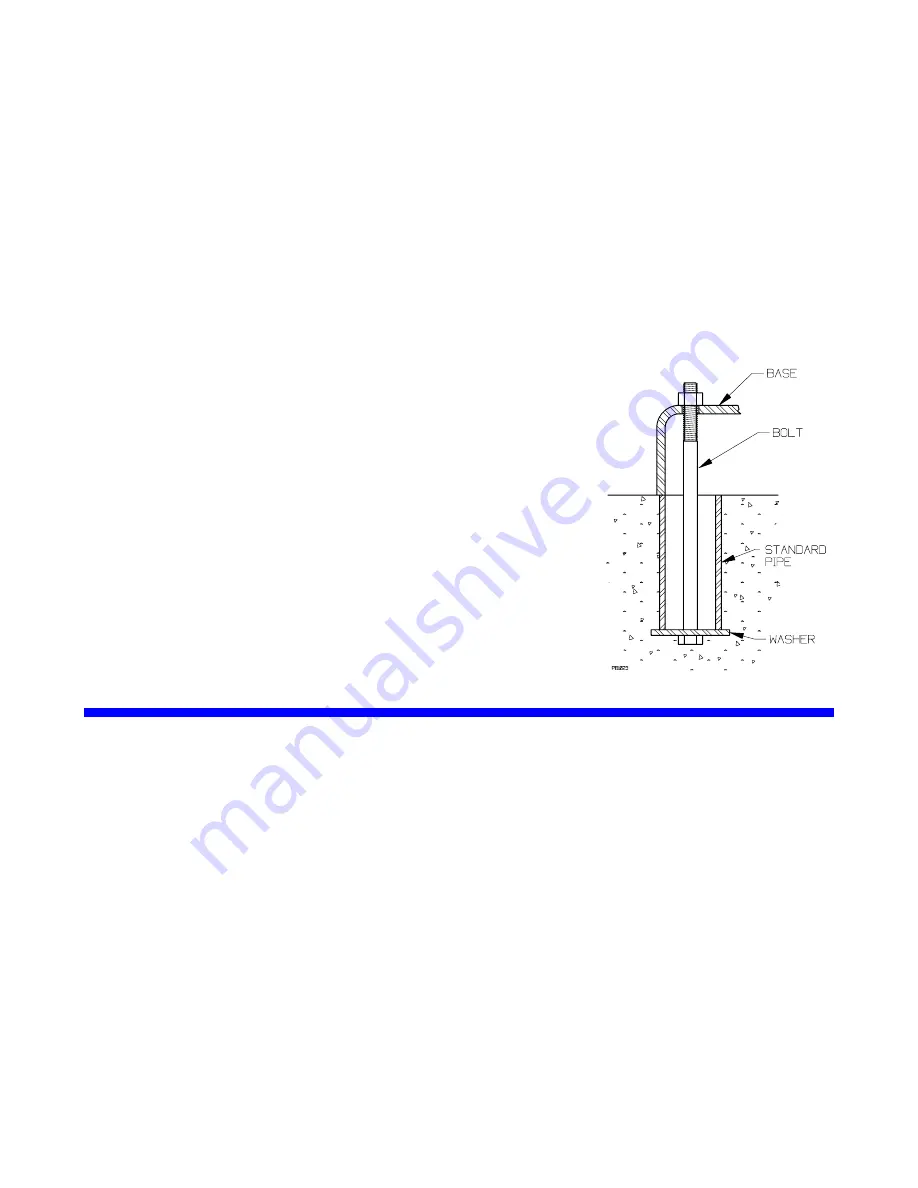
CB-9A-040 page 8
INSTALLATION
LOCATION AND PIPING
Compressor life and performance can be significantly reduced when installed in an improperly designed system.
Before starting layout and installation of the piping system, consider the following suggestions:
1.
A strainer should be installed in the inlet line to protect the compressor from foreign matter. A #30 mesh
screen or finer is recommended. Strainers must be cleaned regularly-once every 180 days, or more
frequently if the system requires.
2.
All piping must be leak free to a pressure of 1.5 times the maximum system pressure.
3.
Expansion joints, placed within 36" (0.9 m) of the compressor, will compensate for expansion and
contraction of the pipes.
4.
Piping must be well supported so that it does not spring away or drop down when flanges or union joints
are disconnected.
5.
Both suction and discharge piping should slope down from the compressor. The compressor should not
be placed at a low point in the piping system.
MOUNTING THE COMPRESSOR UNIT
A solid foundation reduces noise and vibration, and will improve
compressor performance. On permanent installations it is recommended
the compressor be secured by anchor bolts as shown. This arrangement
allows for slight shifting of position to accommodate alignment with the
mounting holes in the base plate.
For new foundations, it is suggested that the anchor bolts be set in
concrete. When compressors are to be located on existing concrete floors,
holes should be drilled into the concrete to hold the anchor bolts.
NOTE: To keep vibration at a minimum, in addition to a solid concrete
foundation it is important that the concrete be located on a stable soil
foundation. The base should have complete contact along its entire length
with the foundation. Visible separations can result in vibrations which are
magnified in the upper part of the unit.
Pipe Type Anchor Bolt-Box
OPERATION
PRE-STARTUP CHECK LIST
1.
After the compressor is installed in the system, a complete leak test should be performed on both the
compressor and the piping.
2.
Check the alignment of the pipes to the compressor. Pipes should be supported so that they do not spring
away or drop down when flanges or union joints are disconnected.
3.
If V-belt driven, check the alignment of the motor and the compressor sheaves. The faces of the sheaves
must be parallel.
4.
It is recommended that pressure gauges be installed in the discharge and inlet lines. These can be used
to check actual suction and discharge conditions after startup.
5.
Check the electrical connections for proper wiring, grounding, etc.
6.
Blackmer compressors are shipped from the factory without oil in the crankcase. Fill with a high quality oil
of the proper viscosity (see "Lubrication").
7.
Disconnect the power and remove the nameplate. Squirt oil onto the crosshead guide bores and rotate
the compressor by hand to verify smooth operation.
8.
Ensure that all guards in properly in place.
Summary of Contents for HD172A
Page 23: ...CB 9A 040 page 23 NOTES...