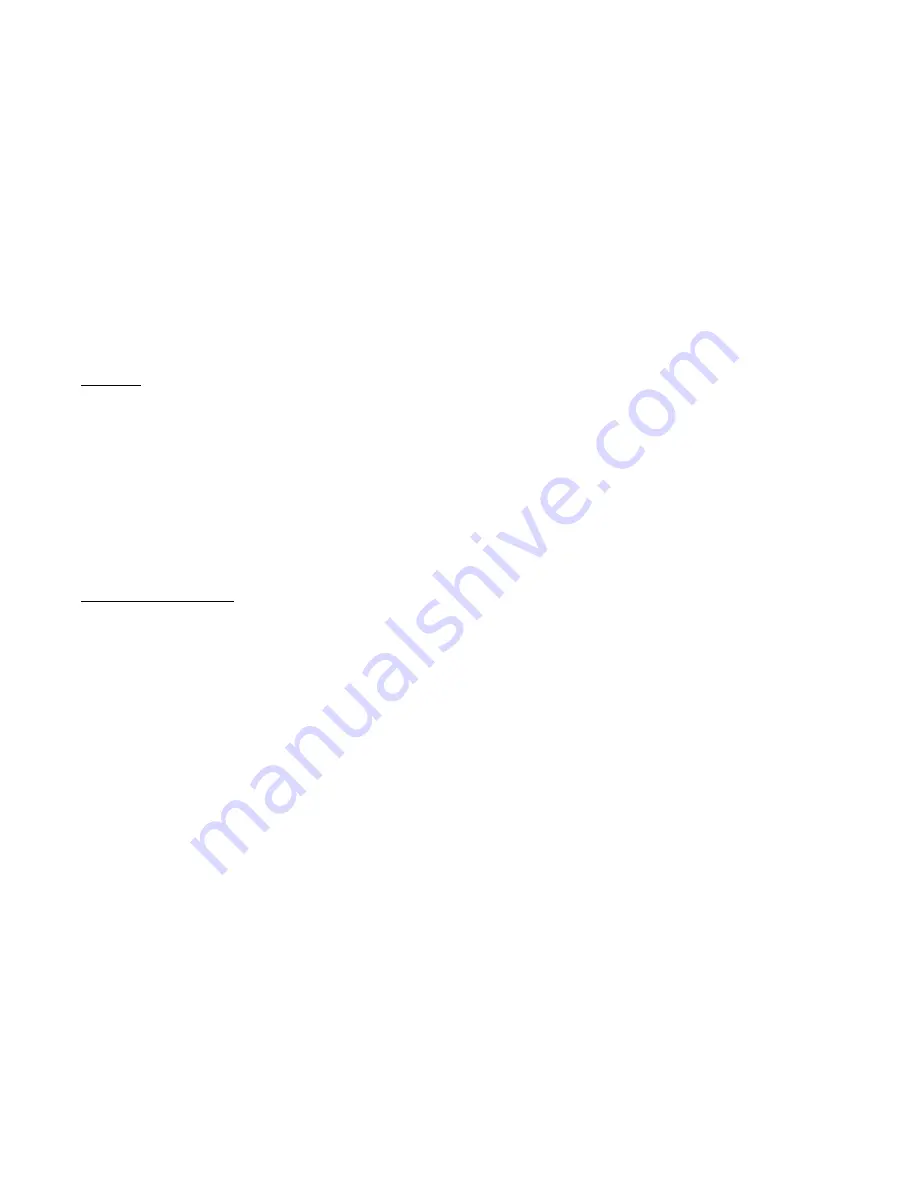
5
ASSEMBLY
Little, if any, assembly is required of this jack; refer to figure 1 and figure 2 for components location. Familiarize yourself
with the illustrations in the operator's manual. Know your jack and how it operates before attempting to use. Assemble
handle to the handle fork. Secure the handle with provided bolt to prevent inadverent removal. Connect to adequate air
source and ensure air control valve is secured into the pipe nipple of the jack.
OPERATION
Lifting
1. Use wheel chocks to help prevent inadvertent shifting and movement of vehicle being lifted.
2. Position the jack near lift point. Consult vehicle service manual for the location of recommended lift points.
3. Close the release valve by turning the handle mounted knob, clockwise until it is firmly closed.
Important: Never
wire, clamp or otherwise disable the lift control valve to work by any means other than by using
the operators hand.
Caution:
Use only saddle extenders (if equipped) provided and recommended by the manufacturer of the jack. Lift
only on the manufacturer’s recommended lift points and in accordance with the published guidelines in your vehicle
owners manual. Always use jack stands to support the load immediately after lifting.
4. Squeeze the lift control valve until saddle contacts load. Check to ensure proper saddle/lift point alignment. To end
cycle, simply release the grip on the lift control valve.
5. Raise load to desired height, then immediately transfer the load to appropriately rated support devices such as
jack stands.
Lowering
1. Raise load high enough to clear the jack stands, then carefully remove jack stands (
always
used in pairs).
2. Slowly turn the release valve counterclockwise, but no more than 1/2 turn.
If the load fails to lower:
a. Use another jack to raise the vehicle high enough to reinstall jack stands.
b. Remove the malfunctioning jack and then the stands.
c. Using the functioning jack, lower the load by turning the release valve counterclockwise, but no more than 1/2 turn.
3. Push ram and handle sleeve down to reduce exposure to rust and contamination after removing jack from under
the load.
MAINTENANCE
Important
: Use only a good grade hydraulic jack oil. We recommend Hein-Werner HW93291 hydraulic oil. Avoid
mixing different types of fluid and NEVER use brake fluid, turbine oil, transmission fluid, motor oil or glycerin. Improper
fluid can cause premature failure of the jack and the potential for sudden and immediate loss of load.
Adding oil
1. Lower saddle fully and fully depress piston.
2. Set jack in its upright, level position.
3. Remove oil filler screw.
4. Fill with oil until just below the rim of the oil filler screw hole.
5. Reinstall the oil filler screw.
Changing oil
For best performance, replace the complete hydraulic fluid annually.
1. Remove the oil filler screw with saddle fully lowered.
2. Lay the jack on its side and drain the fluid into a suitable container.
3. Fill with oil until just below the rim of the oil filler screw hole.
4. Reinstall the oil filler screw and cover plate.
Note:
Dispose of hydraulic fluid in accordance with local regulations.