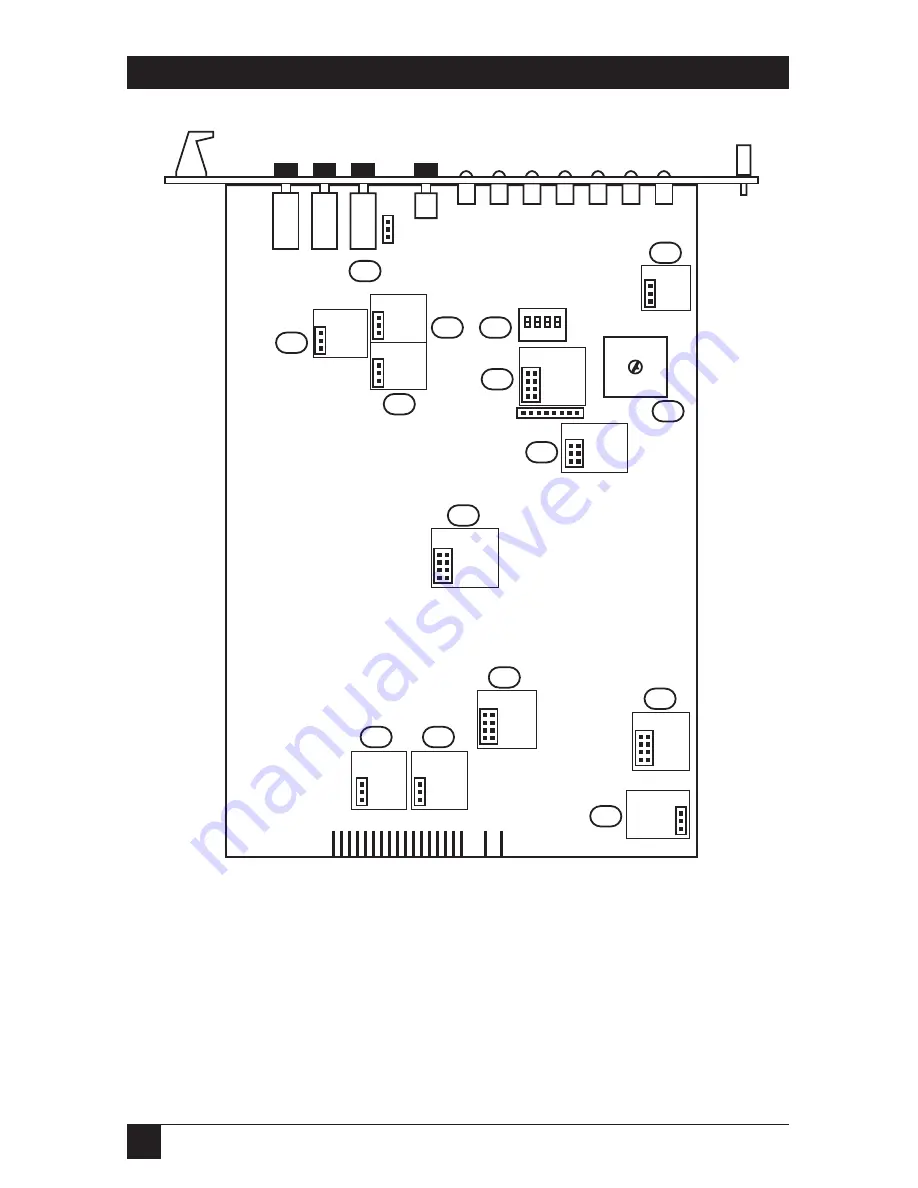
34
LDM-MR19.2
Figure 4-3. The LDM-MR19.2 card’s board layout.
1
2 3 4
5
6
78
9
0
1 2 3 4
PIN 21
(RLB)
ENABL
DIS
PIN 18
(AN.LP)
ENABL
DIS
XMT IMPD
600
300
150
LOW
CHAS GND
DIS.
CONN.
RCV IMPD
600
300
150
HIGH
XMT LEVEL
0dbm
-3dbm
-6dbm
-9dbm
XMT TIMING
INT.CK
EXT.CK
RCV.CK
ASYNC
CTS DELAY
0 msec
8 msec
64msec
AGC
CNTRL
ON
2/4 WIRE
2W
4W
CARRIER
CNTRL
ON
SWITCH
DIS
EN
V54 DLY
ON
OFF
ASY LENGTH
DATA RATE
REM ANA DIG
LEDs
10
9
7
8
12
6
4
2
15
14
1
13
3
5
11
RPF