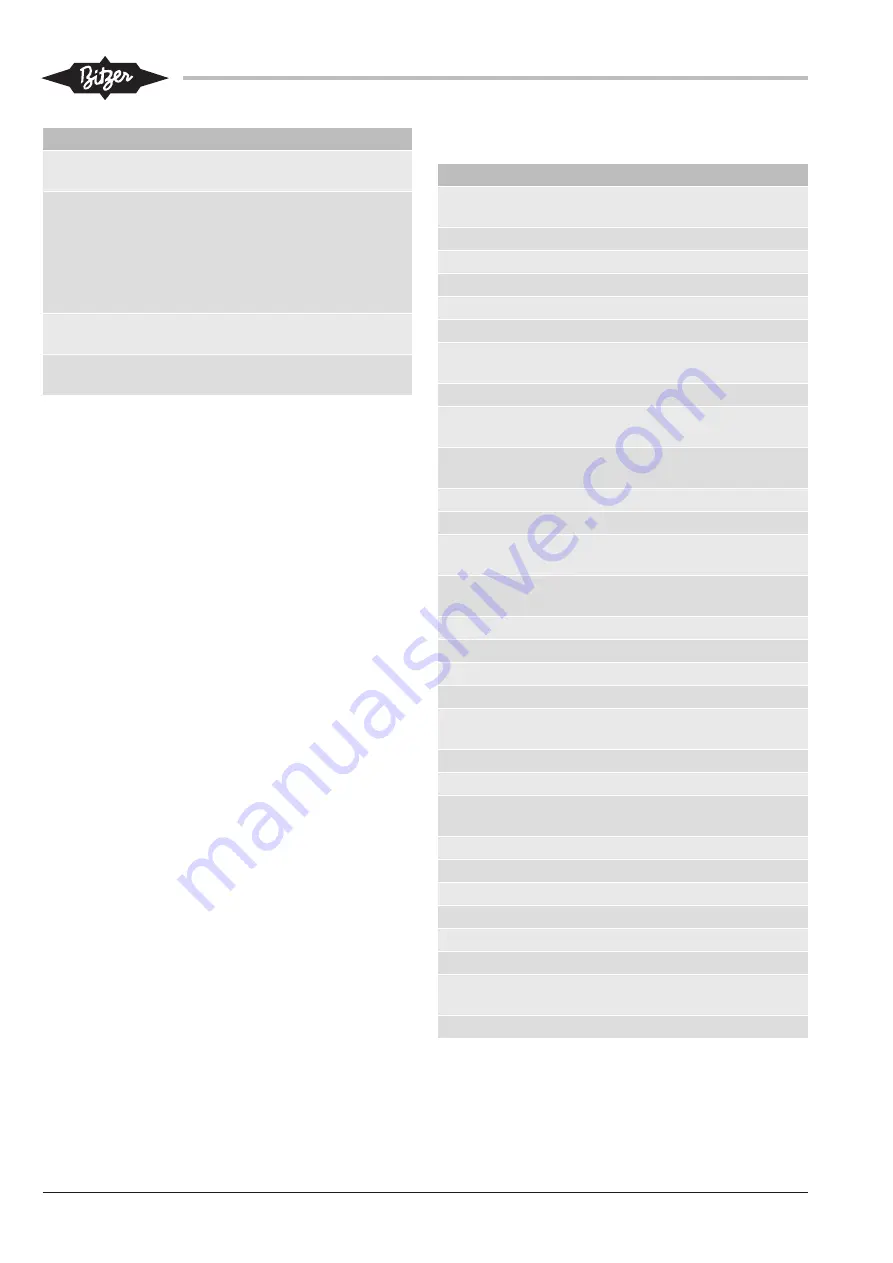
KT-230-1
8
Monitored function
Measuring sensor
High pressure (option)
High pressure transmitter
(B6)
Oil supply (standard)
Oil level monitoring with
OLC-D1 (F4) on 4VES-6Y
to 4NES-20(Y)
Differential oil pressure
monitoring with DP-1 (F4)
on 4JE-13Y to 8FE-70(Y)
Cycling rate of the
compressor (standard)
Integrated in CM-RC-01
Temperature at any
place (option)
Optional temperature
sensor
The compressor control module compares the meas-
ured values with the the programmed data, sending
signals via Modbus and indicating the operating condi-
tion by means of differently coloured LEDs, see chapter
Protective functions, page 13. The compressor will be
shut off in case of operation beyond the application lim-
its, lack of oil or excessive motor temperature. The cyc-
ling rate and the measured value of the optional tem-
perature sensor are monitored and recorded.
5
Electrical connection
Keep the compressor control module energized when
the motor is not running. If necessary, the module activ-
ates the oil heater, thus ensuring the lubricity of the oil
even after a long standstill period.
De-energize the module only if you plan a long stand-
still period of the compressor or for maintenance pur-
poses.
5.1
Schematic wiring diagram for part winding start
Schematic wiring diagram, see figure 2, page 9. In
the event of direct start, path 4 is omitted: contactor K2
and thermal overload relay F14 as well as the cable
connection on the terminal strip CN2, terminal 1. For
soft start and operation with frequency inverter, only
one contactor is required.
For operation with frequency inverter, please observe
the following: Emit the release signal to the compressor
control module only after charging of the DC link during
the first switch-on.
5.2
Schematic wiring diagram for star-delta start
In the event of star-delta start, the motor contactors are
not connected according to the terminal labelling on the
CM-RC-01, see figure 3, page 10.
5.3
Legend for the schematic wiring diagrams
Abbr. Component
B1
Command for compressor start (release sig-
nal from system controller)
B6
High pressure transmitter
B7
Low pressure transmitter
F1
Main fuse
F2
Compressor fuse
F3
Control circuit fuse
F4
Oil monitoring: 4VES-6Y .. 4NES-20(Y): OLC-
D1 / 4JE-13Y .. 8FE-80(Y): DP-1
F5
High pressure switch
F13
Thermal overload relay "Motor" (1st part wind-
ing and Y/Δ)
F14
Thermal overload relay "Motor" (2nd part
winding)
F17
Control transformer fuse
H3
Signal lamp "Collective fault"
K1
Contactor "1st part winding" (PW) or main
contactor (Y/Δ)
K2
Contactor "2nd part winding" (PW) or delta
contactor (Y/Δ)
K3
Star contactor (Y/Δ)
M1
Compressor
M2
Additional fan
Q1
Main switch
R1 ..
6
PTC sensor in motor winding
R7
Discharge gas temperature sensor
R8
Oil heater
R11
Optional temperature sensor (not included in
the scope of delivery)
S1
Control switch (on/off)
S2
Fault reset of CM-RC-01
T1
Control transformer (example for 230 V)
Y1
Solenoid valve "Start unloading SU"
Y3-1
Solenoid valve "1st capacity regulator CRII"
Y3-2
Solenoid valve "2nd capacity regulator CRII"
Y3-3
Solenoid valve "3rd capacity regulator
CRII" (only for BE6 compressors)
Y5
CIC injection valve
Tab. 2: Components of the schematic wiring diagrams