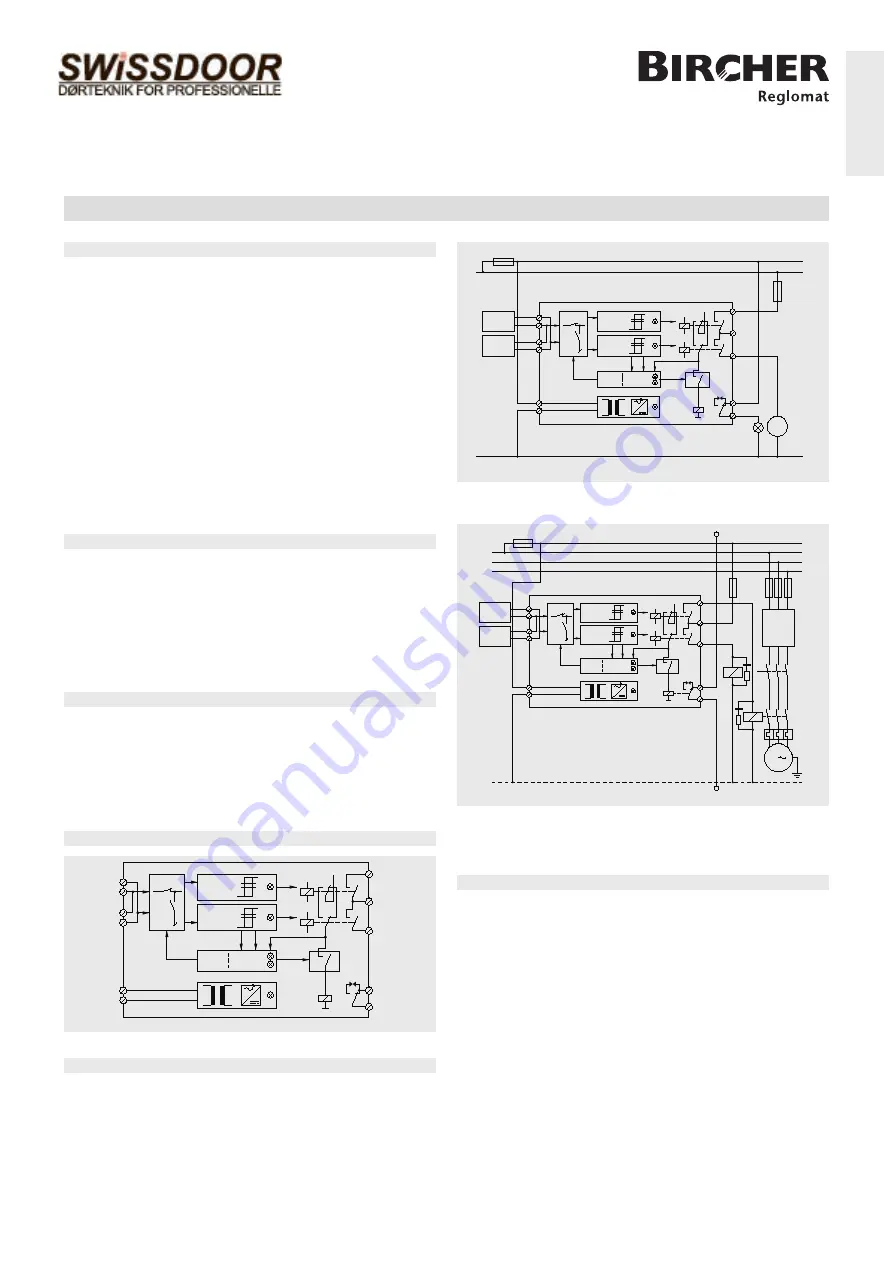
3
ESR-31, -31C / ESR-32, -32C
Switching Units ESR-3
Translation of the original instructions
General / Security Category
Safety systems in the Category 3 (EN ISO 13849-1) can be achieved with Switching
Units Type ESR-3. Safety edges and Safety Mats can be used as sensors.
The Switching Units together with the sensors are intended for use in industrial appli-
cations. For applications in connection with smal children, special sensors are re-
quired. Contact us for further details concerning such applications.
The Switching Unit has two input channels and accordingly sensors can be connected
to each single channel. The evaluation of both channels is completed with a redundant
technique. This means that two evaluation circuits are installed so that if one fails the
other ensures a certain Off condition. The fault will be immediately detected, or at the
latest with the next system startup, resulting in a system shutdown and error indi-
cation. The error indication relay contact opens on the ESR-31,-32 and closes on the
ESR-31C,-32C.
Activation of the sensor (safety function) causes both output relays to immediately
de-energise. On the ESR-31,-31C resetting can be achieved by pressing the “Reset”
button or disconnecting the power supply for a few seconds. On the ESR-32,-32C reset-
ting occurs when the sensor is no longer activated or also when the power supply is
disconnected for a short period. Each time the power supply is connected, a self-test is
initiated during which all the unit functions are checked.
Installation of the Switching Unit
The switching unit and sensors are to be installed and wired according to the appli-
cable local regulations. The min. sensor cable cross section is 0.5 mm
2
. The 11 pin so-
cket can be screwed on the mounting plate or snapped on to a DIN rail.
The switching units may only be installed in dry locations and must be provided with
drip-water protection. It is preferable that the unit be installed in a control cabinet with
a min. protection class of IP 54. Several switching units can be mounted in a row, but
it must be ensured that there is at least 2 cm of free space above and below the units
to ensure that heat from the power supply dissipates.
Connection of Sensors
Sensors, with a total length of up to 25 m and a total area of 5m2, can be connected to
each of both sensor inputs. The sensors are to be connected in series and the last must
have a termination resistor with a value of 8.2 kOhm.
If only one sensor input is used channel 2 must be jumpered or the error signal “Sensor
Error” is indicated. For this purpose the supplied 8.2 kOhm resistor should be connected
across terminals 7/9.
DE EN
209554R
01/16
Wiring and Connection Diagram
Wiring Suggestions
It is imperative to use the indicated fuses.They protect the relay contacts from melt ing
due to overload (F1, F2 max. 2A slow). Suppressors 220 Ohm/0,1 uF are to be
con nected across inductive loads. It is also to be observed that the error indication
relay contact is only used for data transfer and on no account to be utilised for switch-
ing off dangerous movements on machines and systems. This contact is not fault
monitored.
F1
P
N
+
22(5)
32(8)
14(3)
31(11)
12(4)
11(1)
21(6)
24(7)
34(9)
A1(2)
A2(10)
SM1
SR2
SR1
Sensor
1
Test Erorr
Reset
Sensor
2
F2
M
without auxillary
contactor
Single-phase drive. Circuit diagram with Switching Unit ESR-31C,-32C designed to illu-
minate the error indication lamp when a fault occurs (1/6 close).
+
22(5)
32(8)
14(3)
31(11)
12(4)
11(1)
21(6)
24(7)
34(9)
A1(2)
A2(10)
L1
L2
L3
N
F1
F2
F3–5
1
SM1
SR2
SR1
Sensor
1
Machine
control
Test Error
Reset
M
3
Sensor
2
Three-phase drive. Circuit diagram with Switching Unit ESR-31 showing error colecting
loop (1–6 open). By using Switching Unit ESR-31C it is possible to connect a signal
lamp as, for example, in the single-phase diagram.
Commissioning
a) Check the wiring. Are F1 and F2 installed with max. 2A slow fuse?
b) Before inserting the unit in the socket, it is advisable to measure the resistance
value between the connecting terminals 5/8 and 7/9. The value should be 8.2 kOhm
when the sensor is not active. Typical value between 7.5 and 9.0 kOhm.
c) Check the voltage information indicated on the unit type plate.
d) After the voltage has been connected, the self-test begins. The test phases are indi-
cated by various LED’s. After about 4 seconds the green LED “Operation” illumina-
tes, the system is operational.
e) Both yellow LED’s “Safety Function” will illuminate and both signal output relays
de-energise when one or more sensors are actuated. Now actuate the sensors at
different locations and observe if both yellow LED,s illuminate. The signal output
relays remain de-energised.
f) Push the “Reset” button (ESR-31,-31C). Start-up test commences.
g) If a terminal of the sensor input (e.g. 5 ) is opened thus interupting the signal con-
nection, the signal output relay de-energises and the red LED’s “System Error” and
“Sensor Error” illuminate. The error indication relay contact opens (or closes in the
case of the ESR-31C, -32C).
h) When the terminal is again closed, the error condition is maintained until, with ESR-
31,-31C, the reset button is actuated or the supply voltage is interrupted for a few
seconds. The self- test, described in d) now commences.
i) Repeat g) and h) with the other sensor input (e.g. 7).
Error collecting loop
+
5
8
3
11
4
6
1
SM1
SR2
SR1
7
9
2
10
Sensor
1
Test Error
Reset
Sensor
2
Supply
voltage
Drive
Error-
indication