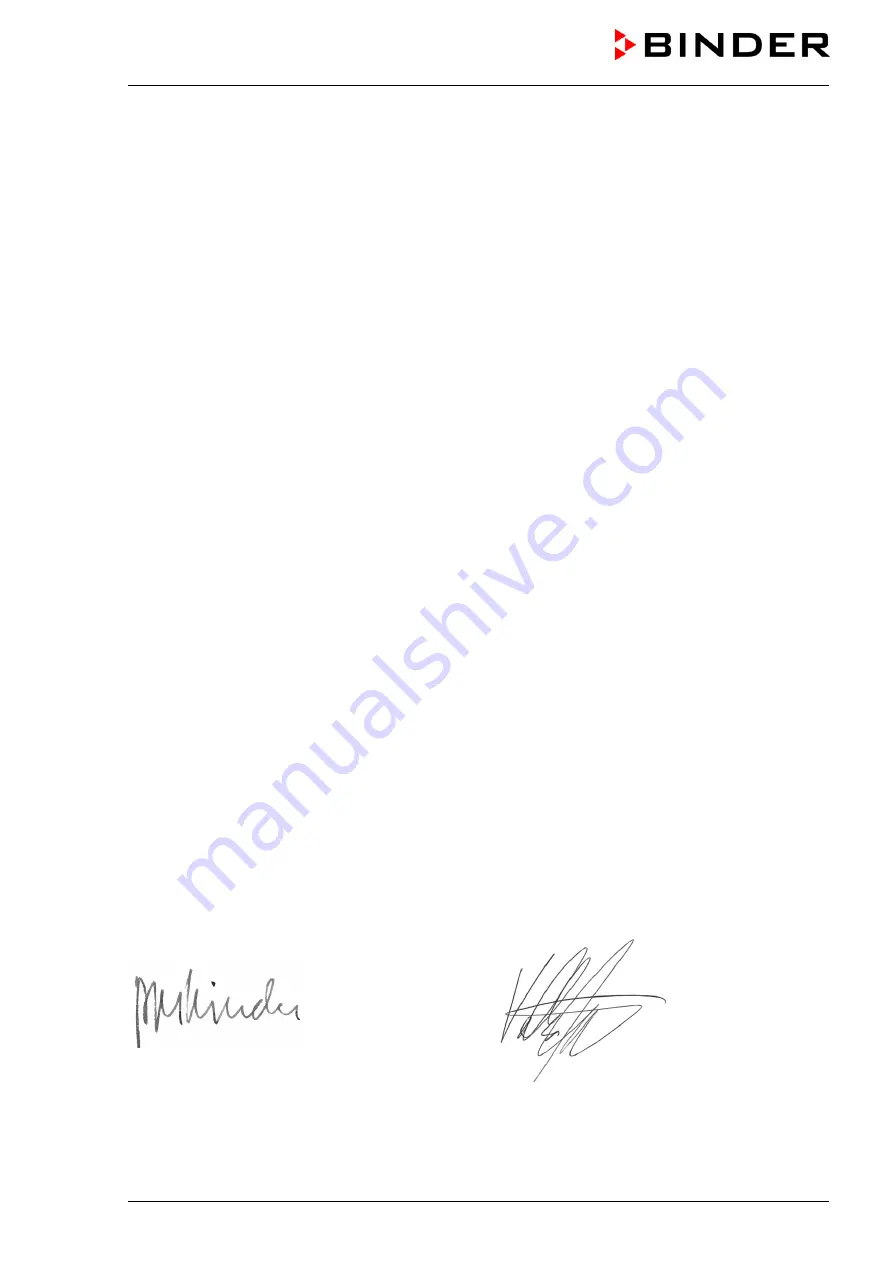
KBF-LQC (E5.2) 12/2010
page 3/106
Die oben beschriebenen Produkte sind konform mit folgenden harmonisierten Normen:
The products described above are in conformity with the following harmonized standards:
Les produits décrits ci-dessus sont conformes aux normes harmonisées suivantes:
Sicherheit / safety / sécurité:
EN 61010-1:2001
Sicherheitsbestimmungen für elektrische Mess-, Steuer-, Regel- und
Laborgeräte – Teil 1: Allgemeine Anforderungen
Safety requirements for electrical equipment for measurement, control,
and laboratory use – Part 1: General requirements
Règles de sécurité pour appareils électriques de mesurage, de régula-
tion et de laboratoire – Partie 1 : Prescriptions générales
EN 61010-2-010:2003
Sicherheitsbestimmungen für elektrische Meß-, Steuer-, Regel- und
Laborgeräte – Teil 2-010: Besondere Anforderungen an Laborgeräte für
das Erhitzen von Stoffen
Safety requirements for electrical equipment for measurement, control,
and laboratory use – Part 2-010: Particular requirements for laboratory
equipment for the heating of materials
Règles de sécurité pour appareils électriques de mesurage, de régula-
tion et de laboratoire. Partie 2-010 : Prescriptions particulières pour
appareils de laboratoire utilisés pour l’échauffement des matières
EMV / EMC / CEM:
EN 61326-1:2006 + Corr. 2008 Elektrische Mess-, Steuer-, Regel- und Laborgeräte – EMV-
Anforderungen. Teil 1: Allgemeine Anforderungen.
Electrical equipment for measurement, control and laboratory use –
EMC requirements. Part 1: General requirements.
Matériel électrique de mesure, de commande et de laboratoire – Exi-
gences relatives à la CEM. Partie 1: Exigences générales.
EN 61326-2-2:2006
Elektrische Mess-, Steuer-, Regel- und Laborgeräte – EMV-
Anforderungen. Teil 2-2: Besondere Anforderungen - Prüfanordnung,
Betriebsbedingungen und Leistungsmerkmale für ortsveränderliche
Prüf-, Mess- und Überwachungsgeräte in Niederspannungs-
Stromversorgungsnetzen.
Electrical equipment for measurement, control and laboratory use –
EMC requirements. Part 2-2: Particular requirements - Test configura-
tions, operational conditions and performance criteria for portable test,
measuring and monitoring equipment used in low-voltage distribution
systems.
Matériel électrique de mesure, de commande et de laboratoire – Exi-
gences relatives à la CEM. Partie 2-2: Exigences particulières - Confi-
gurations d’essai, conditions de fonctionnement et critères d’aptitude à
la fonction des matériels portatifs d’essai, de mesure et de surveillance
utilisés dans des systèmes de distribution basse tension.
D-78532 Tuttlingen, 04.02.2009
BINDER GmbH
P. M. Binder
Geschäftsführender Gesellschafter
Managing Director
Directeur général
V. Siegle
Leiter F & E
Head of R & D
Chef de service R&D
2 / 2