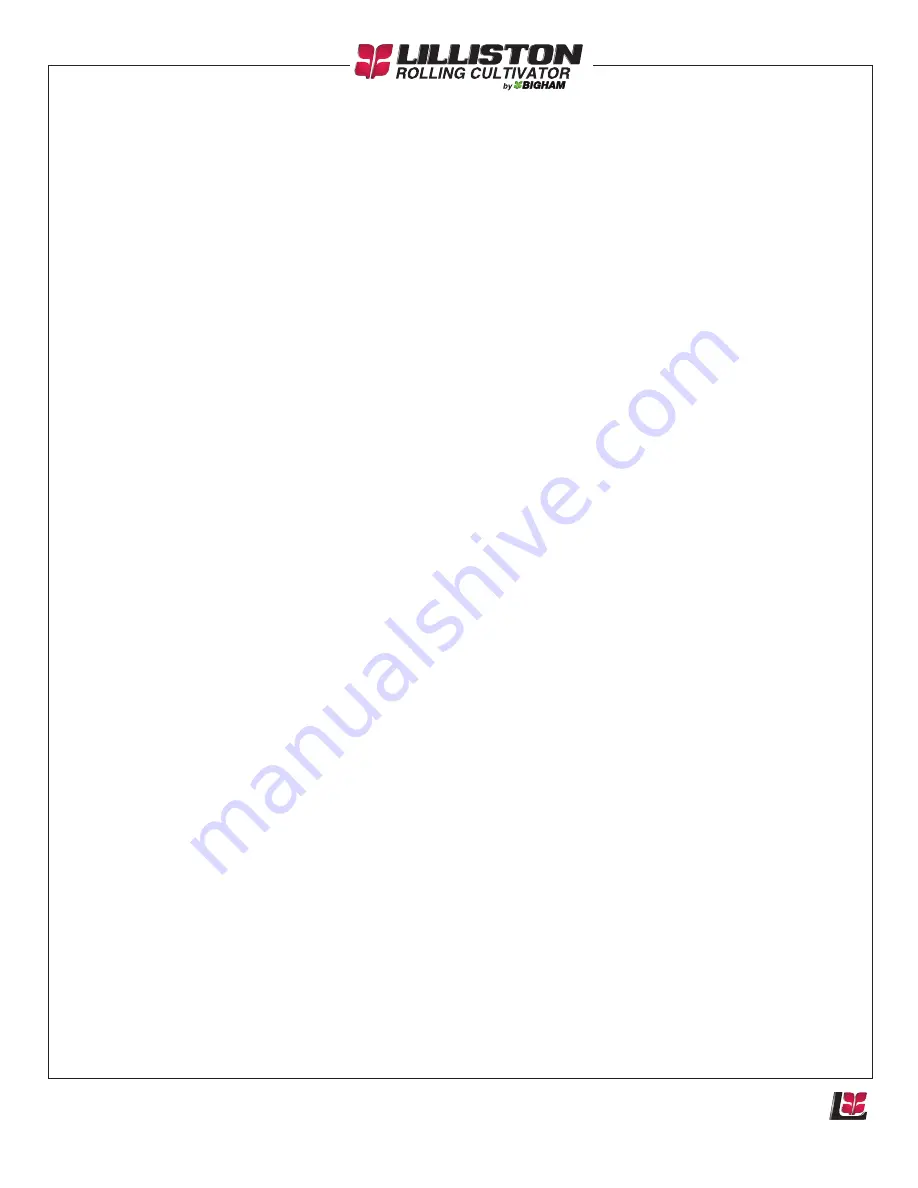
Page 17
Form # B15-790
®
®
®
•
All employees who work in the area where the energy control procedure(s) are utilized need to
be instructed in the purpose and use of the energy control procedure(s) and about the prohibition
against attempting to restart or reenergize machines or equipment that is locked or tagged out.
•
All employees who are authorized to lockout machines or equipment and perform the service
and maintenance operations need to be trained in recognition of applicable hazardous energy
sources in the workplace, the type and magnitude of energy found in the workplace, and the means
and methods of isolating and/or controlling the energy.
•
Specific procedures and limitations relating to tagout systems where they are allowed.
•
Retraining of all employees to maintain proficiency or introduce new or changed control methods.
OSHA outlines a six-step procedure for controlling hazardous energy:
•
Step 1:
Prepare for shutdown. It must be determined what type of power system is going to be
deactivated including electrical, hydraulic, pneumatic or other energy sources. Knowledge of
shut down methods is necessary.
•
Step 2:
Shutdown the equipment. This should be completed consistent with the
manufacturer’s instructions for the shutdown procedure and could be a simple as placing a
switch in the “off” position or pressing a button.
•
Step 3:
Isolate the equipment. This step involves closing of valves, throwing the main
disconnects or circuit breakers and disconnecting or capping any auxiliary power sources or
secondary electrical systems.
•
Step 4:
Apply the lockout/tagout device. This is done to prevent restoration of the flow of
energy and is done at all disconnect switches, valves or other energy isolating devices. Locks
are the preferred method of controlling energy and should be supplemented with tags.
Various lockout devices are available including group lockout hasps. Locks should be individually
assigned and have only one key.
•
Step 5:
Control the stored energy. This step includes the release, disconnect or restraint of any
residual hazardous energy which may be present and a check that all moving parts have stopped
moving. It may also include the installation of “pancakes” or blanking of pipe flanges, the
installation of ground wires to discharge electrical capacitors and the blocking or supporting
of elevated equipment.
•
Step 6:
Verify isolation of equipment. Double-check the steps and verify that the equipment
indeed has been shut down and that the lock and tag do control the stored energy. Employees
should be warned and the system tested, including pressing of all start buttons to assure that
the equipment will not start.
Summary of Contents for Lilliston Rolling Cultivator Generation 3
Page 9: ...Page 9 Form B15 790 FRONT REAR...
Page 49: ...Page 49 Form B15 790 Notes...
Page 50: ...Page 50 Form B15 790 Notes...
Page 51: ...Page 51 Form B15 790 Notes...
Page 52: ......