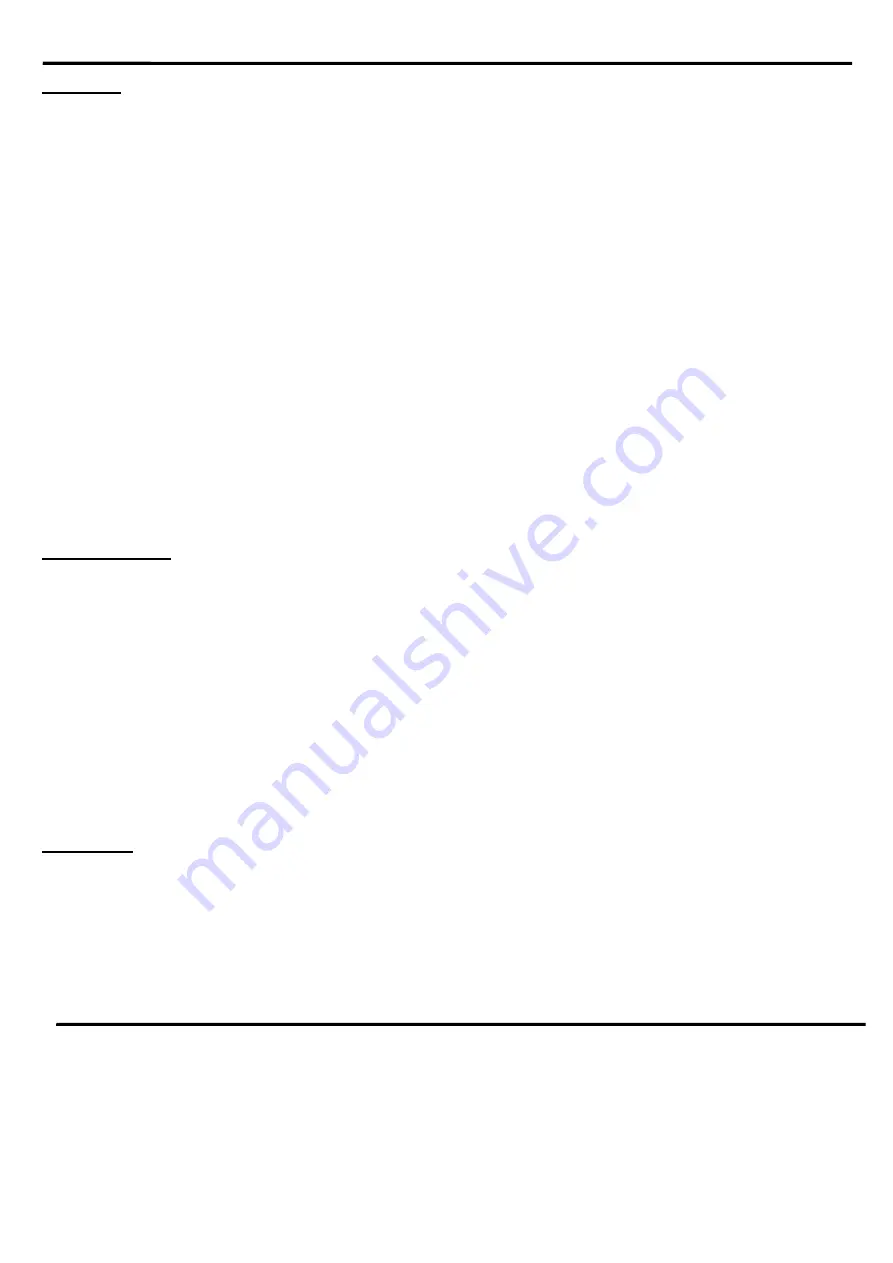
IS200 Electro-Hydraulic Actuator Positioner
Orange Instruments Limited.
Drwg. No.: 1357-007 Issue : K Date : 07/10/2013 Page :
5 of 9
Iss c - Certificate number added. Iss D - Ta changed to -20 to +60
Iss E - Details of fail modes, timers and retrans. O/P added. Retrans. Signal barrier changed to KFD0-CC-Ex1
Iss F
– Details of change in Max/min on & off times + addition of 10R in line with pos o/p –ve
Iss G
– Stepping times range change to allow finer adjustment 15/11/2007
Iss H
– CE Cert. of Conformity details added, Ta to –40degC, 60079:0,26 mods 25/06/2008
Iss J
– Harmonised standards in C of C modified to meet current status 04/08/2008
Iss K - Markings changed to meet EN 60079-0:2012 02/10/2103
ATEX Certified Equipment - Change Authority ATEX Manager ONLY
Calibration
Calibration can only be carried out local to the IS200 unit so it is essential to have either purged the area or to use IS signal
injection and measuring equipment. An alternative is to use the remote DCS to inject and read the actual position signal
and transfer the information by handheld radio. If this approach is used ensure that the radio is operated 2m or more from
the IS200 and associated wiring.
A command signal is required, normally in the range 4-20mA (Terms 20+ and 21-) and a DVM with a 0-10V range to read the
retransmitted position signal (Terms 18+ and 19-).
1. Press the CALIBRATE button, and hold until the CALIBRATE LED goes out. When the button is released, the
CALIBRATE LED will flash briefly once per second and the Manual LED will light.
2. The positioner has been switched automatically into Manual, non-stepping mode so use the INCREASE /
DECREASE buttons to set the actuator to the required position for the minimum, 4mA command signal. This
position can be either fully open or fully close, or indeed anywhere in the mechanical range of the actuator.
3. Set the command signal to 4mA.
4. Adjust the CAL1 potentiometer to give the required output for the chosen position. Note that this not need be 0V to
match the command signal, but can be any value in the range 0-5V.
5. Press and hold the CALIBRATE button until the CALIBRATE LED goes out. Release the button and the
CALIBRATE LED will flash twice briefly every second.
6. Use the INCREASE and DECREASE buttons to set the actuator to the required position for the maximum, 20mA
command signal. As before, this can be any position within the mechanical range of the actuator.
7. Set the command signal to 20mA.
8. Adjust the CAL1 potentiometer to give the required output for the chosen position. Note that this not need be 5V to
match the command signal, but can be any value in the range 0-5V.
9. Press and hold the CALIBRATE button until the CALIBRATE LED goes out. Release the button to complete the
calibration sequence and the Manual LED will extinguish.
General operation
When calibration has been completed the IS200 reverts to automatic mode and to stepping operation if DIL switch 4 is set
ON. The actuator should now follow the command signal input and move to the desired position.
If there is any instability in positioning, particularly if the hydraulic flow rate is high, then the DEADZONE potentiometer can
be set progressively clockwise, half a turn at a time, until stable positioning following a step change can be achieved.
If the command signal or the feedback signal becomes faulty then the selected fail mode will operate. The actuator will
either freeze position, drive down or drive up and the control to the ESD solenoid will be removed. The system will recover
to normal operation when the signals are re-instated. If an ESD solenoid is not required then the ESD output can be used as
a system fault output to the remote DCS if driven through a suitable barrier. If the unit is in "stepping mode" (DIL switch 4 =
ON) then failure mode drive can be either in the selected stepping mode or, if DIL switch 1 is ON, then the unit will fast-fail to
its default position.
All calibration parameters are stored within the processor EEPROM and are restored each time the controller is powered up.
The controller will respond to current command and feedback signal conditions within 100mS of power being applied to the
system
Maintenance
The outside of the enclosure can be cleaned using a damp cloth. Do not use solvents. Do not open the enclosure whilst a
hazard is present.
No internal parts are user serviceable and component level repairs should not be attempted. If a fault occurs then please
return the unit to the Manufacturers describing the nature and circumstances of the problem.