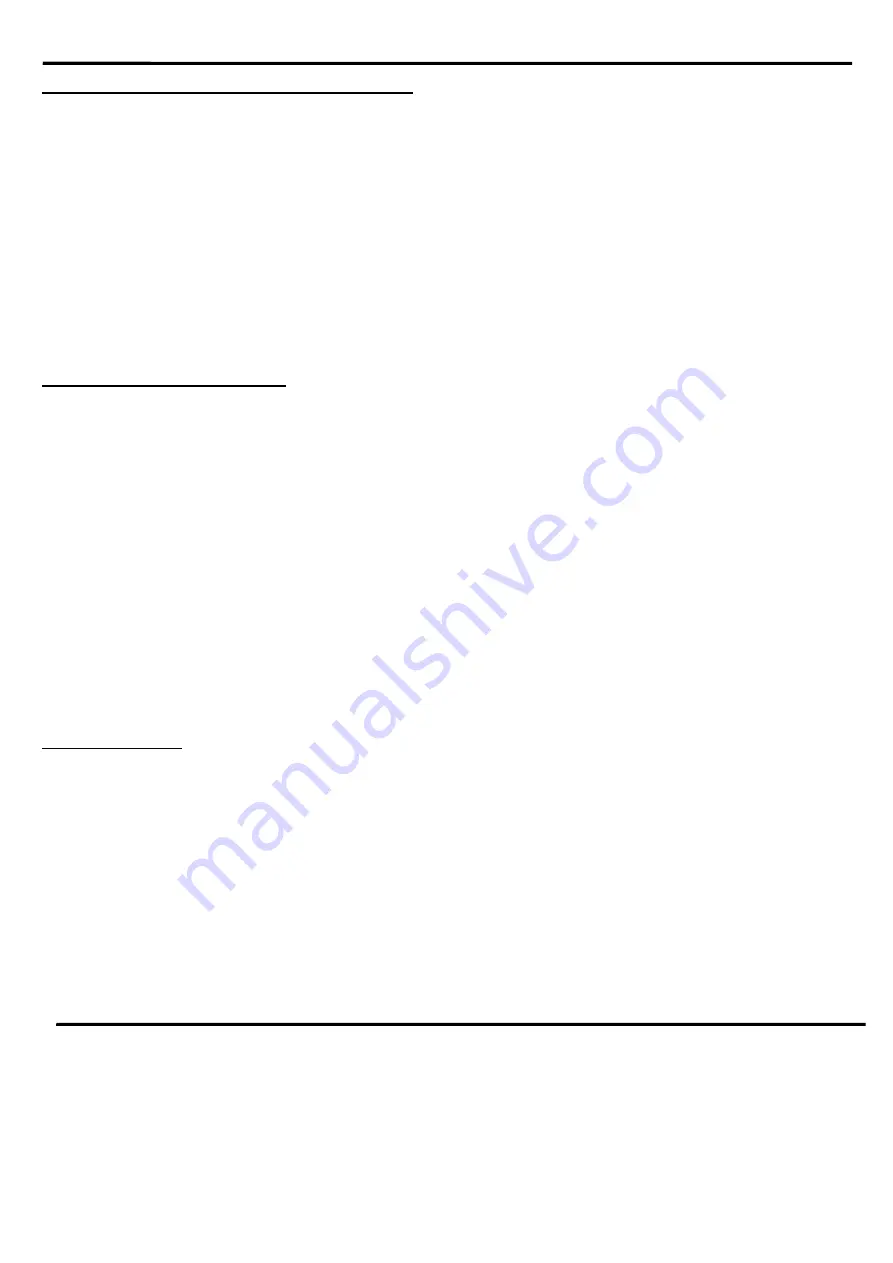
IS200 Electro-Hydraulic Actuator Positioner
Orange Instruments Limited.
Drwg. No.: 1357-007 Issue : K Date : 07/10/2013 Page :
4 of 9
Iss c - Certificate number added. Iss D - Ta changed to -20 to +60
Iss E - Details of fail modes, timers and retrans. O/P added. Retrans. Signal barrier changed to KFD0-CC-Ex1
Iss F
– Details of change in Max/min on & off times + addition of 10R in line with pos o/p –ve
Iss G
– Stepping times range change to allow finer adjustment 15/11/2007
Iss H
– CE Cert. of Conformity details added, Ta to –40degC, 60079:0,26 mods 25/06/2008
Iss J
– Harmonised standards in C of C modified to meet current status 04/08/2008
Iss K - Markings changed to meet EN 60079-0:2012 02/10/2103
ATEX Certified Equipment - Change Authority ATEX Manager ONLY
Setting the command signal break default operation
The positioner can be configured to move to a default position or freeze at the current position in the event of the command
or feedback signal faults. These faults are characterised as:
a) the command falling below 1mA - command signal break
b) the potentiometer wiper showing less than 0.25V - potentiometer maximum or wiper break
c) the potentiometer wiper showing more than 4.7V - potentiometer minimum break.
A one-off operation of the positioner will store the choice in non-volatile EEPROM memory.
1. Hold in the MANUAL pushbutton and apply power to the positioner.
2. The MANUAL LED will light continuously and pressing the manual DECREASE and INCREASE pushbuttons will
cause the appropriate DECREASE and INCREASE LEDS to “toggle” on and off.
3. Select the DECREASE LED on for drive downscale on fault,
4. Select the INCREASE LED on for drive upscale on fault.
5. Leave both LEDs off to select freeze at the current position on fault.
6. When satisfied press the MANUAL pushbutton again.
7. Remove power from the positioner.
Setting the stepping option timers
If stepping operation is required, the ON and OFF timers for the open and close solenoids have to be set. This operation is
best performed when the actuator hydraulics are isolated but the settings can be trimmed during normal operation of the
system. Minimum ON / OFF times 20mS. Maximum ON / OFF times 11 seconds.
1. Set DIP switch 3 to ON. This selects timer setting mode. Manual mode is selected automatically.
2. Set DIP switch 1 to ON.
Do not select DIP switches 1 and 2 ON together.
The DECREASE LED will flash and the
decrease solenoid will operate. Adjust CAL1 potentiometer to vary the ON time and CAL2 potentiometer to vary the
off time. Time the on/off transition over a few cycles to obtain the required result.
3. Press the CALIBRATE button to store the decrease step timer values.
4. Set DIP switch 1 to OFF.
5. Set DIP switch 2 to ON.
Do not select DIP switches 1 and 2 ON together.
The INCREASE LED will flash and the
increase solenoid will operate. Adjust CAL1 potentiometer to vary the ON time and CAL2 potentiometer to vary the
off time. Time the on/off transition over a few cycles to obtain the required result.
6. Press the CALIBRATE button to store the increase step timer values.
7. Set DIP switch 1 to OFF.
8. Set DIP switch 3 to OFF.
9. The stepping option can be selected by setting DIL switch 4 ON.
10. The above sequence, or part of it, can be selected at any time during normal operation but the actuator will move
during the adjustment so hydraulic isolation is advised.
First time operation
WARNING !!
The actuator and associated mechanical equipment connected to it could possibly move in an unpredictable
manner during initial calibration. Ensure that all personnel take appropriate precautions.
1. Ensure that any end of travel limit switches and mechanical stops are correctly adjusted before operation.
2. Apply power and provide the 4-20mA command signal. Press the Auto/Manual Switch. Check that the Auto/Manual LED
is lit.
3. Operate the Open and Close buttons and confirm that the actuator moves as required.
4. The system must be calibrated before automatic mode is selected.