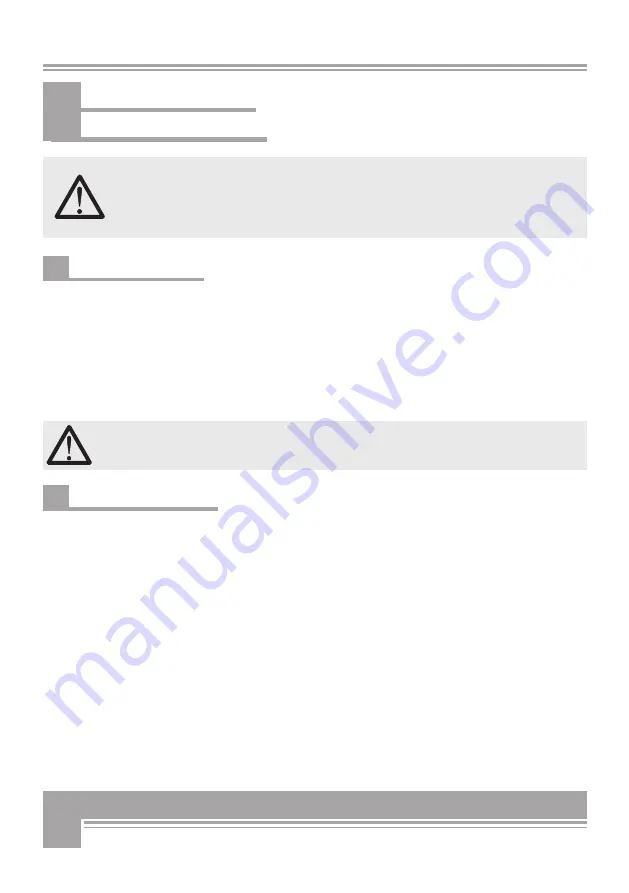
20
9. REPAIRS AND
MAINTENANCE
Make sure that the machine is fully disconnected and all
moving parts are secured before performing any main-
tenance/repair work on the machine. In the event of
any malfunctioning, switch the machine off before trou-
ble-shooting.
9.1 Ordinary maintenance
Make maintenance a regular part of daily operation. The daily mainte-
nance routine needs to include:
• Cleaning of the machine and clearing of all parts from residual wood
debris, chips, dust, bark pieces and eventual other waste.
• Greasing of the sliding pads inside the splitter stand.
• Hydraulic oil check and (in case of leakage) hydraulic hose and fit-
tings check-up to detect eventual oil leaks.
• Lubrication of all moving parts.
Oil or grease the wedge slinding pads after every 10 operation
hours.
9.2 Recommended oil types:
Periodically check the oil level inside the hydraulic oil tank. When doing
so, accurately avoid contaminating the tank with dirt, wood chips, sow
dust etc...Make sure that the splitter never runs without oil or with a low
oil level. When this happens, air is likely to reach inside the hydraulic
loop. Failure to maintain due oil level may cause poor running and irre-
gular splitter operation (very rough, back/forth or up/down motions) as
well as major pump damages. Please schedule your first oil change after
approximately 25-30 operation hours and later ones at least once a year.
Make sure to accurately clean the suction filter at each oil change.
Recommended oil types:
DEA HD B 46, Shell Tellus 10-46, Esso Nuto H 46.
After each new oil fill, operate the splitter and let it run for 2 or 3 complete
cycles before plugging the tank. This operation will help bleeding all residual
air out of the hysdraulic line. No parts or components of this rugged splitter
construction are likely to get damaged during compliant use and handling.
However always check all hydraulic hoses, fittings and couplings to detect
and repair eventual oil leaks. Do not check for leaks with your hand.