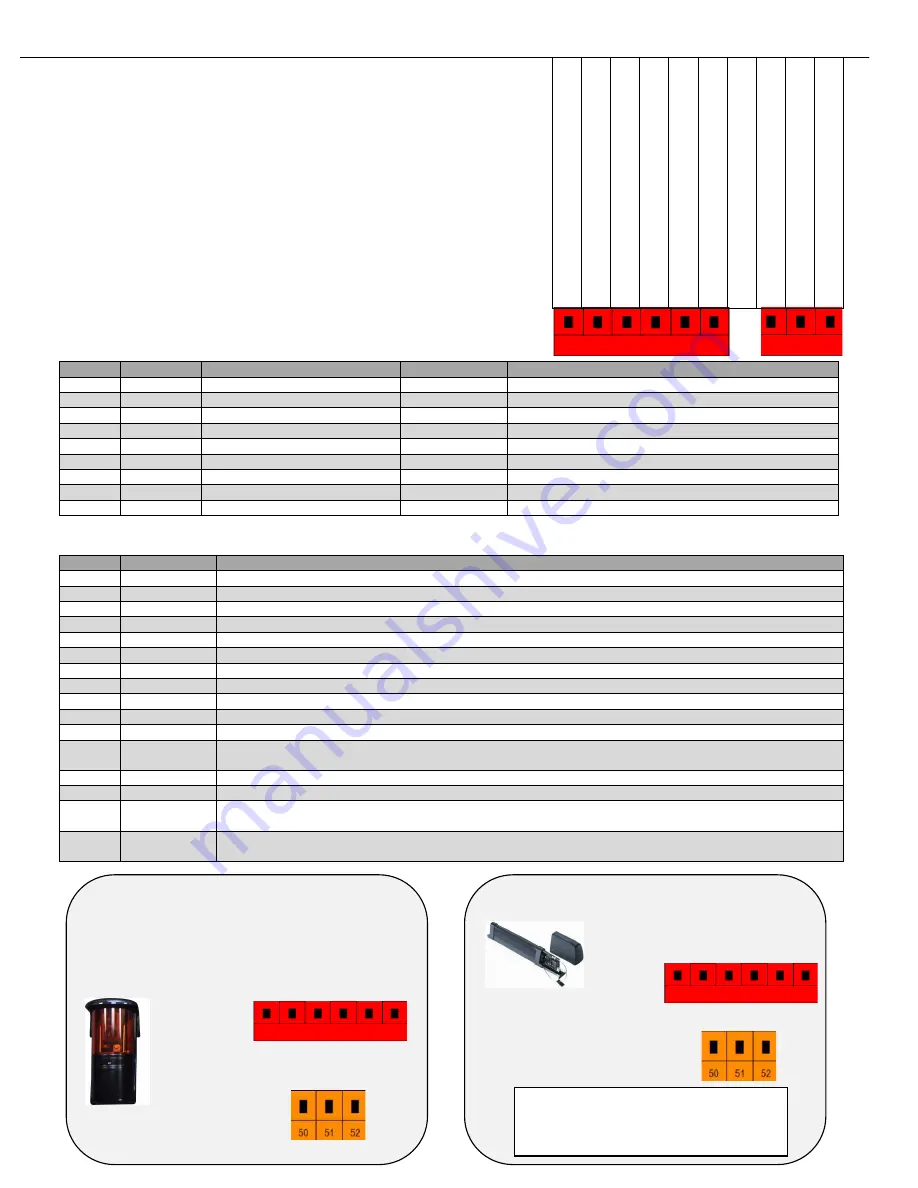
SAFETY DEVICES
The Thalia board provides:
- one
STOP
command input;
- one obstruction sensing device input
UL
3
25-2016
compatible,
SAFE 1
with its
mandatory supervision circuit input
FAULT 1
. The system reacts to the input in both
opening (stops) and closing (reverses) cycles;
- two programmable obstruction sensing device inputs,
SAFE 2
and
SAFE 3
, both
provided with their optional supervision circuit input
FAULT 2
and
FAULT 3
.
All the
3
safety inputs are
N.C. (normally closed)
contacts. All the FAULT inputs are
N.O. (normally open)
contacts. Below is a table with the terminal numbers and their
corresponding functions and default values.
Terminal
Name
Description
Default
Notes
70
COM
Safety positive common
Common
71
STOP
Stop command
STOP
Overrides all other commands
72
SAFE 1
Safety input #1
PHOT
Stops operators during opening, reverses on closing
73
FAULT 1
Supervisory circuit for SAFE 1
FAULT
Requires opposite relay state from SAFE 1
74
SAFE 2
Safety input #2
006 - BAR
Programmable input (see LOGIC sub-menu)
75
FAULT 2
Supervisory circuit for SAFE 2
FAULT
Requires opposite relay state from SAFE 2
76
COM
Safety positive common
Common
77
SAFE 3
Safety input #3
015 - SHADOW
Programmable input (see LOGIC sub-menu)
78
FAULT 3
Supervisory circuit for SAFE 3
FAULT
Requires opposite relay state from SAFE 3
VALUE
FUNCTION
DESCRIPTION
000
PHOT
System reacts to the input in both opening (stops) and closing (reverses) cycles
001
PHOT TEST
Same as above. Requires the device to be supervised (FAULT active)
002
PHOT OP
System reacts to the input only during the opening cycle (stops)
003
PHOT OP TEST
Same as above. Requires the device to be supervised (FAULT active)
004
PHOT CL
System reacts to the input only during the closing cycle (reverses)
005
PHOT CL TEST
Same as above. Requires the device to be supervised (FAULT active)
006
BAR
Safety edge input. It reacts in both opening and closing. It stops and partially reverses
007
BAR TEST
Same as above. Requires the device to be supervised (FAULT active).
008
BAR 8K2
Safety edge input with EOL resistor as supervision method.
Active only on SAFE 2
009
BAR OP
Safety edge input. During opening it stops and partially reverses. During closing it stops.
010
BAR OP TEST
Same as above. Requires the device to be supervised (FAULT active)
011
BAR OP 8K2
Safety edge input with EOL resistor as supervision method. During opening it stops and partially reverses.
During closing it stops.
Active only on SAFE 2
012
BAR CL
Safety edge input. During closing it stops and partially reverses. During opening it stops.
013
BAR CL TEST
Same as above. Requires the device to be supervised (FAULT active)
014
BAR CL 8K2
Safety edge input with EOL resistor as supervision method. During closing it stops and partially reverses.
During closing it stops.
Active only on SAFE 2
015
SHADOW
Safety loop input. If the contact is closed, it prevents any movement of the leafs when gate is open (VALUE 0 of the
LOGIC
SHADOW
) or when the gate is both open and closed (VALUE 1 of the
LOGIC
SHADOW
). See chart example N. 3 on next page.
Both
SAFE 2
and
SAFE 3
can be programmed to perform any of the following functions under the
LOGIC
sub-menu:
EXAMPLE 1
: UL
3
25-201
6
SAFETY PHOTO BEAM SENSOR WIRING
RELAY N.
O
.
RELAY N.C.
COMMON
POWER 24V +
POWER 24V -
EXAMPLE 2
: SAFETY EDGE WIRING
RELAY N.C.
COMMON
PROGRAMMING
:
LOGIC > SAFE 2 > 006 (BAR)
7
0
-
C
o
m
m
o
n
7
1
-
S
T
O
P
72
–
SAFE
1:
PHOT
UL
3
25-16
(obstruction)
73
–
FAULT
1
UL
3
25
-
2016
7
4
–
S
A
F
E
2
–
p
ro
g
ra
m
m
a
b
le
-
d
e
fa
u
lt
i
s
BA
R
(s
a
fe
ty
e
d
g
e
)
7
5
–
F
A
U
L
T
2
7
6
-
C
o
m
m
o
n
7
7
–
S
A
F
E
3
–
p
ro
g
ra
m
m
a
b
le
–
d
e
fa
u
lt
i
s
S
H
A
D
O
W
(
sa
fe
ty
l
o
o
p
)
7
8
–
F
A
U
L
T
3
76 77 78
20
70
71
72
73
74
75
70
71
72
73
74
75
70
71
72
73
74
75