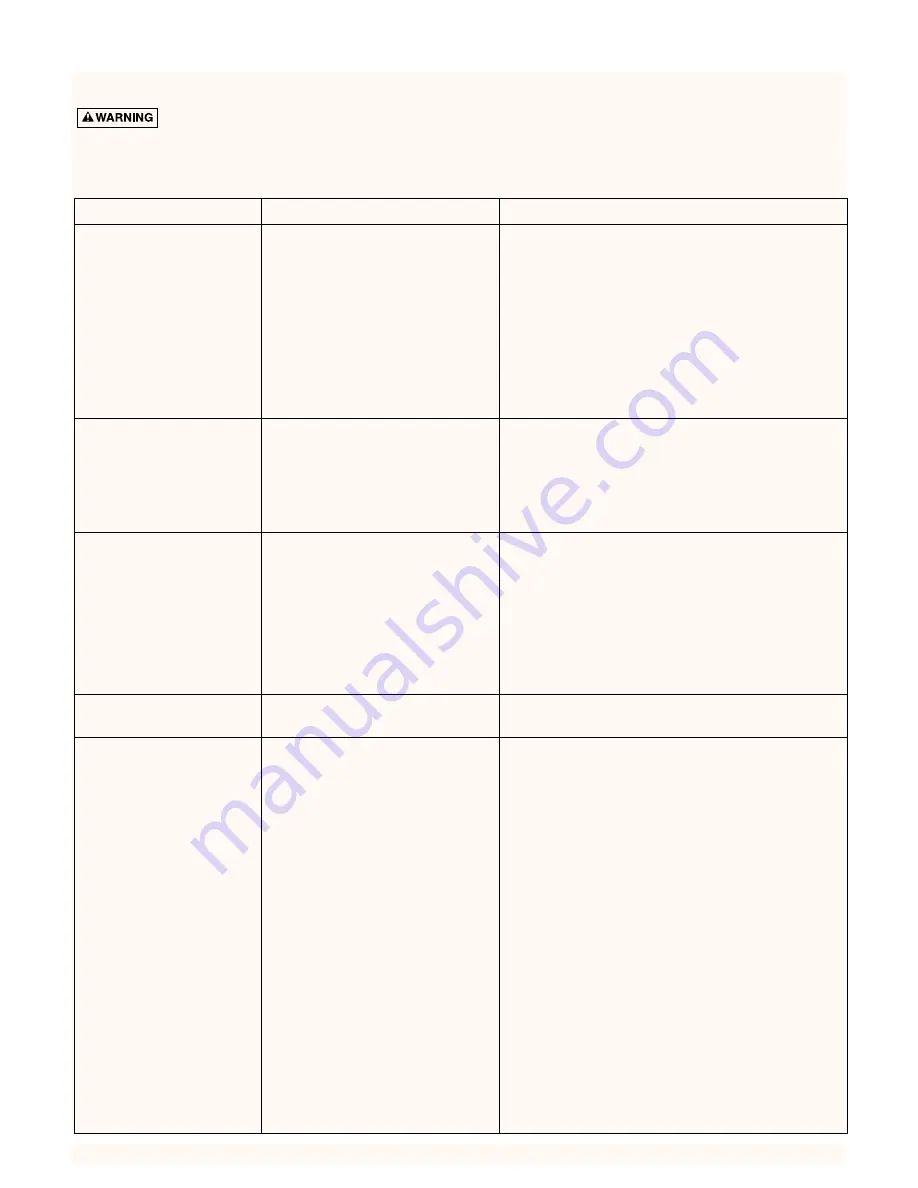
12
TROUBLESHOOTING
PROBLEM
POSSIBLE CAUSE
REMEDY
Fuses blow or overload
1. Pump sandlocked.
1. a) Check motor winding resistance - see "Circuit
circuit breaker trips when
(Winding) Resistance", Page 6.
motor starts.
b) If motor is not shorted, turn on current and rap
discharge pipe sharply to loosen sand.
c) Pull pump and clean.
2. Low or high voltage.
2. Check line voltage (see Page 4). If high or low,
contact power company.
3. Cable damaged or shorted.
3. Check pump cable for ground (see Page 6).
4. Pump forced into crooked well.
4. Forcing pump into a crooked hole will cause mis-
alignment of pump and motor. Consult well driller.
Fuses blow or overload
1. Low or high voltage.
1. Check voltage on service lines (see Page 4).
trips while motor is running.
2. Water contains abrasives.
2. If water contains excessive sand, remove pump
and clean sand out of well.
3. Motor or cable shorted and/or
3. See "Circuit (Winding) Resistance Test" and
grounded.
"Ground Check", Page 6.
Motor does not start but
1. Fuses blown or circuit breaker
1. Reset circuit breakers or replace fuses.
does not blow fuses or
tripped.
trip circuit breaker.
2. Voltage does not reach terminals.
2. 3-Phase: Check voltage at controller between wire
pairs: L1 – L3, L3 – L2, L2 – L1.
Single Phase: Check voltage between L1 and L2 on
box terminal strip.
3. Loose wire in control box.
3. Check and tighten all wires.
4. Defective magnetic controller coil.
4. Check starter and coil.
Pump does not shut off.
1. Cable leads improperly connected.
1. Check wiring diagram on box cover for correct
connections.
Motor runs, but delivers
1. Horizontal line check valve
1. Reinstall correctly.
little or no water.
installed backwards.
2. Motor running backwards
2. Reconnect motor for proper rotation (see Page 3).
(3-Phase only).
3. Pump gaslocked.
3. Start and stop pump several times allowing one
minute between stops and starts.
4. Water level in well has dropped.
4. a) Restrict pump flow to equal well production.
b) Install liquid level control.
c) Reset pump lower in well.
5. Leak in discharge pipe.
5. Raise pipe until leak is found.
6. Coupling between motor shaft
6. remove pump from well and check coupling.
and pump shaft broken.
7. Pump parts worn from abrasives.
7. a) Check pump shut-off pressure. Pressure should
be at least 90% of pressure at installation.
b) Replace worn parts.
8. Intake screen clogged.
8. Remove pump from well and clean screen.
9. Pump set below recommended
9. a) Reduce pressure switch setting until pump will
depth.
shut off.
b) Install pump producing higher pressure.
10. Discharge pipe friction reduces
10. Install larger pipe or pump producing higher pressure.
output.
Hazardous voltage. Can shock, burn, or
kill. When troubleshooting or servicing pump, use all
normal precautions for the voltages involved.
1.
Disconnect power unless required for testing.
2.
Have electrical testing done by a qualified
electrician.
3.
Most problems occur above ground. Remove pump
from well only as a last resort.