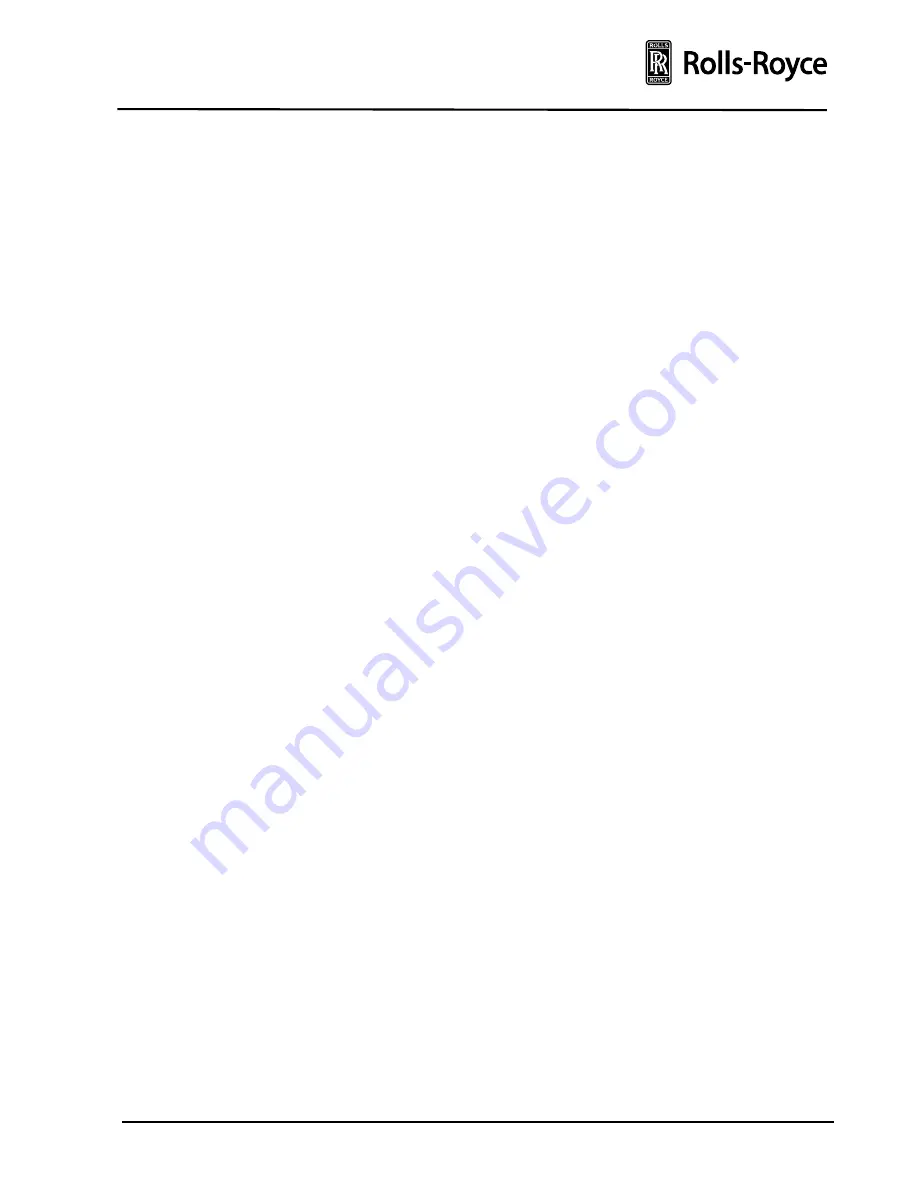
, Gas
Lubricating oil system
Page 1 : 9
2.08
0915 BC
L
UBRICATING
OIL
SYSTEM
Introduction
The engine has one main lubricating oil system
design, with a separate branch to the turbocharger
and reduced oil pressure to the valve gear.
Components attached to the engine are shown on
the enclosed system drawing B1104/47(L),
B1104/69 (V12) and B1168/94 (V20).
Lubricating Oil Tanks
The engine has as standard a wet sump arrange-
ment. The wet sump oil volume at maximum level
is approx. 0.5 - 0.64 litre/kW for propulsion engines.
Engines designed for dry sump are available on
request.
Pumps and Capacities
The engine has an engine driven gear type main
lubricating oil pump with a built-in pressure
relief valve set to 3.8 - 4.0 bar pressure.
For the rocker arms the lubricating oil pressure is
reduced to approx. 0.5 bar.
Lubricating oil volume in crankcase:
High level: ............................approx. 0,8 litre/kW MCR
Low level:..............................approx. 0,6 litre/kW MCR
Priming pump
This engine type is as standard equipped with an
electrically driven priming pump 31LO, normally
mounted off engine. In case of a single propulsion
engine installation hence required combined
priming / stand by (full flow) el. driven lubricating oil
pump, the pump must be mounted off engine.
Capacity and electrical data are available upon
request. See Technical Data, part 1.04 for other pump
capacities.
Pipe Materials/Velocities and
Pressure Losses
Steel pipes are normally used in the lubricating oil
system. In order to prevent excessive pressure losses
in the piping system, we recommend that the
lubricating oil velocity should not exceed:
•
1,0 m/s in a suction pipe.
•
1,5 - 2,0 m/s in a pressure pipe.
Crankcase Venting
In internal combustion engines the combustion
pressure causes a certain amount of blow-by past
piston rings into the crankcase. Seal air from the
turbocharger is also led into the crankcase.
To prevent pressure build up in the crankcase, a vent.
tube is provided to allow the gas and seal air to
escape. As the gas consists of combustion gases and
oil fumes, the vent. pipe has to be led to a safe out-
door position. This is to prevent clogging of air filters,
health hazard etc.
To clean the oil mist, a crankcase ventilation filter,
designed to build up underpressure is used. The two
stage filter unit separates oil from the mist and the
oil is led back to the engine oil sump. The cleaned
gas is led to a safe outdoor position.
If ambient temperature on electrical control box
exceeds 40°C, the control box must be disconnected
from the filter unit and moved to a suitable place
with ambient temperature of max. 40°C.
A separate crankcase venting system is required for
each engine. This is also to prevent fumes and mois-
ture produced by a running engine from entering an
engine in stand-by.
The vent pipe system (diameter and length) to be
designed according to the following, applicable for
engines for fuel gas operation:
Max. allowable back pressure: .................15 mm WG
Gas flow (design flow): .......................................... 0.5 %
of combustion air consumption.
See Technical Data in part 1.04.
The back pressure may be calculated according to
the following formula:
where
L = Total pipe length, straight pipe (m)
S = Density of gas (1,0 kg/m
3
)
Q = Gas flow (m
3
/s)
D = Inside diameter of pipe (m)
The vent pipe should have a continuous upward
gradient of minimum 15 degrees. Steel pipes are to
be used in the vent system.
dp
1 70
10
3
–
L
S
Q
2
D
5
--------------------------
mmWG
=
Summary of Contents for B35:40
Page 1: ...Ma r i n e P r o j e c t G u i d e B e r g e ne n g i n et y p eB 3 5 4 0G a s...
Page 2: ...BLANK...
Page 4: ...BLANK...
Page 6: ...BLANK...
Page 9: ...Gas Technical data Page 1 8 1 02 0611 B TECHNICAL DATA...
Page 17: ...Gas Main dimensions Page 1 8 1 03 0611 B MAIN DIMENSIONS...
Page 18: ...Main dimensions Page 2 8 1 03 Gas 0611 B...
Page 19: ...1 03 Gas Main dimensions Page 3 8 0611 B...
Page 20: ...Main dimensions Page 4 8 1 03 Gas 0611 B...
Page 21: ...1 03 Gas Main dimensions Page 5 8 0611 B...
Page 22: ...Main dimensions Page 6 8 1 03 Gas 0611 B...
Page 23: ...1 03 Gas Main dimensions Page 7 8 0611 B...
Page 24: ...Main dimensions Page 8 8 1 03 Gas 0611 B...
Page 26: ...Gas Load limit Page 1 1 1 07 0314 B G LOAD LIMIT Load limit curve B35 40 PG...
Page 31: ...Starting and control air system Page 4 5 2 01 Gas 0615 BC...
Page 32: ...2 01 Gas Starting and control air system Page 5 5 0615 BC...
Page 37: ...Exhaust gas system Page 4 5 2 03 Gas 0317 BC...
Page 38: ...2 03 Gas Exhaust gas system Page 5 5 0317 BC...
Page 44: ...Fuel gas supply system Page 4 4 2 05 Gas 0717 BC...
Page 48: ...Page 4 6 2 06 Gas 1011 BC...
Page 49: ...2 06 Gas Page 5 6 1011 BC...
Page 50: ...Page 6 6 2 06 Gas 1011 BC...
Page 56: ...Lubricating oil system Page 4 9 2 08 Gas 0915 BC...
Page 57: ...2 08 Gas Lubricating oil system Page 5 9 0915 BC...
Page 58: ...Lubricating oil system Page 6 9 2 08 Gas 0915 BC...
Page 59: ...2 08 Gas Lubricating oil system Page 7 9 0915 BC...
Page 60: ...Lubricating oil system Page 8 9 2 08 Gas 0915 BC...
Page 61: ...2 08 Gas Lubricating oil system Page 9 9 0915 BC...
Page 70: ...3 02 Gas Safety Control and Monitoring System Page 7 9 0211 BC...