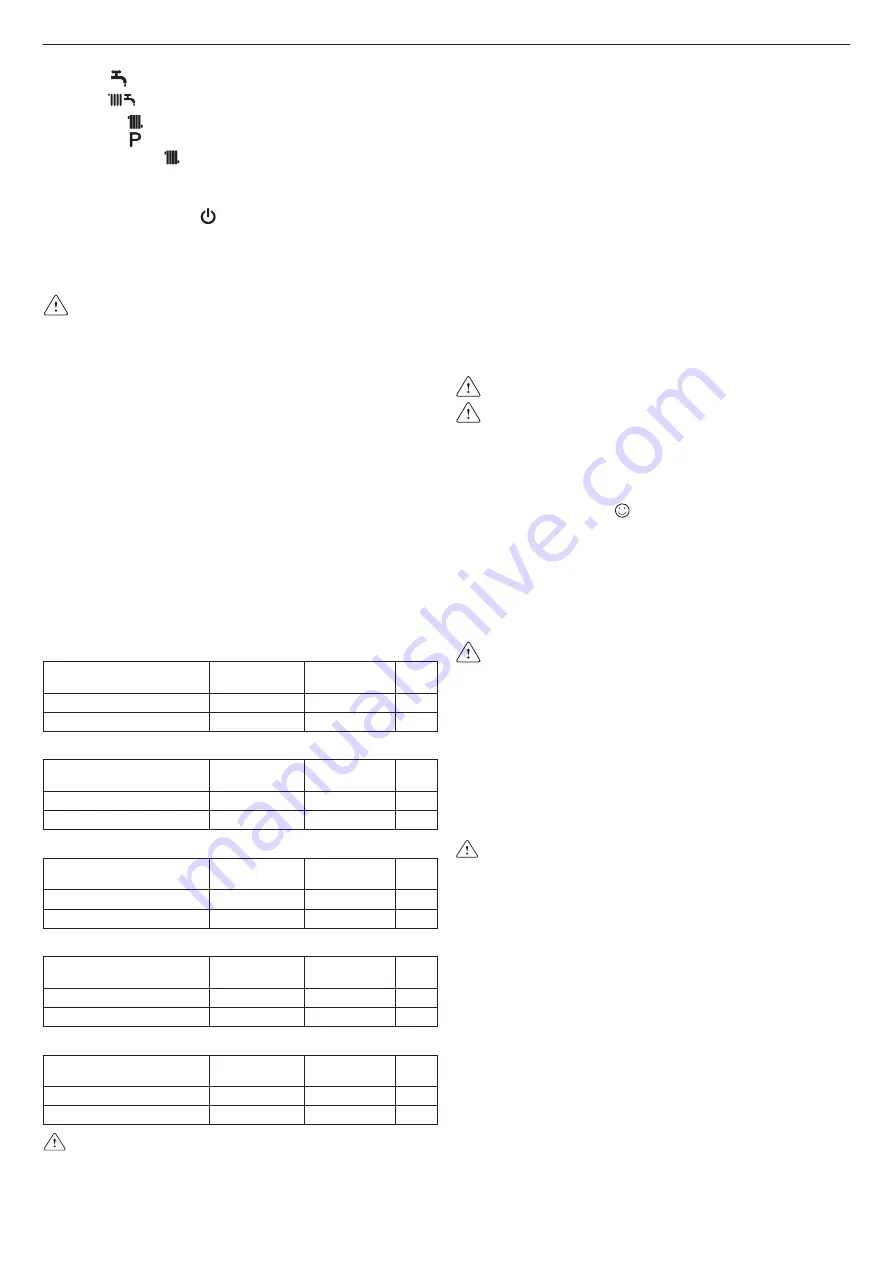
QUADRA GREEN C.S.I.
28
1. Maximum
2. Minimum
3. Max. heating
4. Slow ignition
5. Max. preset heating
GAS VALVE CALIBRATION
- Connect the boiler to the power supply
- Open the gas tap
- Set the function selector to
(OFF/RESET) (monitor off )
- Loosen the screws (
E
), remove the housing, then lower the instrument
panel towards you (fi g. 14)
- Loosen the fi xing screws on the cover (
F
) to access the terminal board
(fi g. 16)
- Using a small screwdriver included, press the CO button (fi g. 26)
Live electrical parts.
- Wait for burner ignition.
The display shows “ACO” and the yellow LED fl ashes. The boiler oper-
ates at maximum heat output.
The “combustion analysis” function remains active for a limited time (15
min); if a delivery temperature of 90°C is reached, the burner is switched
off . It will be switched back on when this temperature drops below 78°C.
- Insert the analyser probe in the ports provided in the air distribution box,
after removing the screws from the cover (fi g. 41)
- Press the “combustion analysis” button a second time to reach the num-
ber of rotations corresponding to the maximum domestic hot water output
(
table 1
); the yellow LED continues to fl ash while the red LED is fi xed
- Check the CO
2
value: (
table 3
) if the value does not match the value
given in the table, use the gas valve maximum adjustment screw
- Press the “combustion analysis” button a third time to reach the number
of rotations corresponding to the minimum output (
table 2
); the yellow
LED continues to fl ash while the green LED is fi xed
- Check the CO
2
value: (
table 4
) if the value does not match the value
given in the table, use the gas valve minimum adjustment screw
- To exit the “combustion analysis” function, turn the control knob
- Remove the fl ue gas probe and refi t the plug
- Close the instrument panel and refi t the housing.
The “combustion analysis” function is automatically deactivated if the board
triggers an alarm. In the event of a fault during the combustion analysis
cycle, carry out the reset procedure.
table 1
MAXIMUM NUMBER OF
FAN ROTATIONS
METHANE
GAS (G20)
LIQUID GAS
(G31)
25 C.S.I.
heating - DHW
49 - 61
49 - 61
rpm
30 C.S.I.
heating - DHW
53 - 62
52 - 60
rpm
table 2
MINIMUM NUMBER OF
FAN ROTATIONS
METHANE
GAS (G20)
LIQUID GAS
(G31)
25 C.S.I.
14
14
rpm
30 C.S.I.
14
14
rpm
table 3
Max. CO
2
METHANE
GAS (G20)
LIQUID GAS
(G31)
25 C.S.I.
9,0
10,5
%
30 C.S.I.
9,0
10,5
%
table 4
Min. CO
2
METHANE
GAS (G20)
LIQUID GAS
(G31)
25 C.S.I.
9,5
10,5
%
30 C.S.I.
9,5
10,5
%
table 5
SLOW IGNITION
METHANE
GAS (G20)
LIQUID GAS
(G31)
25 C.S.I.
40
40
rpm
30 C.S.I.
40
40
rpm
If the CO
2
values do not correspond to the values in the Multigas
table, make further adjustments.
4.8 Gas conversion (fi g. 42-43)
Gas conversion from one family of gases to another can also be easily
performed when the boiler is installed. This operation must be carried out
by professionally qualifi ed personnel. The boiler is designed to operate with
methane gas (G20) according to the product label.
It is possible to convert the boiler to propane gas, using the special kit.
For disassembly, refer to the instructions below:
- switch off the power supply to the boiler and close the gas tap
- remove in sequence: housing and air distribution box cover
- remove the fi xing screw from the instrument panel
- unhook and turn the instrument panel forwards
- remove the gas valve (
A
)
- remove the nozzle (
B
) inside the gas valve and replace it with the nozzle
from the kit
- refi t the gas valve
- remove the silencer from the mixer
- open the two half-shells by prising apart the corresponding hooks (
C
)
- replace the air diaphragm (
D
) in the silencer
- refi t the air distribution box cover
- re-power the boiler and turn on the gas tap
Adjust the boiler as described in the chapter entitled “Adjustments” with
reference to the information on LPG.
Conversion must be carried out by qualifi ed personnel.
Once the conversion is complete, affi
x the new identifi cation
label supplied in the kit.
4.9 Checking the combustion parameters
To carry out the combustion analysis, proceed as follows:
- set the main switch of the installation to the “OFF” position
Method 1
- frontal procedure
- turn the selector to position
- chimney sweep function
Method 2
- board procedure
- loosen the fi xing screws (
D
) on the housing (fi g. 13)
- move the base of the housing forwards and then upwards to unhook it
from the chassis
- loosen the fi xing screws (
E
) on the instrument panel (fi g. 14)
- lift then turn the instrument panel towards you
- loosen the fi xing screws on the cover (
F
) to access the terminal board
(fi g. 16)
- using a small screwdriver included, press the CO button (fi g. 26)
Live electrical parts.
For both methods
- Wait for burner ignition. The display shows “ACO”, the yellow LED fl ashes
and the boiler operates at maximum heat output.
- Insert the analyser probe in the ports provided in the air distribution box,
after removing the screws from the cover (fi g. 41).
- Check that the CO
2
values match those given in the table, if the value
shown is diff erent, change it as indicated in the chapter entitled “Gas
valve calibration”.
- Perform the combustion check.
Then:
- remove the analyser probe and close the sockets for combustion analysis
with the special screw
- close the instrument panel and refi t the housing.
The fl ue gas analysis probe must be fully inserted as far as
possible.
IMPORTANT
Even during the combustion analysis phase, the function that switches the
boiler off when the water temperature reaches the maximum limit (about
90°C) remains enabled.
5 MAINTENANCE
The appliance must be systematically controlled at regular intervals to
make sure it works correctly and effi ciently and conforms to legislative
provisions in force.
The frequency of controls depends on the conditions of installation and
usage, it being anyhow necessary to have a complete check carried out by
authorized personnel from the Servicing Centre every year.
- Check and compare the boiler’s performance with the relative
specifi cations. Any cause of visible deterioration must be immediately
identifi ed and eliminated.
- Closely inspect the boiler for signs of damages or deterioration, particularly
with the drainage and aspiration system and electrical apparatus.
- Check and adjust – where necessary – all the burner’s parameters.
- Check and adjust – where necessary – the system’s pressure.
- Analyze combustion. Compare results with the product’s specifi cation.
Any loss in performance must be identifi ed and corrected by fi nding and
eliminating the cause.
- Make sure the main heat exchanger is clean and free of any residuals or
obstruction; if necessary clean it.
- Check and clean – where necessary – the condensation tray to make
sure it works properly.
Summary of Contents for 20095438
Page 95: ...QUADRA GREEN C S I 95 g 45...