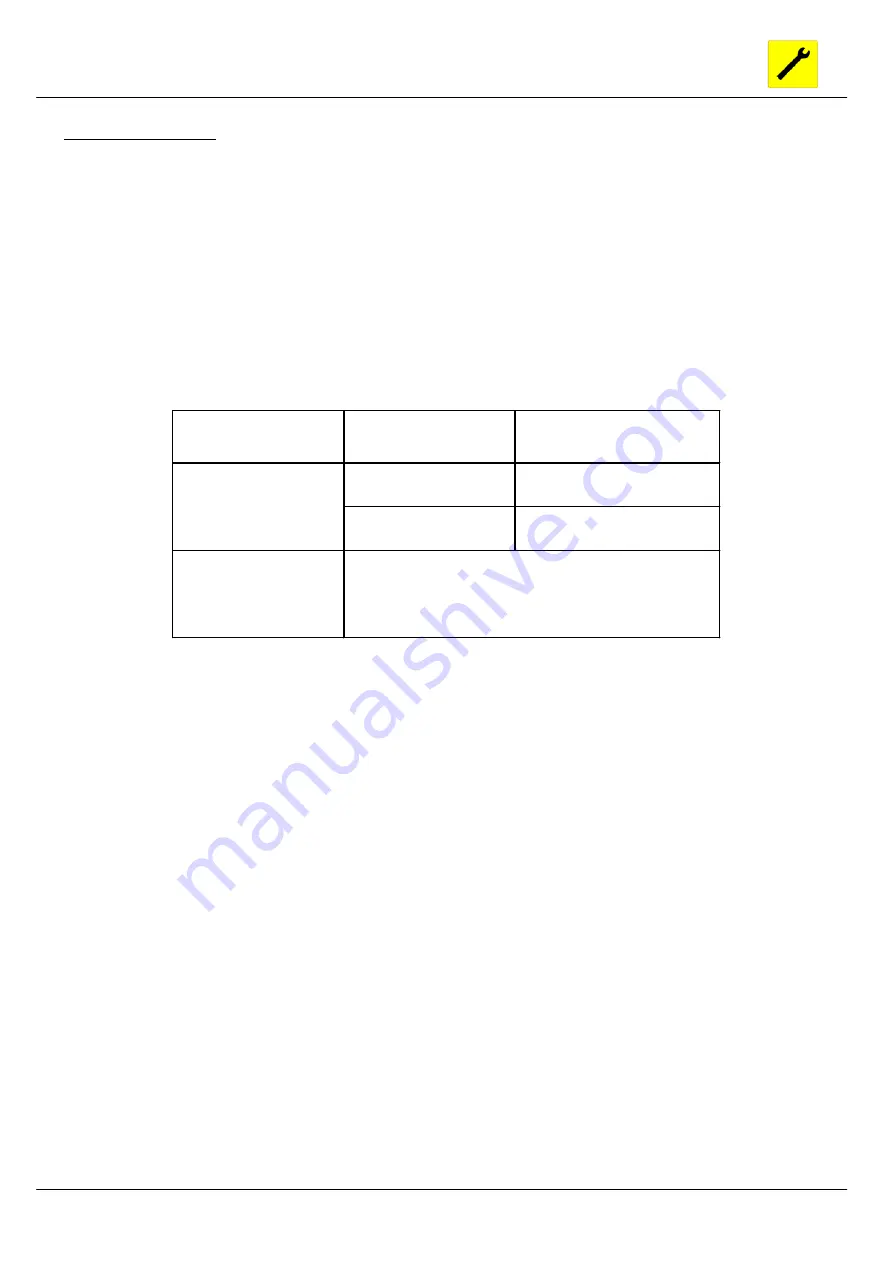
Appendix 1
Page 14 Issue 2
Errors of Eccentricity
The procedure for measuring eccentricity is precisely analogous to that used for angularity.
In this case, however, the measurements are taken in a radical direction and the most
convenient and accurate means of doing this utilises a dial indicator suitably clamped to one
half coupling, and bearing on the hub or flange of the other, as shown in figures 4 and 5 on
page 13.
Care must, however, be taken to ensure the support for the dial indicator is sufficiently rigid
to prevent the weight of the indicator from causing deflection and, in consequence,
inaccurate readings. Extra care should be taken where taper roller bearings are fitted to
ensure that alignment is checked with shafts in mid-point position and a final check made
with the unit at operating temperature.
Rigid
All Other types
Please see appropiate installation and maintenance
manual for coupling type fitted
Type of Coupling
Unit Size
Allowable Eccentricity
(mm)
SIZE 08 & UNDER
0.025
SIZE 09 & OVER
0.035
SPECIAL NOTE CONCERNING RIGID COUPLINGS
In lining up elements involving rigid couplings it is important that no attempt is made to
correct errors of alignment or eccentricity greater than those above by tightening of the
coupling bolts (This applies when the system is cold or at operating temperature). The result
is miss-alignment and the setting up of undue stresses in the shaft, coupling and bearings.
This will be revealed by the springing apart of the coupling faces if the bolts are slackened
off. A check on the angularity of a pre-assembled job, after bolting down, can be obtained in
the case of rigid couplings by slackening off the coupling bolts, when any mis-alignment will
cause the coupling faces to spring apart. This check may not, however, reveal any strains
due to eccentricity owing to the constant restraint imposed by the spigot.
SERIES X COUPLINGS
We produce standard flexible couplings to cover the complete range of gear units, please
contact Application Engineering for details.
Summary of Contents for C Series
Page 15: ...Appendix 1 Page 13 Issue 2 ...
Page 20: ...Appendix 2A Page 18 Issue 2 Series C K F Shaft Mount Units Alternative Shaft Fixing Methods ...
Page 24: ...Appendix 2C Page 22 Issue 2 Shrink Disc Installation Maintenance ...
Page 25: ...Appendix 2D Page 23 Issue 2 Series C Torque Bracket Dimensions ...
Page 27: ...Appendix 2D Page 25 Issue 2 Series K Torque Bracket Dimensions ...
Page 33: ...Appendix 4 Page 31 Issue 2 ...
Page 35: ...Appendix 4 Page 33 Issue 2 ...
Page 37: ...Appendix 4 Page 35 Issue 2 ...
Page 39: ...Appendix 4 Page 37 Issue 2 ...