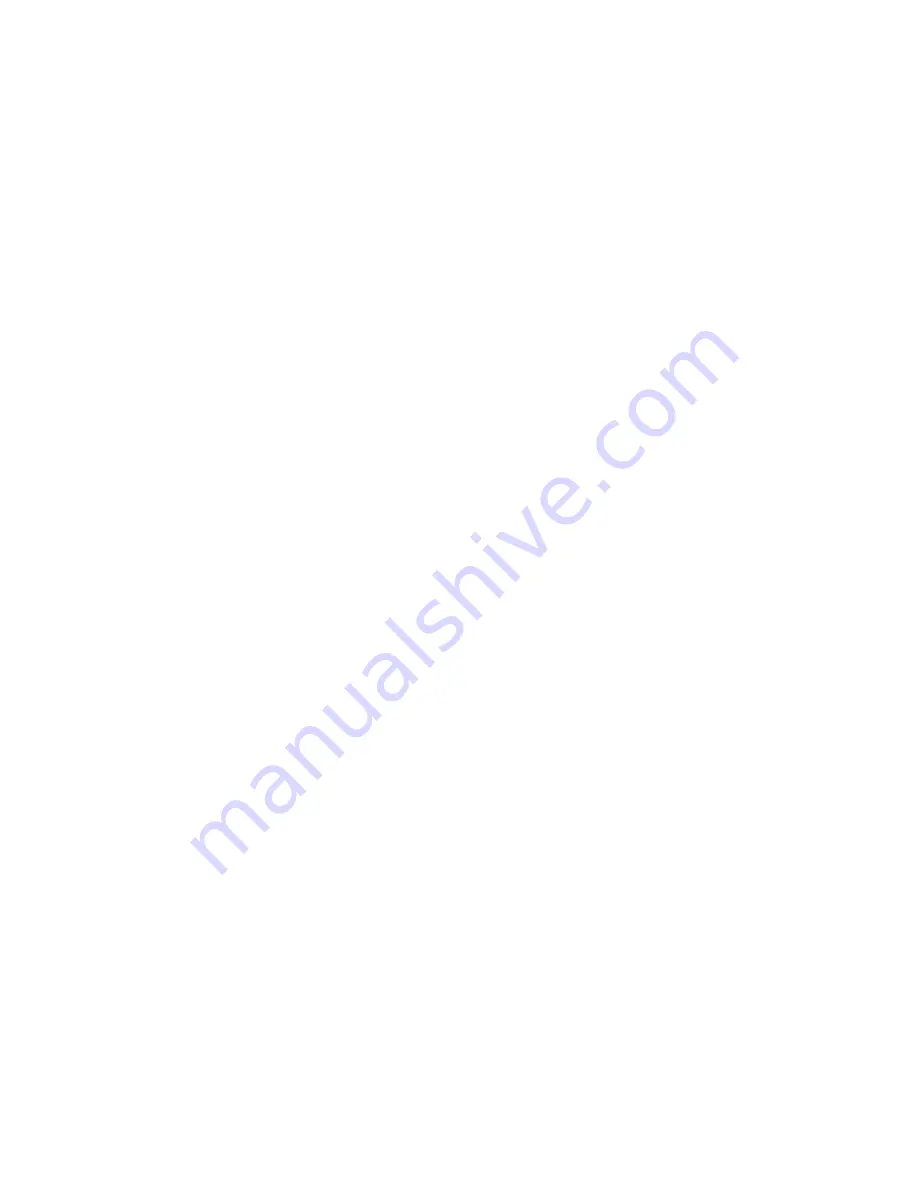
Fan on - 60
o
C
Fan off - 30
o
C
Overheat limit - 100
o
C
Also check that the white button (automatic) is
pulled outward and that the red button (reset)
is pushed inwards to the reset position.
(k) Ensure that the burner is securely attached
to the heater.
(l) Test for electrical earth continuity between
the heater, oil pipe work, and mains supply.
(m) Turn on main electrical supply, select the
following switch settings
Heat/Ventilation - Ventilation
The fan will start enabling fan direction etc
to be verified. Reset on/off switch to off
position.
(n) Turn mains electrical supply to off, replace
and secure lower louver panel covering fan
and motor assembly.
(o) Set thermostat to 'demand' position.
4.2 Commissioning - Ignition
Warning
Do not proceed with commissioning unless all
the criteria detailed within sections 4.0 and 4.1
have been satisfied.
(a) Ensure that the electrical supply is turned
off.
(b) Ensure that the oil supply is turned off.
(c) Select the following switch settings on the
heater
Heat/Ventilation - Heat
(d) Turn on main electrical supply.
(e) Select 'on' position for heater on/off switch.
(f) Check for the following burner sequence
Interval Operand
1 <5s Combustion air damper actuated,
burner fan motor initiates purge
cycle...
2 <15s Solenoid valve opens ignition
transformer provides spark for
burner ignition...
E I T H E R --------
3 >15s Ignition failure caused by oil
starvation resulting in burner lock-
out/shut-down...
(g) Set heater on/off switch to off position
(h) Attach oil manifold (bleed screw and
pressure gauge)
(i) Open oil supply valves and bleed air from
pipe work and adjust burner oil pressure as per
detailed in burner manual Repeat steps 4.1 q,
and 4.2 c,e,f.
--------- O R ------------
4 >15s Burner ignition.flame detection...
5 <20s Burner ignition cycle complete
Note
It is strongly recommended that the separate
manual concerning the operational details of
the burner supplied with the heater as part of
the information package is studied prior to
commissioning.
Time intervals within the ignition sequence will
vary slightly from one model to another.
Warning
If burner ignition is not satisfactorily
accomplished, commissioning must not
proceed until the reason or fault has been
identified and rectified, if necessary by
reference to the separate burner information or
to section 6 of this manual.
(
k) Repeat steps 4.2 c,a,
Summary of Contents for MH300
Page 2: ......
Page 22: ...Wiring Diagram 20 49 146...