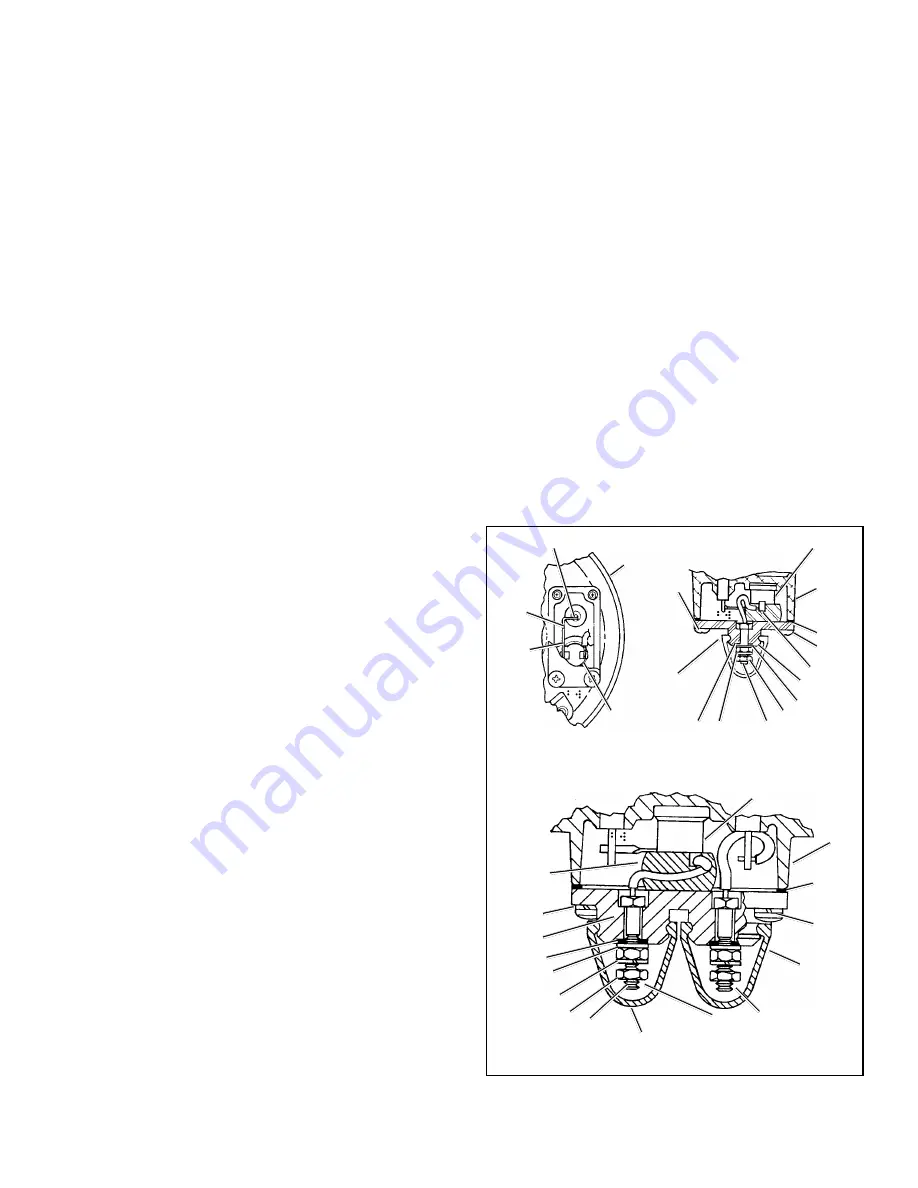
5
2. Check mounting bolts for tightness. Retorque to 270-
385 inch pounds.
3. Perform the Operation & Leakage Tests listed in this
publication.
Every 10,800 hours or 300,000 miles or 36 months:
1. Rebuild the air dryer including the desiccant cartridge.
Note: The desiccant change interval may vary from vehicle
to vehicle. Although typical desiccant cartridge life is three
years, many will perform adequately for a longer period of
time. In order to take maximum advantage of desiccant life
and assure that replacement occurs only when necessary,
it is important that Operation & Leakage Tests be performed.
WARNING!
This air dryer is intended to remove moisture and other
contaminants normally found in the air brake system.
Do not inject alcohol, anti-freeze, or other de-icing
substances into or upstream of the air dryer. Alcohol
is removed by the dryer, but reduces the effectiveness
of the device to dry air. Use of other substances can
damage the air dryer and may void the warranty.
OPERATION & LEAKAGE TESTS
1. Test the outlet port check valve assembly by building
the air system to governor cut-out and observing a test
air gauge installed in the supply reservoir. A rapid loss of
pressure could indicate a failed outlet port check valve.
(Note: Purge valve will be open when governor cut-out
pressure is reached. Allow 45 seconds after governor
cut-out occurs to complete the purge cycle before testing
the check valve.) Coat the exhaust with a soap solution.
Leakage should not exceed a 1" bubble in 1 second.
2. Check for excessive leakage around the purge valve.
With the compressor in loaded mode (compressing air),
apply a soap solution to the purge valve housing
assembly exhaust port and observe that leakage does
not exceed a 1" bubble in 1 second. If the leakage
exceeds the maximum specified, service the purge valve
housing assembly.
3. Close all reservoir drain cocks. Build up system pressure
to governor cut-out and note that AD-4
™
air dryer purges
with an audible escape of air. “Fan” the service brakes
to reduce system air pressure to governor cut-in. Note
that the system once again builds to full pressure and is
followed by an AD-4
™
air dryer purge.
4. Check the operation of the safety valve by pulling the
exposed stem while the compressor is loaded
(compressing air). There must be an exhaust of air while
the stem is held and the valve should reseat when the
stem is released.
5. Check all lines and fittings leading to and from the air
dryer for leakage and integrity.
6. Check the operation of the end cover heater and
thermostat assembly during cold weather operation as
follows:
A. Electric Power to the Dryer
With the ignition or engine kill switch in the ON
position, check for power at the dryer’s electrical
terminal using a voltmeter or test light. On a single
terminal AD-4
™
air dryer’s disconnect the lead wire
at the end cover terminal post. Place the test leads
on the lead wire and a GOOD vehicle ground. On
dual terminal AD-4
™
air dryer’s disconnect both lead
wires at the end cover terminal posts. If there is no
voltage indicated, look for a blown fuse, broken wires,
or corrosion in the vehicle wiring harness. Check to
see if a good ground path exists.
B. Thermostat and Heater Operation
Turn off the ignition switch and cool the end cover
assembly to below 40 degrees Fahrenheit. Using an
ohmmeter, check the resistance between the
electrical terminal and the metal end cover (see Figure
5). (Note: On the dual terminal end cover, check the
resistance between the two terminals.) The
FIGURE 5 - AD-4
™
AIR DRYER SINGLE AND DUAL
TERMINAL THERMOSTAT ASSEMBLIES
DUAL WIRE SYSTEM
BOOT
7
10
9
1
11
8
6
1
CONNECTIONS FOR POWER
AND INSULATED RETURN
BOOT
3
2
4
5
BOLD NUMBERS ARE ITEMS IN MAINTENANCE KITS
SINGLE WIRE SYSTEM
1
9
8
1
9
2
1
4
6
11
7
10
THERMOSTAT
COVER
5
3
A
B
HEATER POST