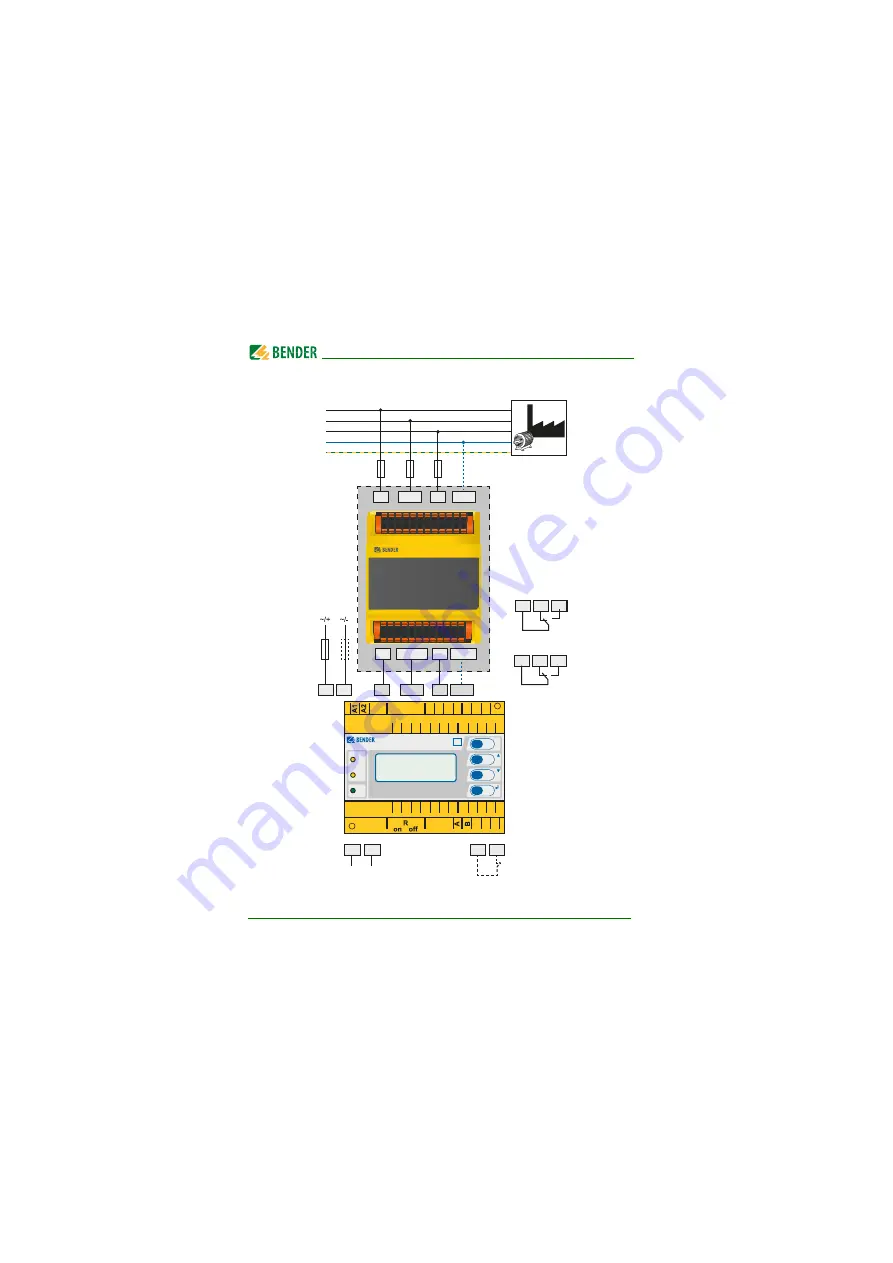
Installation and connection
28
VMD461_D00314_01_M_XXEN/10.2018
4.9.4
3(N)AC: VMD461 with CD440 (earthed system)
Fig. 4.7: Wiring diagram VMD461 with CD440 (earthed system)
*
CD440 optional
L1'
L2'/DC+'
L3'
11
21
24
12
22
A
B
RTG
RT1
14
N'/DC-'
K1
K2
A1
A2
U
S
6 A
6 A
CD440
L1
L3 N/DC-
L2/DC+
L1'
L3' N'/DC-'
L2'/DC+'
L1
L2
L3
N
L1
L2/DC+
L3
N/DC-
6 A
6 A
6 A
PE
11
12
14
21
22
24
L3
L2/DC+
L1
D2
D1
DG1/2
RTG
RT1
2
1
ON
ALARM
MENU
INFO
TEST
RESET
ESC
LINETRAXX®
VMD461
V
N/DC-
L1
L2/DC+
L3
N/DC-
Summary of Contents for LINETRAXX VMD461
Page 6: ......
Page 40: ...Operation and configuration 40 VMD461_D00314_01_M_XXEN 10 2018 ...
Page 66: ...Menu 66 VMD461_D00314_01_M_XXEN 10 2018 ...
Page 80: ...Technical data VMD461 80 VMD461_D00314_01_M_XXEN 10 2018 ...
Page 83: ......