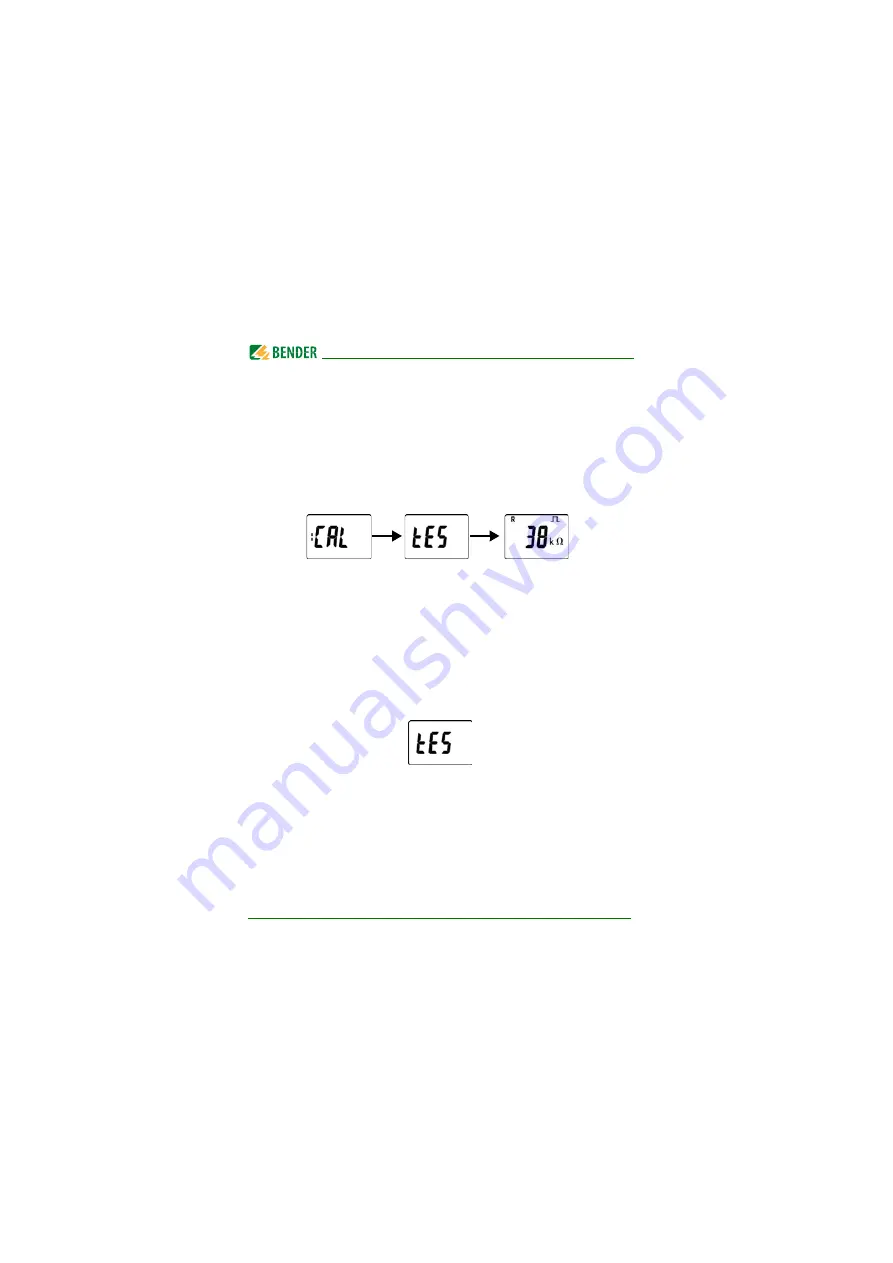
Installation, connection and commissioning
28
isoEV425_D00126_09_M_XXEN/03.2019
4.3
Commissioning
1.
Check that
the ISOMETER® is properly connected to the system to be
monitored.
2.
Connecting supply voltage
U
s
to the ISOMETER®
The device carries out a calibration, a self test and adjusts itself to the IT
system to be monitored. When high system leakage capacitances are
involved, this procedure may take up to 4 min. The standard display
then appears showing the present insulation resistance, e.g.:
The pulse symbol signals an error-free update of the resistance and
capacitance measured values. If the measured value cannot be
updated due to disturbances, the pulse symbol will be hidden.
3.
Start a manual self test
by pressing the test button "T". Whilst the test
button is pressed and held down, all display elements available for this
device are shown. During the test, the "tES" symbol flashes. Any inter-
nal malfunctions detected are shown on the display as error codes
(see
). The alarm relays are not checked during the test (factory
setting). The setting can be changed in the "out" menu, so that the
relays switch to the alarm state during the manual self test.
4.
Checking factory settings for suitability
Are the settings suitable for the installation to be monitored?
The list of factory settings are shown in the table in
5.
Checking the function using a genuine insulation fault
The ISOMETER® in the system being monitored can be checked using,
for example, a suitable resistance to earth.