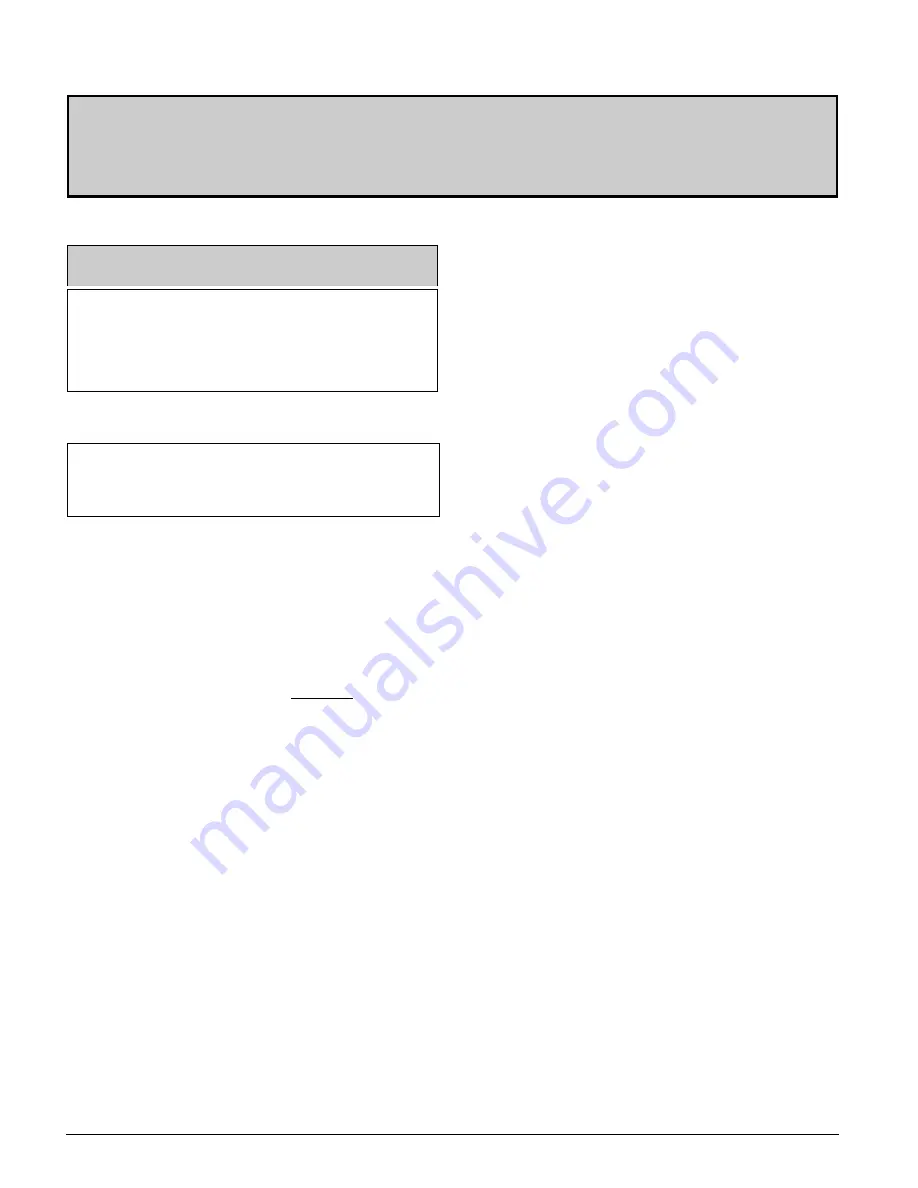
Belshaw Bros., Inc.
•
1750 22
nd
Ave. S.
•
Seattle, WA 98144
•
Phone 206-322-5474
•
Fax 206-322-5425
4 MN-1716EN
Thermoglaze
50
Installation 3
WARNING
To avoid electrocuting yourself or damaging
the Thermoglaze, never allow water, steam,
cleaning solution, or other liquid to enter the
electrical panels or connections
Electrical:
Model Dimensions Power
Requirements
TG21586
88"L x 40W x
63"H
See data tag
Make sure that the power requirements of the
Thermoglaze, shown on the data plate, match
your power source.
Only plug in to power source that matches the
required voltage and current for the
Thermoglaze. (The Thermoglaze unit TG50
comes standard with a Hubbel 360P6W plug that
needs a 360C6W socket or equivalent for
electrical current.
Thermoglaze must be electrically grounded and
connected in compliance with the National
Electrical Code, ANSI-NFPA 70, and applicable
municipal building codes.
Do not apply electrical power to the system until
the assembly has been completed. See Section 4
for the assembly of the Thermoglaze.
Venting:
Local codes prevail. The authorities having
jurisdiction are stated in NFPA 96-1994
regarding requirements for the Thermoglaze.
Building Layouts:
Specification sheets and AutoCAD drawings for
use in developing architectural drawings can be
provided by request. Please call your Belshaw
Bros., Inc. representative for help in defining
your requirements.