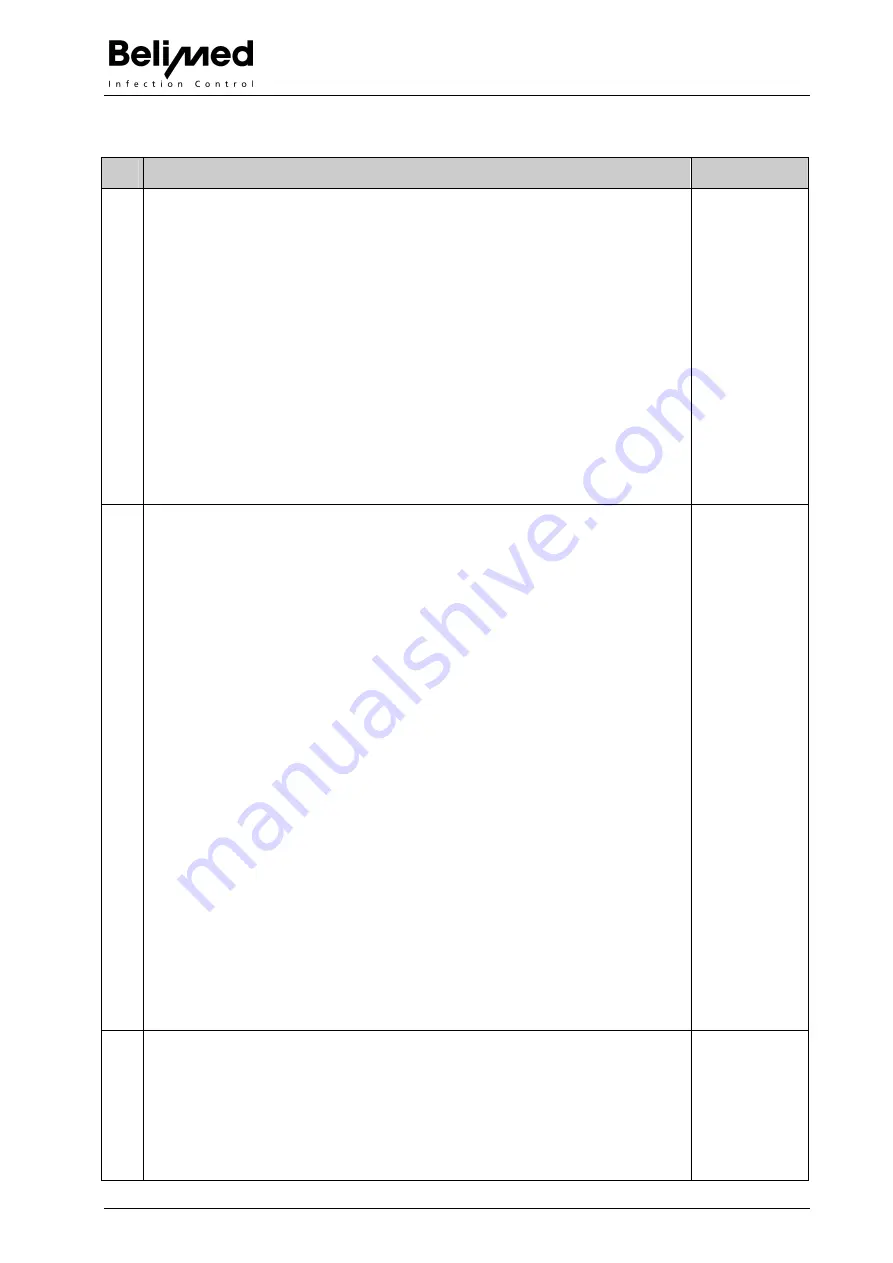
Technical Manual WD 230 and WD 250
Rev. 1.8 PF
Page 44
73018_E rev 1 8-Technical Manual.doc
8.3 Error code / Error chart / Remedy
Error / Cause
Display
100
On door US, Reed sensor S 1 or auxiliary relays K1 is not closed or the potenti-
ometer value is not within the proper range or has changed during the current
program.
Query input S110/111 and R1/2 only during current program.
Cause:
Remedy:
Door switch S1 is closed S110
defect, cable break, adjust
Signal cable linear drive interrupted
interrupt of cable of con-
nector
Linear drive
replace
Relay K1
replace
Actual value pot meters not in target range
readjust doors
Chack all plug connections
Door is open
Error code 100
101
(Only for WD 250/) The opening sequence of
US
door takes more than 20 sec-
onds or the linear drive is defective.
Control system will interrupt the opening sequence and display error if either the
opening process for door with lifting motor US (M 35) takes more than 16 sec-
onds until the lower Reed S 112) or the potentiometer value remains within the
‘closed’ range.
Query input S 112, R1 only during opening procedure.
Cause:
Remedy:
Manual linear drive on door panel print (buttons)
Open
re-calibrate door, ex-
change
Linear
motor
Activate door drive motor M 35 with control K35
replace door motor or ca-
pacitor
Reed sensor S 112 does not open
replace S 112
Check all plug connections
re-crimp S 112 to print
Safety relay ESR 1
Relay ESR 1 LED green
no action required
LED yellow = resistance incorrect
replace safety strip
LED red = cable break
replace safety strip or find
Cable
break
Door does not
open
Error code 101
102
The closing process of the
US
door takes more than 20 seconds or linear drive
is defective.
The control system will interrupt closing sequence and displays error if either
the closing procedure of door with lifting motor US (M 35) takes in excess of 16
seconds until the upper Reed sensor (S 1/K1) closes or until the potentiometer
value R1 comes within ‘closed’ range.
Query of input S 110, R1 only during closing process.
Door does not
close
Error code 102