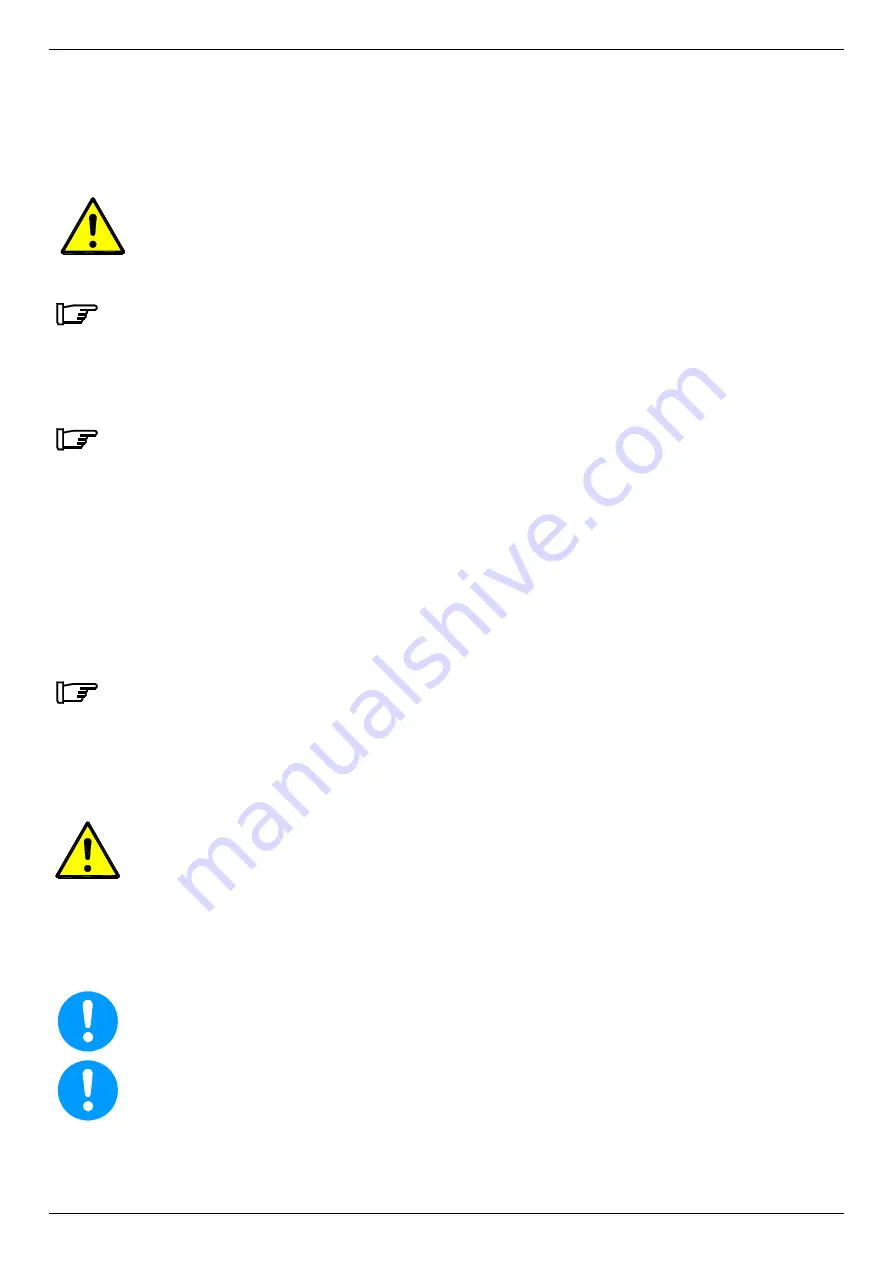
Start-up
DRYPOINT® RA CT 20-500 NA
27
In the cycling operating mode (Energy Saving, ESS=YES – see section 8.12.7), the refigerating compressor is
switched ON and OFF by the DMC51 electronic control unit, according to thermal load applied to the dryer.
The dryer needs to be switched on during the entire compressed-air usage time, even if the compressed-air
compressor works periodically.
10.3 Shut down and restart
RA CT 200-500 3phase - during short-term inactivity (max. two to three days), it is advisable to leave the
dryer and the control panel connected to the supply current circuit. Otherwise, it would be necessary at a
restart of the dryer to wait two hours, until the crankcase heater of the compressor has heated up the oil
in the compressor.
Shut down (see Section 8.1 "Control panel")
• Ensure that the dew point temperature indicated on the DMC 51 electronic control unit is stable.
• Bypass the compressed-air supply.
• After a few minutes, stop the dryer by switching off the ON-OFF switch on the control panel (pos. 1).
Restart (see Section 8.1 "Control panel"
)
• Make sure that the condenser is clean.
• Start the dryer by switching on the ON-OFF switch on the control panel (pos. 1).
• Ensure that the DMC 51 electronic control unit is switched on.
• If the temperature displayed on the DMC51 electronic control unit is sufficiently high, verify that the refrigerating
compressor starts within a few minutes.
NOTE!
– With low temperatures, the refrigerating compressor will remain
OFF
• Wait a few minutes and then check whether or not the dew point temperature indicated on the DMC 51 electronic
control unit is stable
• Establish the compressed-air supply.
• Check that the condensate is regularly drained
RA CT 200-500 3phase - dryer remote control ON/OFF
• Remove the jumper between terminals 1 and 2 of the terminal strip and wire a potential-free contact (see electric
diagram).
• Switch ON the main switch - pos. 1 on the control panel.
• Close the contact at terminals 1 and 2 to switch on the dryer.
• Open the contact at terminals 1 and 2 to switch off the dryer.
Only use potential-free contacts that are suitable for 230 Vac. Ensure the sufficient insulation of
potentially dangerous voltage-carrying components.
In the cycling operating mode (Energy Saving, ESS=YES – see section 8.12.7), the refigerating compressor is
switched ON and OFF by the DMC51 electronic control unit, according to thermal load applied to the dryer.
The dryer needs to be switched on during the entire compressed-air usage time, even if the compressed-air
compressor works periodically.
Note!
A dew point between 32°F (0°C) and +50°F (+10°C)
displayed on the DMC 51 control unit is considered
to be correct according to the possible operating conditions (flow rate, air inlet temperature, ambient
temperature etc.).
Note!
The number of starts/stops by pressing the ON-OFF switch - pos. 1 control panel should be limited to six
per hour.
Irreparable damage can be caused by starting up the device too often.
Summary of Contents for DRYPOINT RA CT 100-NA-EB
Page 39: ...Maintenance troubleshooting spare parts and dismantling DRYPOINT RA CT 20 500 NA 39 ...
Page 40: ...Maintenance troubleshooting spare parts and dismantling 40 DRYPOINT RA CT 20 500 NA ...
Page 43: ...Appendices DRYPOINT RA CT 20 500 NA 43 13 1 2 Dryer dimensions DRYPOINT RA CT 75 NA ...
Page 44: ...Appendices 44 DRYPOINT RA CT 20 500 NA 13 1 3 Dryer dimensions DRYPOINT RA CT 100 150 NA ...
Page 45: ...Appendices DRYPOINT RA CT 20 500 NA 45 13 1 4 Dryer dimensions DRYPOINT RA CT 200 250 NA ...
Page 46: ...Appendices 46 DRYPOINT RA CT 20 500 NA 13 1 5 Dryer dimensions DRYPOINT RA CT 300 350 NA ...
Page 47: ...Appendices DRYPOINT RA CT 20 500 NA 47 13 1 6 Dryer dimensions DRYPOINT RA CT 400 500 NA ...
Page 52: ...Appendices 52 DRYPOINT RA CT 20 500 NA 13 2 2 Exploded diagram DRYPOINT RA CT 20 30 NA ...
Page 53: ...Appendices DRYPOINT RA CT 20 500 NA 53 13 2 3 Exploded diagram DRYPOINT RA CT 50 NA ...
Page 54: ...Appendices 54 DRYPOINT RA CT 20 500 NA 13 2 4 Exploded diagram DRYPOINT RA CT 75 NA ...
Page 55: ...Appendices DRYPOINT RA CT 20 500 NA 55 13 2 5 Exploded diagram DRYPOINT RA CT 100 NA ...
Page 56: ...Appendices 56 DRYPOINT RA CT 20 500 NA 13 2 6 Exploded diagram DRYPOINT RA CT 125 150 NA ...
Page 57: ...Appendices DRYPOINT RA CT 20 500 NA 57 13 2 7 Exploded diagram DRYPOINT RA CT 200 250 NA ...
Page 58: ...Appendices 58 DRYPOINT RA CT 20 500 NA 13 2 8 Exploded diagram DRYPOINT RA CT 300 350 NA ...
Page 59: ...Appendices DRYPOINT RA CT 20 500 NA 59 13 2 9 Exploded diagram DRYPOINT RA CT 400 500 NA ...
Page 72: ...Appendices 72 DRYPOINT RA CT 20 500 NA ...
Page 73: ...Appendices DRYPOINT RA CT 20 500 NA 73 ...