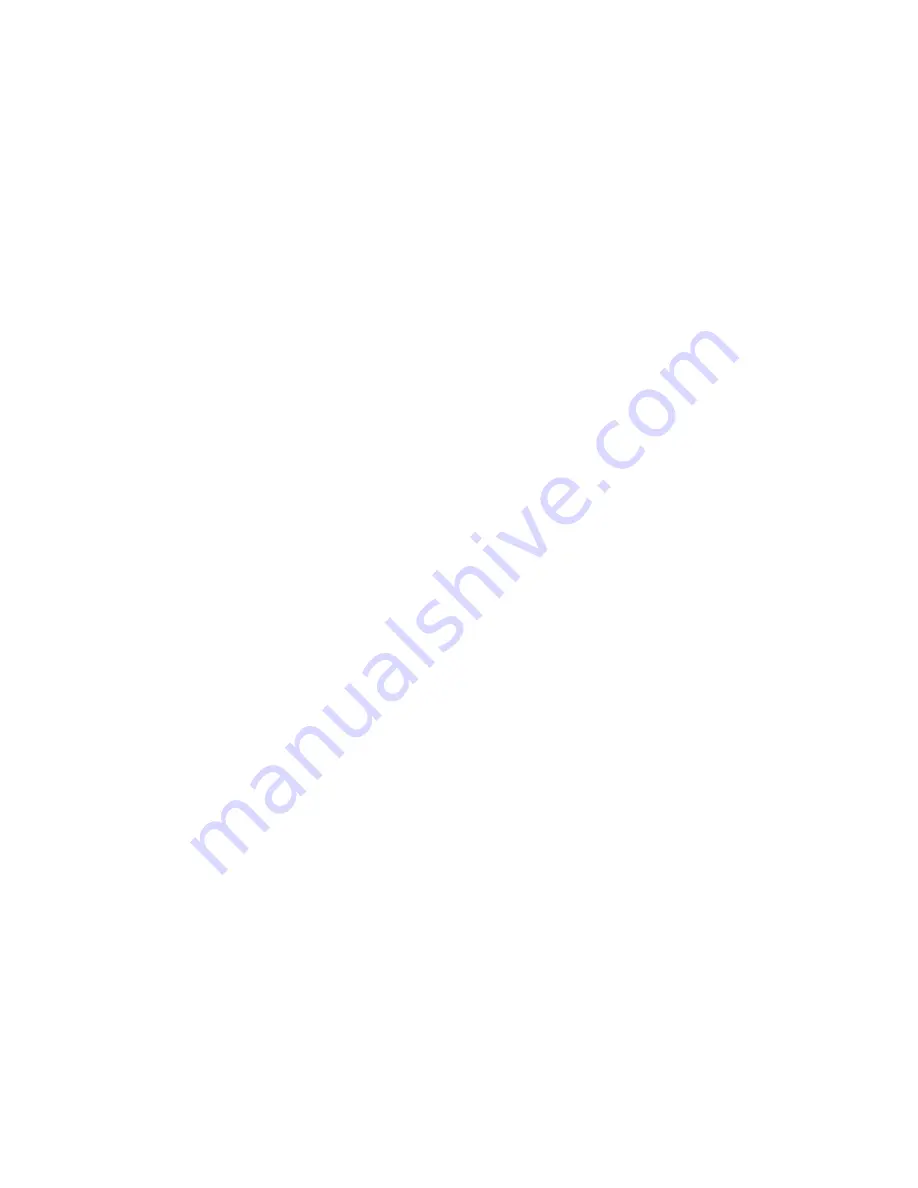
CLEARPOINT® Flanged L100-L304_us_en_2014-6 (rev. A)
6
•
CLEARPOINT®
filters, including accessories, must be checked once a week. This applies in particular to the
function of the drain. Please refer to page 10 check list.
AREAS OF APPLICATION
CLEARPOINT® filters are designed for the separation of solid particles, aerosols, oil vapors and orders from non-
aggressive compressed air or industrial gases. Depending on the specific application, the filter housings are provide with
different insert:
C Coarse filter for the separation of coarse solid matter pollutants up to 25 µm
G General Purpose filter element for the separation of large dirt particles up to 5 µm
F Fine filter element for the separation of liquids up to 0.1 mg/m3 and solid particles up to 1 µm
S Super fine filter element for the separation of liquids up to 0.01 mg/m3 and solid particles up to 0.01 µm
N Nano filter element for the separation of liquids up to 0.003 mg/m3 and solid particles up to 0.01 µm
A Activated carbon filter elements for the separation of oil vapors up to 0.003 mg/m3 and odors
R (x) Dust filter for the separation of solid particles, fineness depends of the grade. Refer to C to N above.
FUNCTION
Filter C, G, F, S, and R(X)
Solid particles are separated by impact and inertia effect, oil and water aerosols by coalescence effect. Due to gravity,
filtered out liquid particles gather in the lower part of the filter housing from where they are discharged either manually
or automatically. With coalescence filters the direction of flow through the filter elements is from the inside to the
outside; with dust filters the flow moves from outside to inside.
Activated carbon filter A
The flow through the activated carbon bed proceeds from the inside to outside. Oil vapors and odors are adsorbed on the
activated carbon. The carbon is incorporated into a binding fabric which ensures the reliable retention of dust particles.
ECONOMIC EFFICIENCY OF FILTERS
Surface and depth filters
Series C, G, F, S, and R(X)
In the course of time, particles accumulate in the filtration medium and reduce the space available for flow.
Consequently, the flow resistance will gradually increase, which is indicated on the differential pressure gauge.
It is recommended to replace the filter elements at a differential pressure of 10 psi or at least once a year, whichever
comes first. If the element replacement is delayed any longer, the economic efficiency will suffer since the higher
differential pressure has to be compensated by the by the upstream compressor. This will push up the electricity
consumption and lead to greater wear on the compressor.
Activated carbon filter, Series A
In order to prolong the service life of the elements, the residual moisture of the inflowing gas should not exceed 80%.
Elements will reach loading capacity after approximately 6 months, requiring replacement at that time.