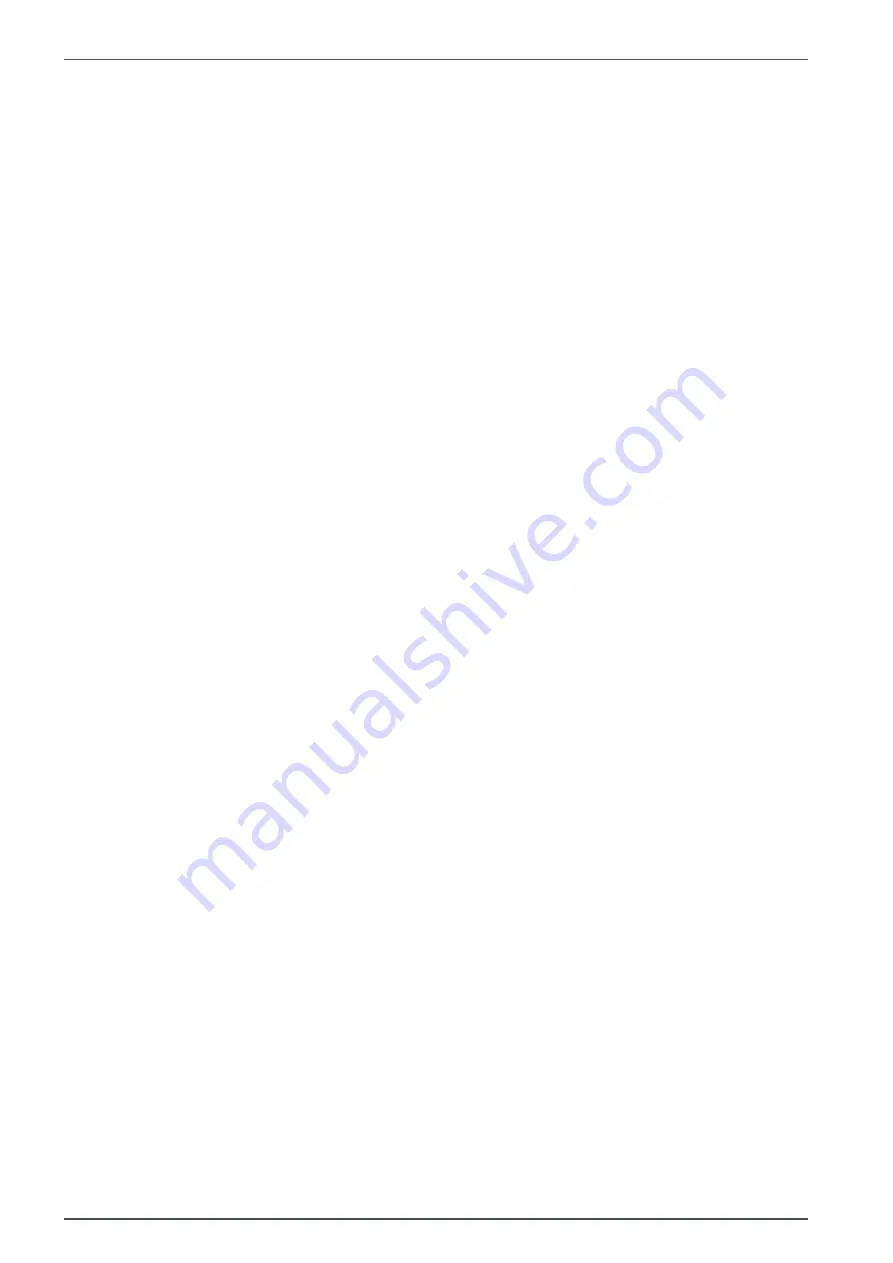
1.6 Resonably foreseeable inappropriate use
Reasonably foreseeable inappropriate use is deemed to have occurred if the filter or any accessories are used in any
other way than that described in the chapter "Intended use". Reasonably foreseeable inappropriate use includes the use
of the product in a manner not intended by the manufacturer or supplier but which may result from foreseeable human
behaviour.
Reasonably foreseeable inappropriate use includes:
•
Executing of modifications of all kinds, in particular design and process engineering interventions, as these can lead
to personal injury and material damage as well as functional and operational malfunctions and device failure.
• The overriding, bridging or non-application of existing or recommended safety devices.
•
The use for treatment of compressed gases which are are not included in fluid group 2 in accordance with PED
2014/68/EU or contain aggressive components. In cases of doubt a gas/condensate analysis must be carried out.
This list is not exhaustive as not all possible inappropriate use can be foreseen in advance. If the operating company is
aware of any inappropriate use of the filter or accessories which are not listed here, the manufacturer must be informed
immediately.
1.7 Legal warranty and liability for property defects
The owner and operator must take into account the intended use. The owner and operator will be completely liable for
every not described action and utilisation which exceeds the stated intended use.
All liability or warranty claims will be invalidated insofar as the filter is not operated according to the intended use or is
operated outside the limits specified in the technical data.
This includes:
• incorrect technical installation, commissioning, servicing, maintenance or operation
• the use of defective components
• non-compliance with the safety-relevant information, action steps and instruction contained in this manual
•
the performance of any kind of modification, in particular constructive and process technology interventions on the
product
• the use of third-party spare parts or accessories, which have not been approved by the manufacturer, during
maintenance and repair work
• Non-compliance with servicing, maintenance and inspection intervals
CLEARPOINT
®
3
eco
coalescing filter
Installation and operation manual
8 | 56