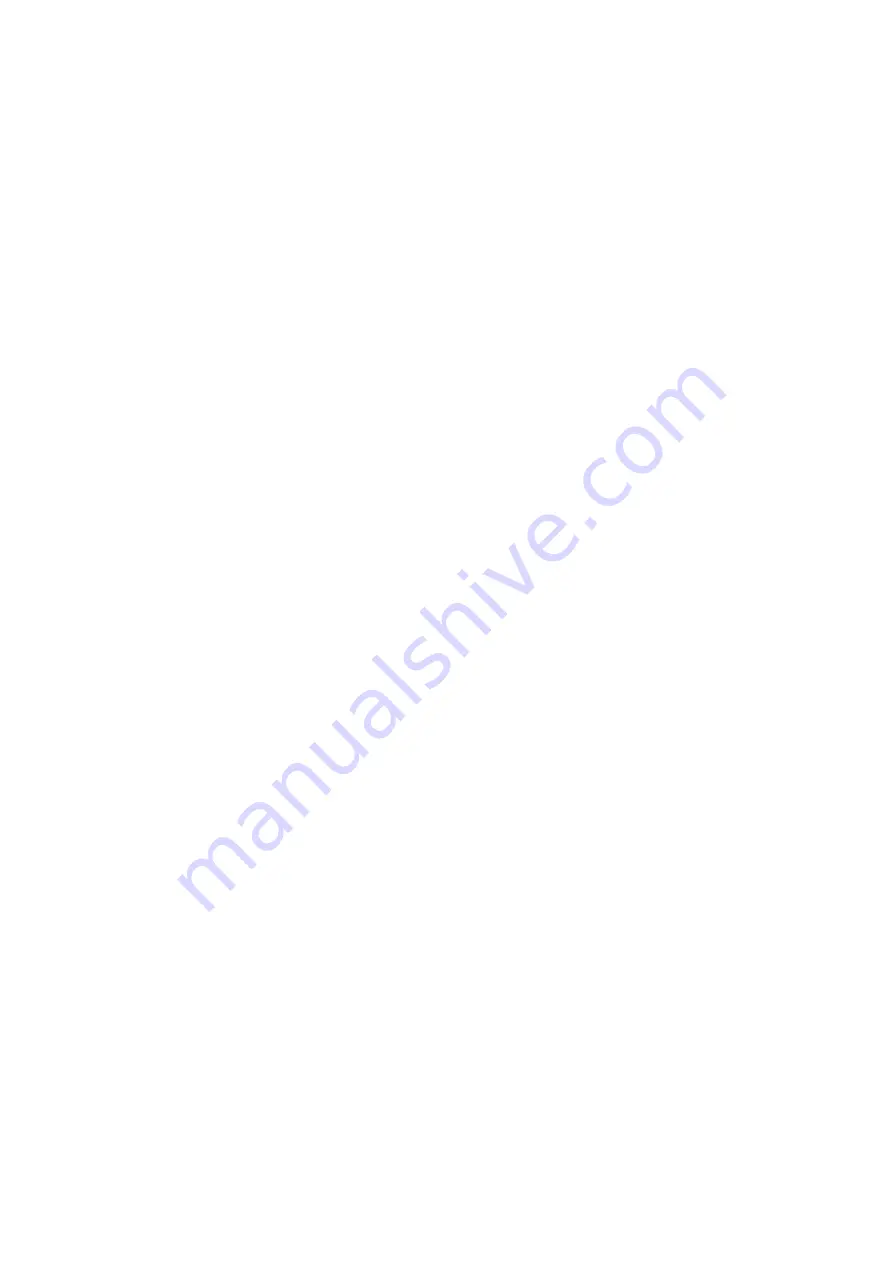
23
9.3.1
Calibration using an external current
source
This method allows direct calibration with a current
source, and is preferred when traceability is
required. If the exact system non-linearity is
unknown, this method also allows direct calibration
from the variable to be displayed. e.g. The output
from a level sensor in an irregular tank may be
displayed in linear volumetric units by filling the
tank with known incremental volumes and
calibrating the indicator to display the sum of the
increments at each break-point.
The number of break-points required should first
be entered using the 'Add' and 'dEL' functions. In
both these functions the indicator initially displays
the current break-point and the total number of
break-points being used. e.g.
5
13
current
total number of
break-point
break-points
Display
Description of function
'Add'
Add a break-point
Adds a new break-point before the
displayed break-point. The calibration
of existing break-points is not
changed, but the identification number
of all subsequent break-points is
increased by one.
'dEL'
Remove a break-point
Removes the displayed break-point
and joins the preceding break-point to
the following break-point with a
straight line. The identification
number of all subsequent break-
points is decreased by one.
To add a break-point select 'CAL' from the main
menu and press
P
to enter the 'Add' function;
press
P
again to reveal the current and total
number of break-points. Each subsequent
operation of the
P
push-button will introduce an
additional break-point. When adding a break-
point to a calibrated indicator, the insertion position
can be selected using the
Up
and
Down
push-
buttons.
The delete break-point function 'dEL' operates in a
similar manner to the 'Add' function described
above.
When the required number of break-points has
been entered, return to the sub-menu by pressing
E
. The indicator will display 'Add' or 'dEL'
depending upon the last function used. Each
break-point can now be programmed.
Select 'PtS' from the sub-menu and press
P
which
will select the first break-point '0 n', where n is the
total number of break-points entered. The
selected break-point can be changed using the
Up
and
Down
buttons. When the required break-point
has been selected press
P
. Set the indicator input
current to the exact value at which the break-point
is to occur, and adjust the indicator display using
the
Up
and
Down
buttons and
P
to move between
digits. When the required display has been set,
press
E
to enter the information and return to the
sub-menu from which another break-point can be
selected.
Repeat this procedure for each break-point, and
then return to the main menu by pressing
E
twice.
9.3.2 Calibration using internal references
This function enables the break-points to be
adjusted without the need for an accurate external
current source. Throughout calibration the
indicator input current may be any value between 4
and 20mA.
The accuracy of this method depends upon the
accuracy of the internal references which should
be calibrated periodically against a traceable
external current source with a resolution of at least
0.4µA. See section 6.7.2
The number of break-points required should first
be entered using the Add and dEL functions. In
both these functions the indicator initially displays
the current break-point and the total number of
break-points being used. e.g.
5
13
current
total number of
break-point
break-points