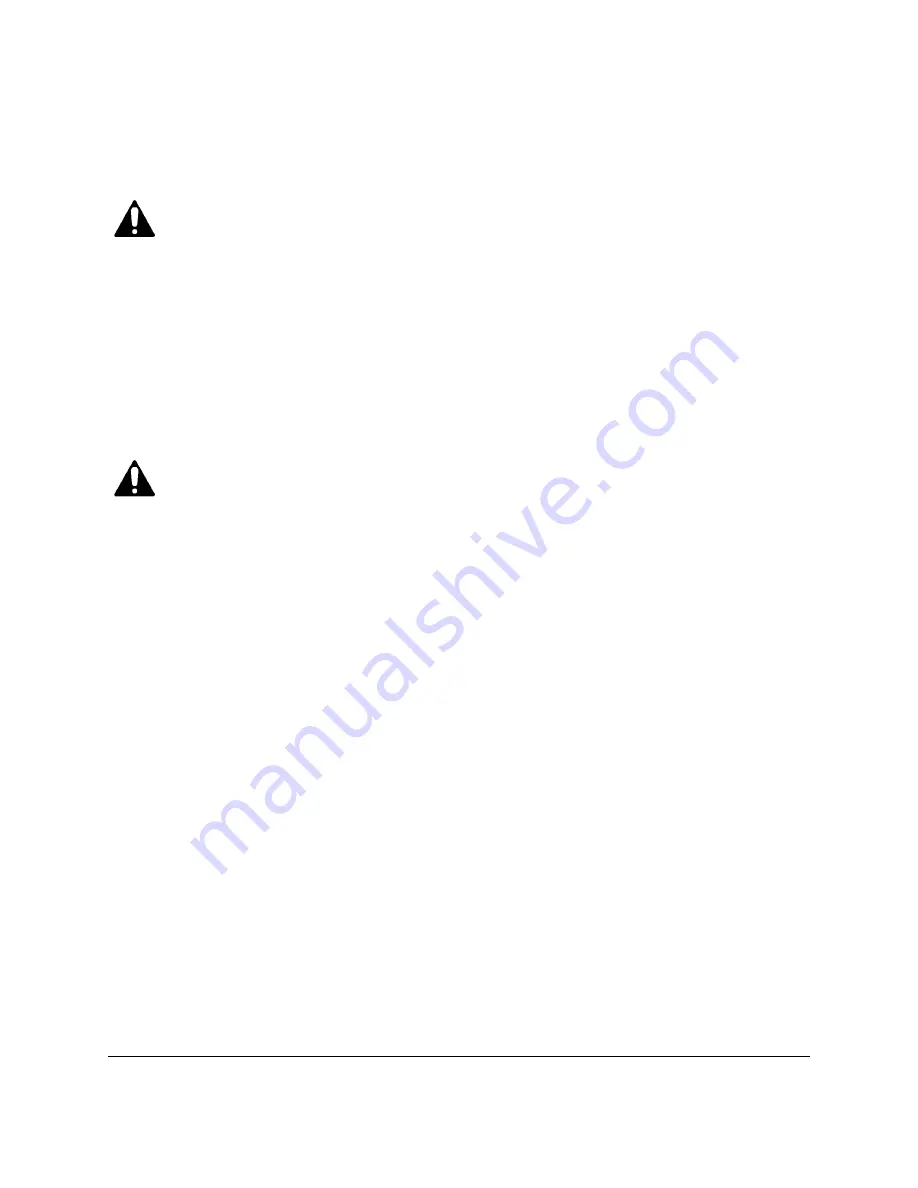
4 - MAINTENANCE
DANGER: Stop engine, lock parking brake and remove key before performing any
service or maintenance.
Never rely on the tractor lift system. Install blocks or stands under the machine to
prevent it from falling. Always use personal protection devices, such as glasses
or gloves when performing maintenance.
Keep fingers out of slots to prevent injury.
4.01 - Maintenance Safety
1. Good maintenance is your responsibility.
2. Keep service area clean and dry. Be sure electrical outlets and tools are properly
grounded. Use adequate light for the job at hand.
3. Make sure there is plenty of ventilation. Never operate the engine of the towing
vehicle in a closed building. The exhaust fumes may cause asphyxiation.
4. Make no repair or adjustments with the tractor engine running. Before working on
the machine, disengage the
PTO,
shut off the engine, set the brakes, and remove
the ignition key.
5. Be certain all moving parts on attachment have come to a complete stop before
attempting to perform maintenance.
6. Never work under equipment unless it is blocked securely.
7. Always use personal protection devices such as eye, hand and hearing protectors,
when performing any service or maintenance.
8. Frequently check blades. They should be sharp, free of nicks and cracks and
securely fastened.
9. Periodically tighten all bolts, nuts and screws and check that all cotter pins are
properly installed to ensure unit is in a safe condition.
10. When completing a maintenance or service function, make sure all safety shields
and devices are installed before placing unit in service.
11. After servicing, be sure all tools, parts and service equipment are removed.
12. Never replace hex bolts with less than grade five bolts unless otherwise specified,
i.e. shear bolts
10
.
13. Where replacement parts are necessary for periodic maintenance and servicing,
genuine replacement parts must be used to restore your equipment to original
specifications. The company will not claim responsibility for use of unapproved parts
and/or accessories and other damages as a result of their use.
M
AINTENANCE
25
BEFCO
T
ILL
-R
ITE
T60
O
PERATOR
’
S
M
ANUAL
10
Refer to Table 2 - Torque Specifications, for head identification marking, page 30.
Summary of Contents for TILL-RITE T60-266
Page 40: ...TILL RITE T60 FRAME OPERATOR S MANUAL T60 266 366 274 374 PARTS MANUAL 40 BEFCO 01 2014...
Page 42: ...TILL RITE T60 FRAME OPERATOR S MANUAL T60 266 366 274 374 PARTS MANUAL 42 BEFCO 01 2014...
Page 44: ...TILL RITE T60 FRAME OPERATOR S MANUAL T60 266 366 274 374 PARTS MANUAL 44 BEFCO 01 2014...
Page 50: ......