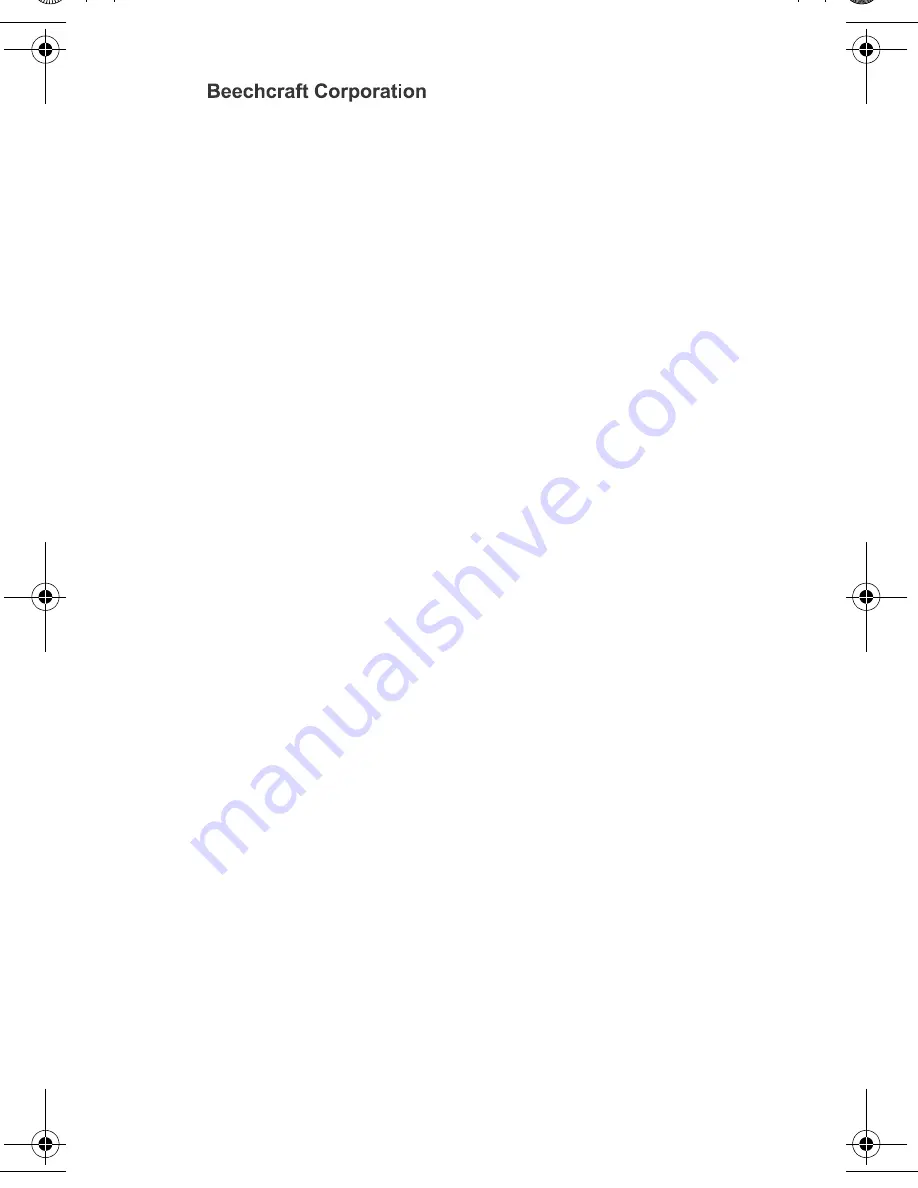
Limitations
Section 2
Model G58
2-13
PROPELLER DEICE AMMETER
Normal Operating Range (Green Arc) . . . . . . . . 14 to 18 amps
WEIGHT LIMITS
Maximum Take-off . . . . . . . . . . . . . . . . . . . . . . . . . . . 5500 lbs
Maximum Landing . . . . . . . . . . . . . . . . . . . . . . . . . . . 5400 lbs
Maximum Ramp . . . . . . . . . . . . . . . . . . . . . . . . . . . . 5524 lbs
Maximum Baggage Compartment Weights:
Main Cabin Compartment
(less occupants and equipment). . . . . . . . . . . . . . . . . . 400 lbs
Extended Aft Compartment . . . . . . . . . . . . . . . . . . . . . 120 lbs
Nose Compartment
(baggage and equipment combined) . . . . . . . . . . . . . . 300 lbs
Refer to Section 6, WEIGHT AND BALANCE/EQUIPMENT
LIST for additional information.
CENTER OF GRAVITY
(LANDING GEAR EXTENDED)
Forward Limits: 74.0 inches aft of datum at 4200 lbs and
under, then straight line variation to 78.0 inches aft of datum at
gross weight of 5400 lbs (maximum landing weight) and 78.3
inches aft of datum at gross weight of 5500 lbs.
Aft Limit: 86 inches aft of datum at all weights.
REFERENCE DATUM
Datum is 83.1 inches forward of center line through forward
jack points.
MEAN AERODYNAMIC CHORD
MAC leading edge is 67.2 inches aft of datum.
MAC length is 63.1 inches.
May, 2015
58-590000-67A12_sec02.fm Page 13 Wednesday, May 27, 2015 8:56 AM
Summary of Contents for Baron G58
Page 1: ......
Page 9: ......
Page 62: ...General Model G58 Section 1 1 26 THIS PAGE INTENTIONALLY LEFT BLANK May 2015 ...
Page 66: ...Model G58 2 4 May 2015 Section 2 THIS PAGE INTENTIONALLY LEFT BLANK Limitations ...
Page 138: ...Emergency Procedures Model G58 Section 3 3 30 THIS PAGE INTENTIONALLY LEFT BLANK April 2008 ...
Page 170: ...Model G58 4 4 June 2011 Section 4 Normal Procedures THIS PAGE INTENTIONALLY LEFT BLANK ...
Page 198: ......
Page 228: ...Model G58 5 4 July 2014 Section 5 THIS PAGE INTENTIONALLY LEFT BLANK Performance ...
Page 247: ...Performance Section 5 Model G58 5 23 July 2014 ...
Page 249: ...Performance Section 5 Model G58 5 25 July 2014 ...
Page 250: ...Performance Model G58 Section 5 5 26 July 2014 ...
Page 259: ...Performance Section 5 Model G58 5 35 THIS PAGE INTENTIONALLY LEFT BLANK July 2014 ...
Page 264: ...Performance Model G58 Section 5 5 40 July 2014 ...
Page 265: ...Performance Section 5 Model G58 5 41 July 2014 ...
Page 275: ...Performance Section 5 Model G58 5 51 July 2014 ...
Page 278: ...Performance Model G58 Section 5 5 54 THIS PAGE INTENTIONALLY LEFT BLANK July 2014 ...
Page 288: ...Wt and Bal Equip List Model G58 Section 6 6 10 December 2009 ...
Page 289: ...Wt and Bal Equip List Section 6 Model G58 6 11 December 2009 ...
Page 310: ...Systems Description Model G58 Section 7 7 10 THIS PAGE INTENTIONALLY LEFT BLANK May 2015 ...
Page 312: ...Systems Description Model G58 Section 7 7 12 May 2015 ...
Page 313: ...Systems Description Section 7 Model G58 7 13 May 2015 ...
Page 355: ...Systems Description Section 7 Model G58 7 55 ENVIRONMENTAL SCHEMATIC May 2015 ...
Page 398: ...Systems Description Model G58 Section 7 7 98 THIS PAGE INTENTIONALLY LEFT BLANK May 2015 ...
Page 434: ...Supplements Model G58 Section 9 9 2 THIS PAGE INTENTIONALLY LEFT BLANK November 2005 ...
Page 437: ......
Page 443: ......
Page 448: ...FAA Approved 6 of 6 P N 36 590002 89 Issued April 2009 THIS PAGE INTENTIONALLY LEFT BLANK ...
Page 449: ......
Page 450: ......
Page 451: ......
Page 452: ......
Page 453: ......
Page 454: ......
Page 455: ......
Page 456: ......
Page 457: ......
Page 458: ......
Page 459: ......
Page 463: ......
Page 487: ......
Page 497: ......
Page 510: ......
Page 534: ......
Page 535: ......
Page 553: ......
Page 554: ......
Page 555: ......
Page 556: ......
Page 557: ......
Page 558: ......
Page 559: ......
Page 560: ......
Page 561: ......
Page 562: ......
Page 563: ......
Page 564: ......
Page 565: ......
Page 566: ......
Page 567: ......
Page 568: ......
Page 589: ...7 of 12 P N 58 590000 0089 Issued December 2014 ...
Page 592: ...10 of 12 P N 58 590000 0089 Issued December 2014 ...
Page 594: ...12 of 12 P N 58 590000 0089 THIS PAGE INTENTIONALLY LEFT BLANK Issued December 2014 ...
Page 595: ......
Page 596: ......
Page 597: ......
Page 598: ......
Page 599: ......
Page 600: ......
Page 601: ......
Page 602: ......
Page 603: ......
Page 604: ......
Page 605: ......
Page 606: ......
Page 607: ......
Page 608: ......
Page 609: ......
Page 610: ......
Page 611: ......
Page 612: ......
Page 613: ......
Page 614: ......
Page 615: ......
Page 616: ......
Page 617: ......
Page 618: ......
Page 619: ......
Page 620: ......
Page 621: ......
Page 622: ......
Page 623: ......
Page 624: ......
Page 625: ......
Page 626: ......
Page 627: ......
Page 628: ......
Page 629: ......
Page 630: ......
Page 631: ......
Page 632: ......
Page 633: ......
Page 634: ......
Page 635: ......
Page 636: ......
Page 637: ......
Page 638: ......
Page 639: ......
Page 640: ......
Page 641: ......
Page 642: ......
Page 643: ......
Page 644: ......
Page 645: ......
Page 646: ......
Page 647: ......
Page 648: ......
Page 649: ......
Page 650: ......
Page 651: ......
Page 652: ......
Page 653: ......
Page 654: ......
Page 655: ......
Page 656: ......
Page 657: ......
Page 658: ......